“The sawmill industry experienced strong cut-throat competition between 2008 and 2018,” reports Wolf-Christian Küspert, owner and Managing Director of the GELO Sawmill in Weißenstadt, Upper Franconia. “About 30% of the timber companies disappeared from the market, and those that managed to survive lost a fair amount of ground. This also created an enormous investment backlog in the industry, which is only now being gradually cleared.” Küspert took over the family business from his father in 2003. The company was founded as a sawmill in 1898. With around 600,000 cubic metres cut annually, it is now one of the largest wood processors in Germany and part of a state-of-the-art wood processing industrial site. “We provide different finishing steps on site, so our customers get everything from a single source,” says the Managing Director.
In 2011, the company founded the WUN Bioenergie GmbH in Weißenstadt together with the Wunsiedel Public Utilities (SWW). With its attached biomass CHP, the subsidiary produces energy from renewable and, above all, regional sources. No waste is produced at GELO because the trees are entirely recycled: Wood chips generated during production end up in the pulp industry. The sawdust is pressed into pellets that provide electricity and sustainable heat for regional households.
“We have constantly expanded the Weißenstadt site,” says Küspert. “However, we reached our limits in terms of space.”
The logical solution for continued growth was a new site – an ideal location was found in Wunsiedel, just a few kilometres away, and the new energy park there soon hosted a CHP and a pellets facility. The wood processing company built the GELO sawmill in the energy park – probably one of the few German greenfield projects constructed in recent years.
The smell of freshly sawn wood is in the air. Wolf-Christian Küspert points to the new hall. “We have built the world’s most modern small-diameter timber sawmill here,” he says. Small-diameter wood is an excellent timber with firmly intergrown branches. With this project, the company also supports the increasing amount of forest conversion, which is occurring because climate change is causing older trees to die earlier and regrowing trees have to be felled more quickly. “The wood has a top diameter of about 25 centimetres or less,” Küspert explains. “Small-diameter wood always means a lot of waste wood, and that’s because the smaller the diameter, the higher the percentage of waste wood when we saw out a rectangular cross-section.” The sawmill in Wunsiedel processes mainly spruce – around 350,000 cubic metres per year.
Efficient processing of waste wood
To prepare the sawdust and wood chips for pellet production, GELO Timber relies on Vecoplan – as it has done for years in Weißenstadt. Vecoplan, the specialist for processing residual materials, is headquartered in Bad Marienberg in the Westerwald region. The company develops plants to shred, convey, separate, and store wood, biomass, plastics, paper and household & commercial waste. “Our tasks include consultancy, planning and finding solutions. We provide integrated project management, including installation, commissioning and comprehensive service,” explains Michael Mützel, Regional Sales Manager in the Wood I Biomass Division at Vecoplan. Wolf-Christian Küspert has known him for a long time through joint projects. The Managing Director has known Vecoplan for even longer: “Even my father and grandfather relied on the reliability of Vecoplan machines and the company’s competence. I grew up with that name. Here, the old German saying is: “Cobbler, stick to your last.”
Vecoplan was involved in the project from the very beginning. “We received the order in January 2020,” says Michael Mützel. “We accompanied the planning phase and were able to build our facilities on the greenfield site during the new construction.” The delivery date was in the summer of 2020, and installation and commissioning took place in November.
Wood chopped into small pieces
Motor noise fills the hall. Vecoplan expert Mützel points to the equipment installed by the Vecoplan team. From the saw line, sawdust and chips fall through the floor of the saw hall onto a long conveyor belt. The conveyor technology transports the material to a star screen to separate excess lengths. The matching waste wood falls onto another conveyor belt. The screened excess lengths and offcuts from the board sorting are transported to the drum chipper via belts and vibrating conveyors. These feed the material to be processed horizontally to the machine. Vecoplan technicians adapted the chipper to match the sawmill’s tasks and achieved a homogeneous and high-quality result.
“Our series is extremely compact,” says Mützel. “The shredding principle reduces the waste wood to a chipping length of about ten millimetres to be fed directly to the drying process in the pellet plant opposite.”
The chips produced by the chipper are then fed back onto the long conveyor belt under the saw line. A chain conveyor takes the waste wood, which has been freed from excess lengths, out of the hall together with the material rated as good by the star screen and transfers it to an approximately 40 metrelong VRF pipe conveyor in the direction of the pellet mill.
So that nothing is lost
“This series consumes about half as much electricity as similar conveyor belt systems,” Mützel reports. The VRF transports the material across the yard to the storage boxes and a screening station. To ensure that nothing is lost, the tubular system completely encloses the material so that neither wind nor storm can blow it away. The conveyor belt in this series passes through a tube; it does not run on rollers as in conventional conveyors. Since an air cushion supports the belt, only minor friction losses occur during operation. It also runs quietly, which makes for a more pleasant atmosphere on the premises.
Each drive station is equipped with two scrapers. Users can adjust the front head scraper and the carbide scraper from outside the machine. The components can be re-tensioned quickly and easily with a ratchet. The front head scraper is flexible but strong enough to remove extraneous materials from the belt. The carbide scraper is more thorough and prevents resin, for example, from sticking to the belt. These scrapers reduce maintenance times, increase equipment availability, and reduce material carry-over. The system conveys the material at a maximum of 2.5 metres per second. Another Vecobelt, approximately 80 metres in length, carries the waste wood from the screening station to the pellet plant.
An optimal location
“The transport routes here are short and energy-saving so that we can save several thousand truck trips a year,” says Küspert. The pellets are not only sold regionally; they are also supplied to various wood pellet gasifiers operated by the Stadtwerke Wunsiedel, GELO and other partners. The electricity generated is fed into the SWW grid. The heat supplies local networks in neighbouring districts, and the power plant also transfers its waste heat to the pellet plant to dry the chips.
Küspert is certain: “A project this big can only succeed with the right partners.And to reduce the complexity, I have to be able to rely on them. With a partner like Vecoplan, I know that things will run smoothly. And if things don’t work out, their experts know exactly what to do.” The time frame of the project was tight. Covid-19’s entry restrictions delayed the work of the installation crews from Finland and Portugal. Still, the wood processing company was finally able to start its regular operations at the end of February 2021. And just three months later, the company was already running at a stable 80% of its total capacity.
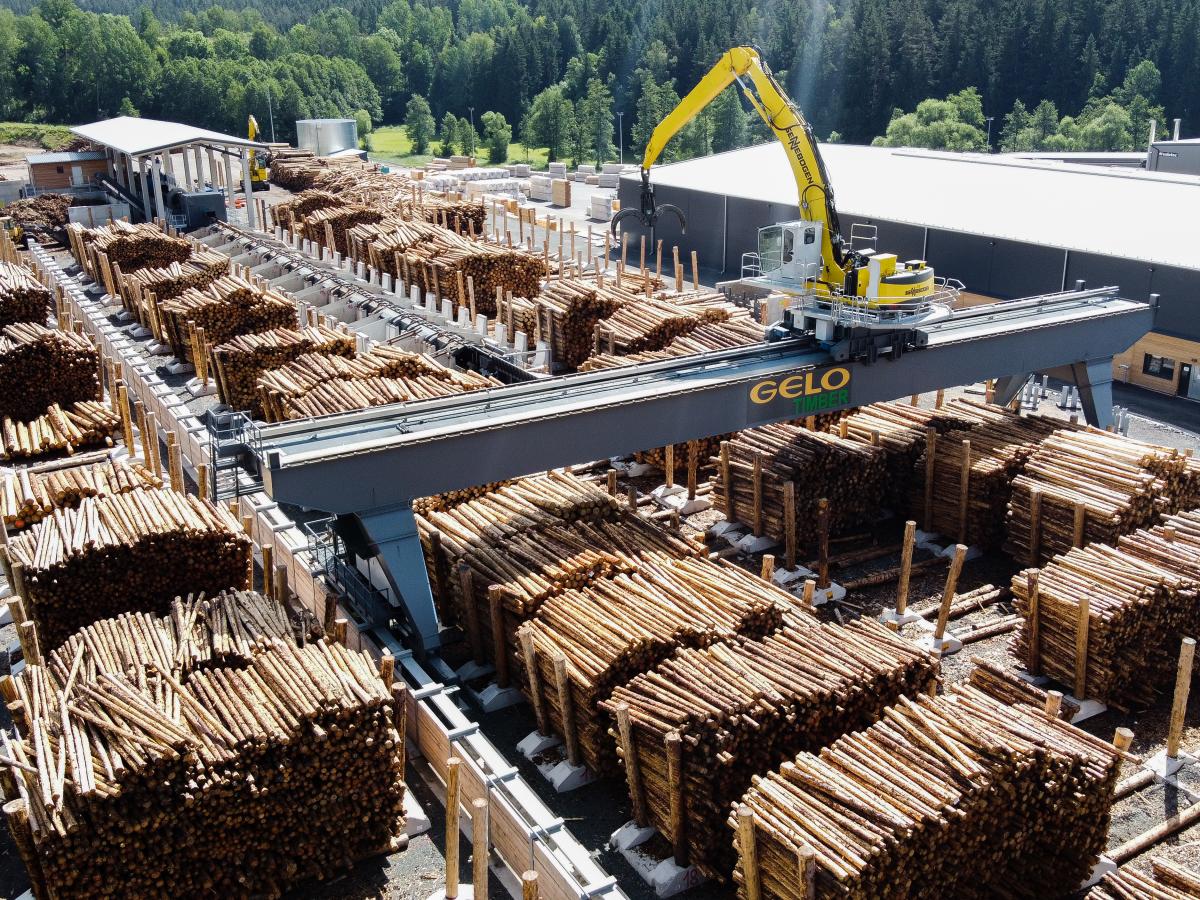
GELO Timber has built the world’s most modern, small-dimensioned wood sawmill in Wunsiedel in the Fichtel Mountains.
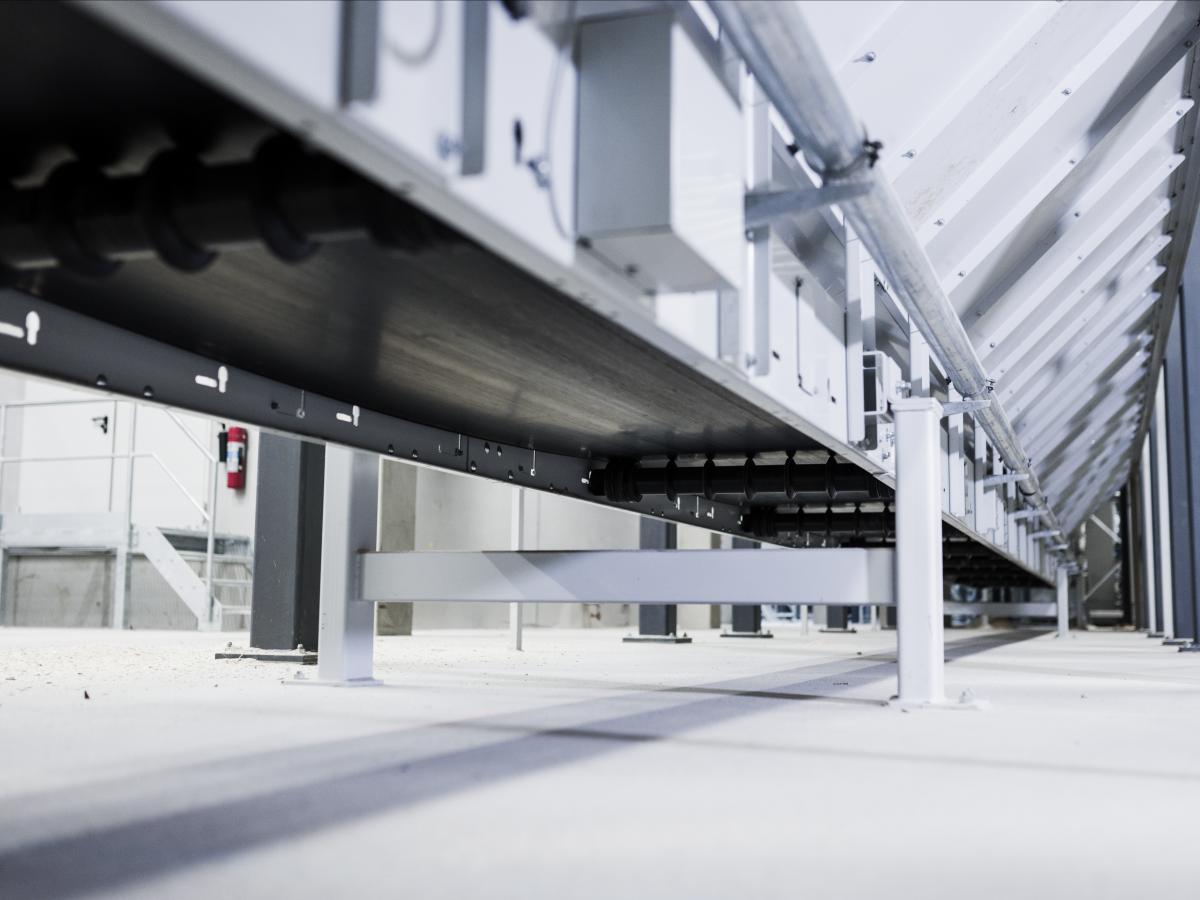
The waste wood falls directly from the sawmill onto the conveyor system, ready for the next stage of pellet production.
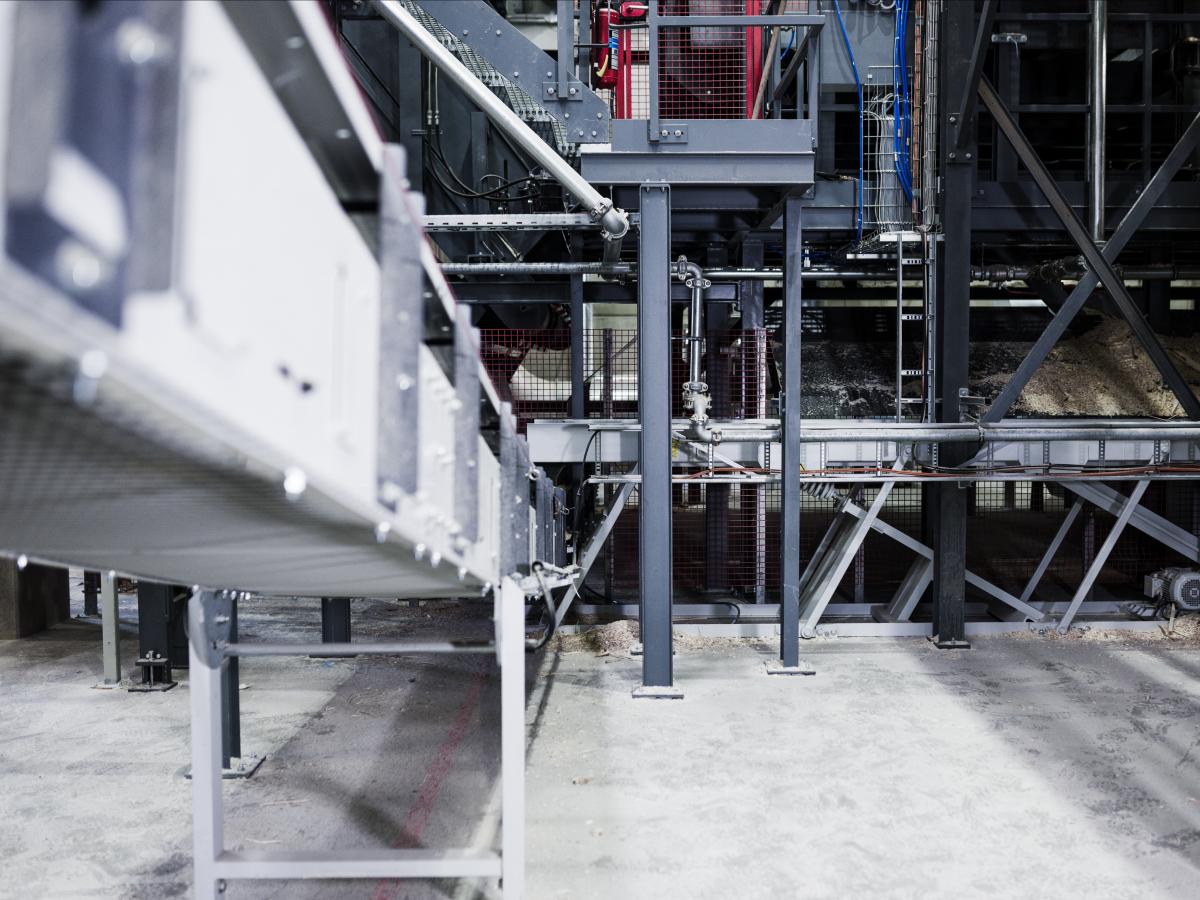
The conveyor system transports the material to the individual stations.
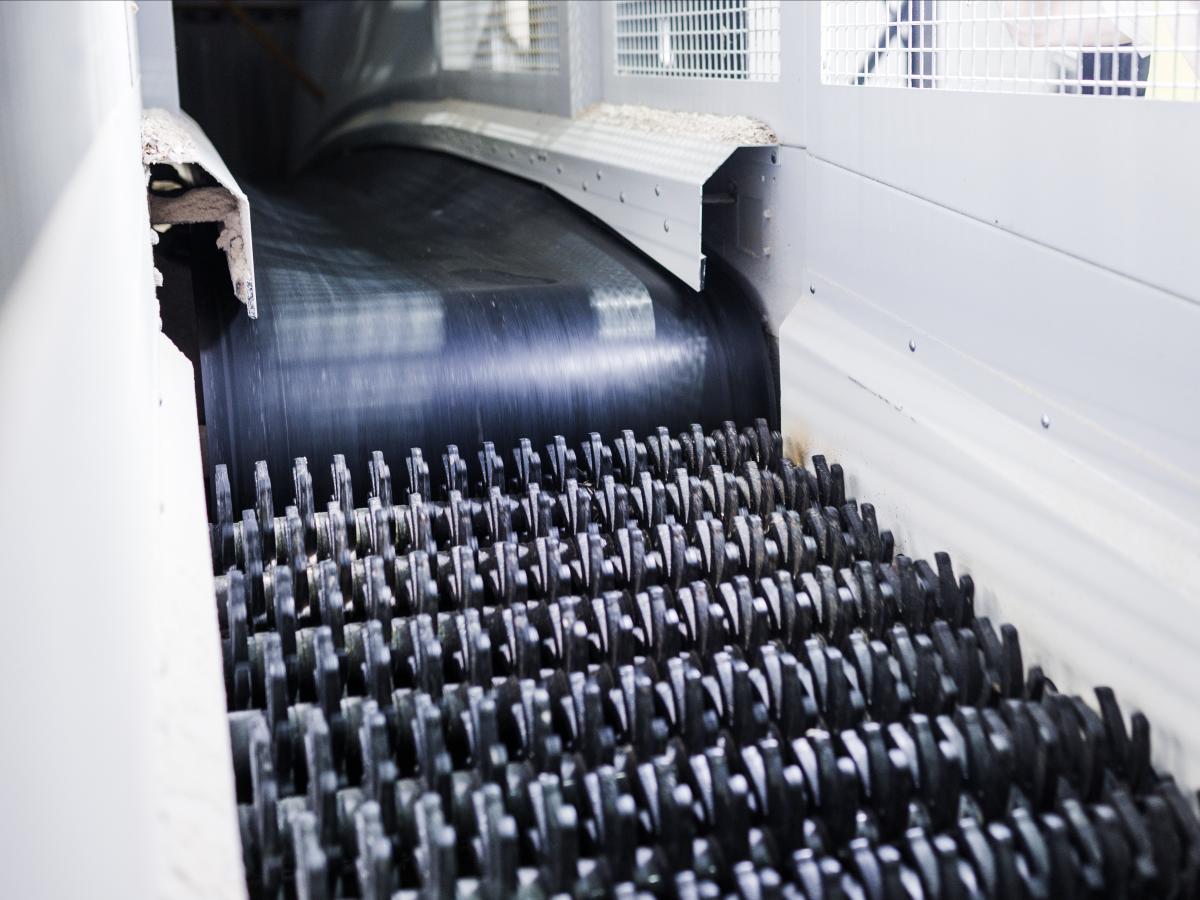
The star screening machine separates excess lengths from the material.
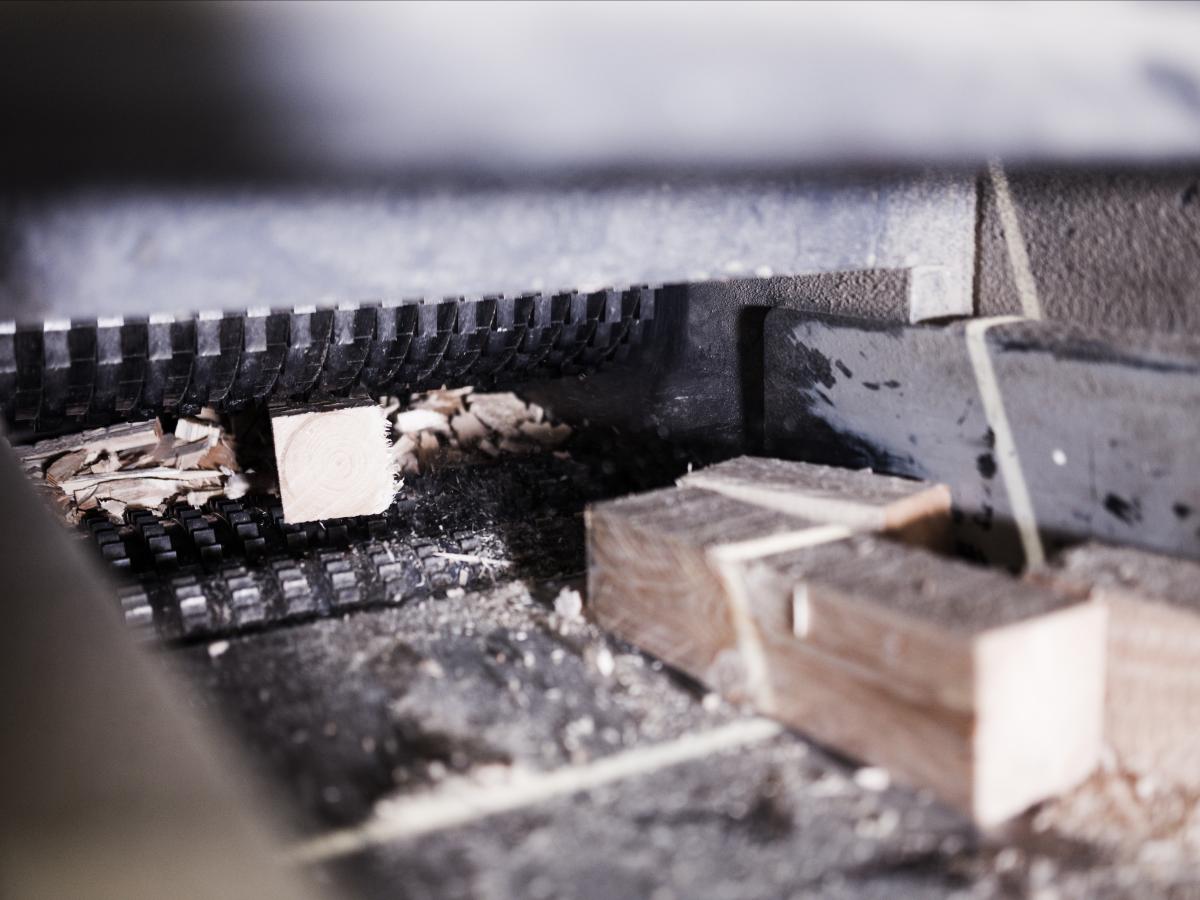
The screened excess lengths and offcuts from the board sorting are transported to the drum chipper via belts and vibrating conveyors.
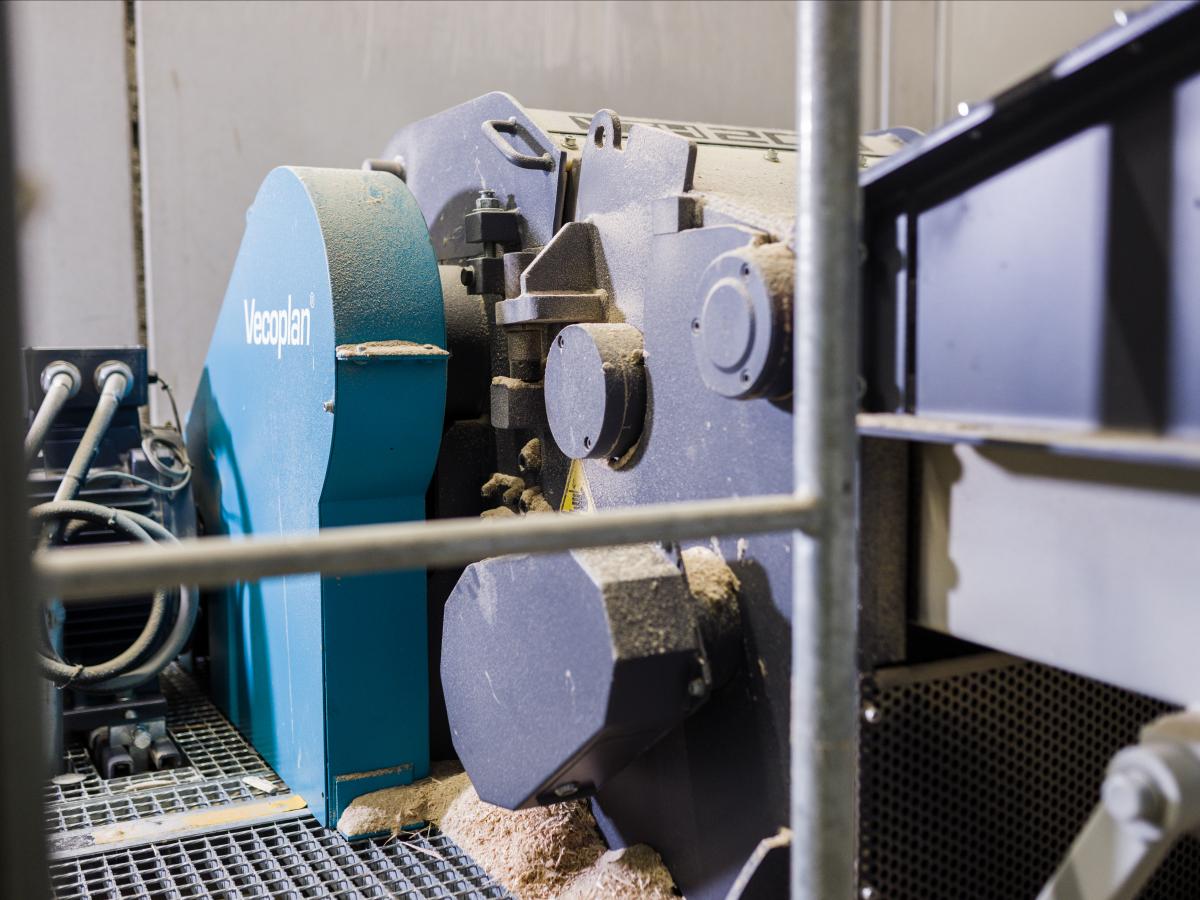
The drum chipper shreds the resulting waste wood to dryer-capable chip size.
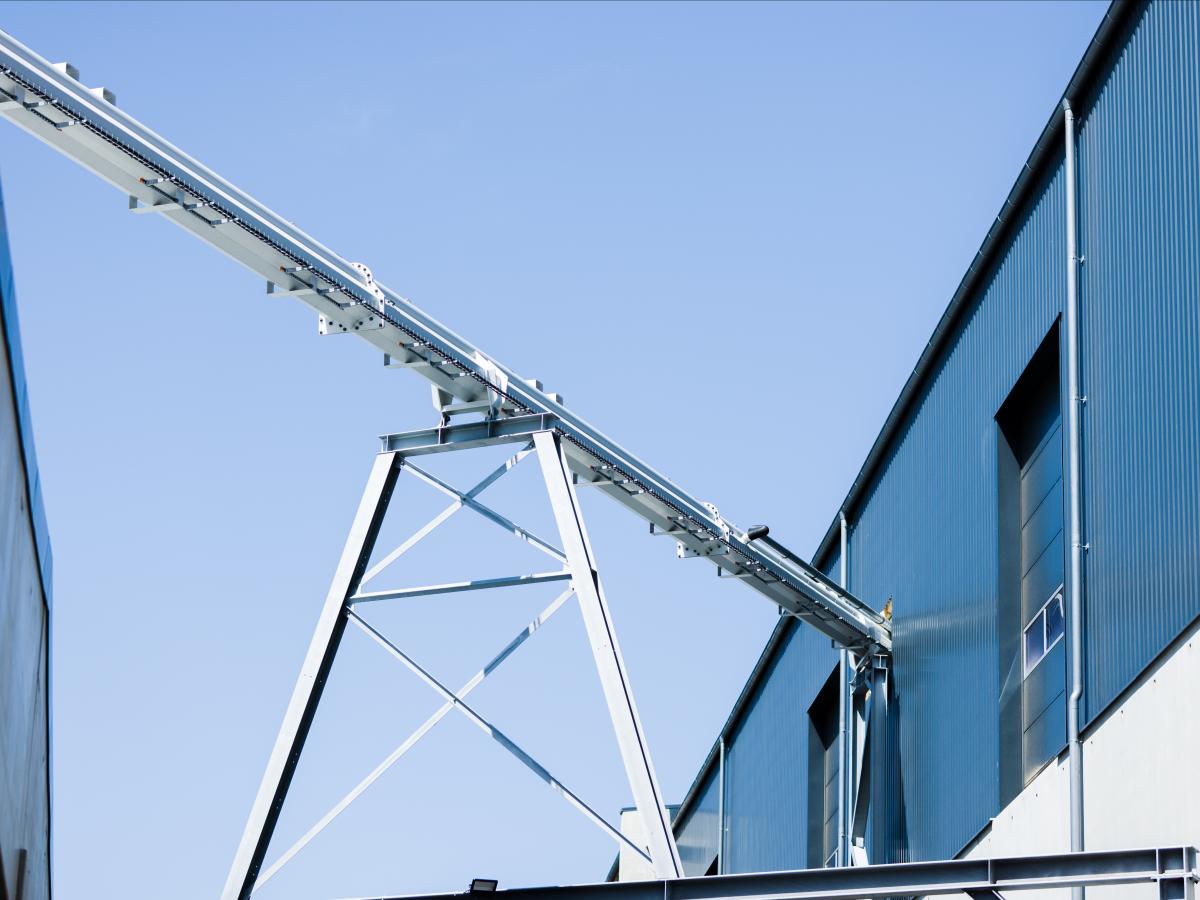
The Vecobelt transports the material across the yard to the storage boxes and the screening station and then to pellet processing.
Managing Director and Investor Wolf-Christian Küspert (left) with Michael Mützel from Vecoplan