“Robust and sophisticated – you can rely on our universal genius,” enthuses Martina Schmidt, Head of Recycling and Waste at Vecoplan AG. The company is one of the leading suppliers of machinery and equipment for the processing of primary and secondary raw materials for thermal and material recycling. “The VAZ 1700, 2000 and 2500 versions can tackle an extensive range of completely different materials,” she promises. That’s why the Vecoplan development team gave this shredder series a modular basis – also the outstanding feature of the new industrial design. Customers have a wide range of machine configuration options. They can adapt components such as rotors, cutting tips, counter knives, screens and drives to match the task at hand. The right choices and the relevant combinations are critical to the performance and quality of the shredding process. “One indicator is the throughput rate,” says Martina Schmidt. It ranges from 2,000 to 25,000 kg. per hour.
U, V or W? The right rotor is ready for action
Users can choose between various rotor versions, depending on the materials to be shredded. The aim is always to achieve maximum cutting performance and high throughput. The result is a homogeneous output quality with very little fine dust and minimum grain variance. “In this way, we effortlessly meet the constant, high-quality output requirements demanded by versatile applications and the best possible value creation,” explains Vecoplan expert Schmidt. All our machine versions are available for the different rotor lengths of 1,700, 2,000 and 2,500 millimetres.
“We always emphasise a small cutting gap between the rotor and the counter knives,” describes Schmidt. This is ensured by the simple external adjustment of both the first and (optionally) the second counter knife.
Vecoplan has significantly enlarged the material intake shredding chamber. “The user can also feed in closed bales,” says Schmidt. The machine is also equipped with a frequency-controlled ram, the speed of which can be infinitely adjusted. High throughput is thus guaranteed, even with challenging or very light input materials. A hydraulically operated swivelling screen with variable screen elements is also available. The customer can adjust these elements to the required output grain size.
Smooth handling
“We equipped the new machine with large maintenance doors and a bottom flap,” Schmidt reports. “This enables us to give service personnel effortless access.” For example, all maintenance on the rotor knives, counter knives and screen, such as changing, resetting or adjusting work, can be carried out by the personnel in a time- and cost-optimised manner – and above all, in an ergonomically comfortable, upright position. This is an unbeatable symbiosis of established know-how and features that will shape the future. The Vecoplan developers have optimised the new VAZ in such a way that maintenance times and costs are minimised. However, the new generation also includes proven features, and Vecoplan has adopted automatic extraneous material detection elements. Extraneous materials can be removed quickly and conveniently at the hydraulic bottom flap. Downtimes are drastically reduced. The well-proven “Flipper” machine breakage protection system in the VAZ machine prevents damage when extraneous materials are fed into the machine. The sensitive overload control reacts to impacts caused by these materials, protecting the shredder from possible severe damage.
Powerful drive
The shredder is equipped with the HiTorc drive, which has a high start-up power and powerful torque. The patented system is characterised by high energy efficiency. “Our HiTorc is the Tesla among drives,” says Martina Schmidt. It has no mechanical components like belts, gear wheels, flywheels or clutches, making the shredder much more robust. A single unscheduled plant stoppage caused by a broken shaft, burnt overload clutch, or defective gear is enough to justify using a HiTorc drive, which significantly reduces maintenance work and downtime. “We recommend this dynamic, powerful start-up and high-torque series of machines, especially to those customers who require continuous operation.”
The HiTorc drive is considerably more efficient than systems with gears. The absence of mechanical drive elements alone accounts for about 15%, making the synchronous motor very efficient, especially in the partial load range. It consumes only about 10% of the energy required by a comparable, asynchronous motor when idling. Operating situations like this often occur with inhomogeneous materials and irregular input. The overall energy consumption for the user is also reduced – because the HiTorc is also very dynamic, it can start up fast even under load, i.e., with a full engine room.
Digitally advanced
The new shredder is equipped with the Vecoplan Smart Center (VSC). This powerful digitalisation concept offers a modern communication interface between Vecoplan and the customer with the VSC.connect system. The user can access services such as document management and remote service. The integrated, intuitive VSC.control operating panel serves as a communication medium for the machine’s control system and a live link to the Vecoplan technicians.
Vecoplan has designed the machine operation to be user-oriented and equipped it with valuable features, such as a dashboard that provides the operator with an overview of all the relevant values and current messages. A message history also enables conclusions to be drawn and ensures rapid troubleshooting, while a data recorder notes all values. Integrating a camera also enables images to be transmitted from inside the machine – for example, for rapid troubleshooting without needing a Vecoplan service technician to be on site.
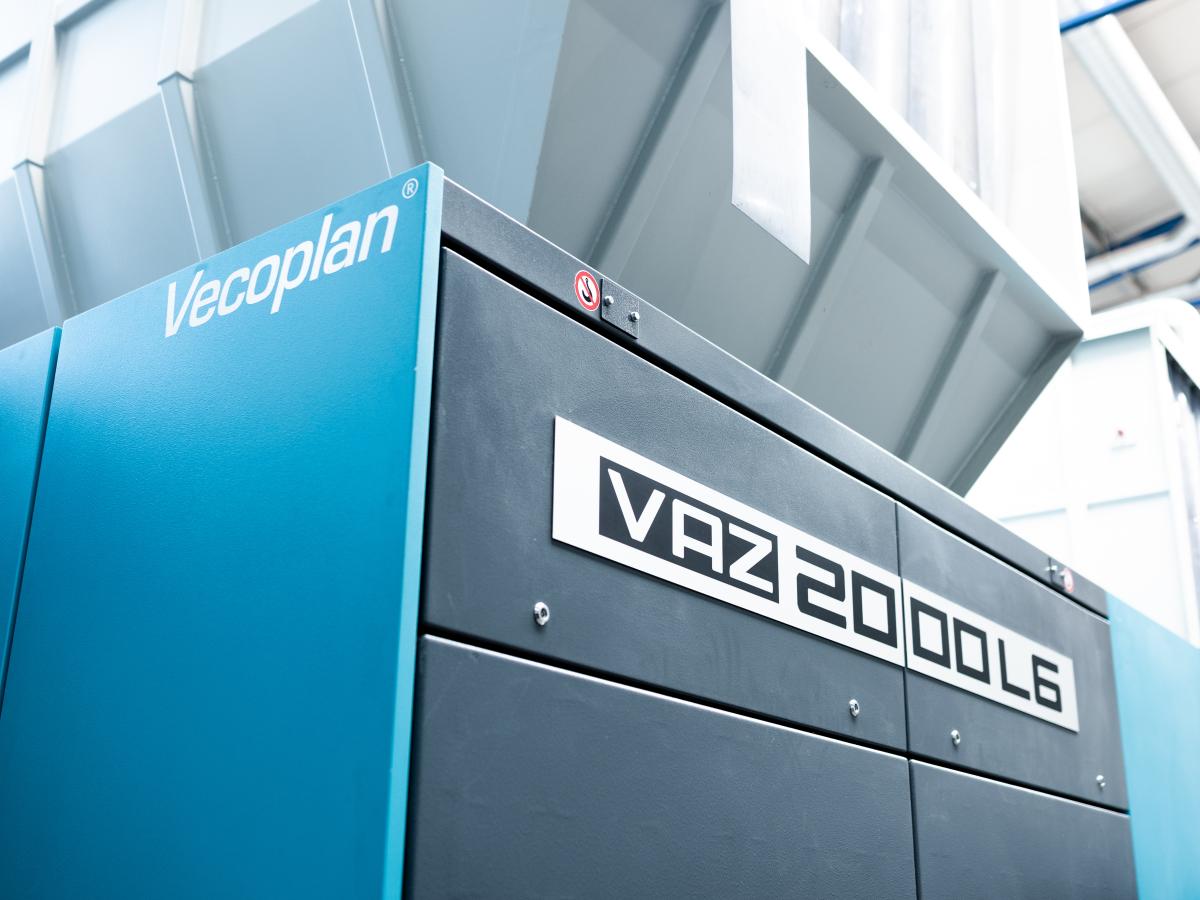
The new VAZ combines attractive technical features with functional modern design.
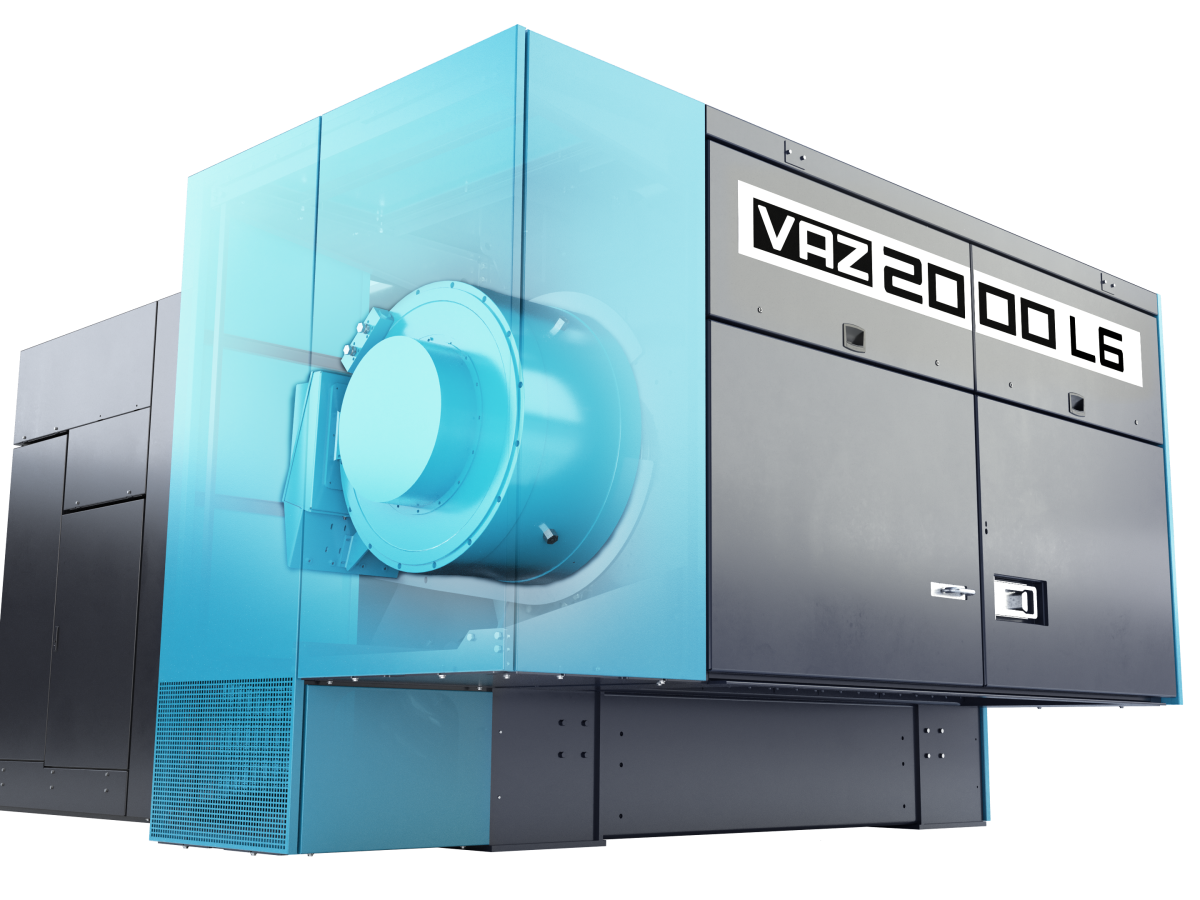
The HiTorc drive is characterized by high energy efficiency. It enables the new VAZ to be used in continuous operation.
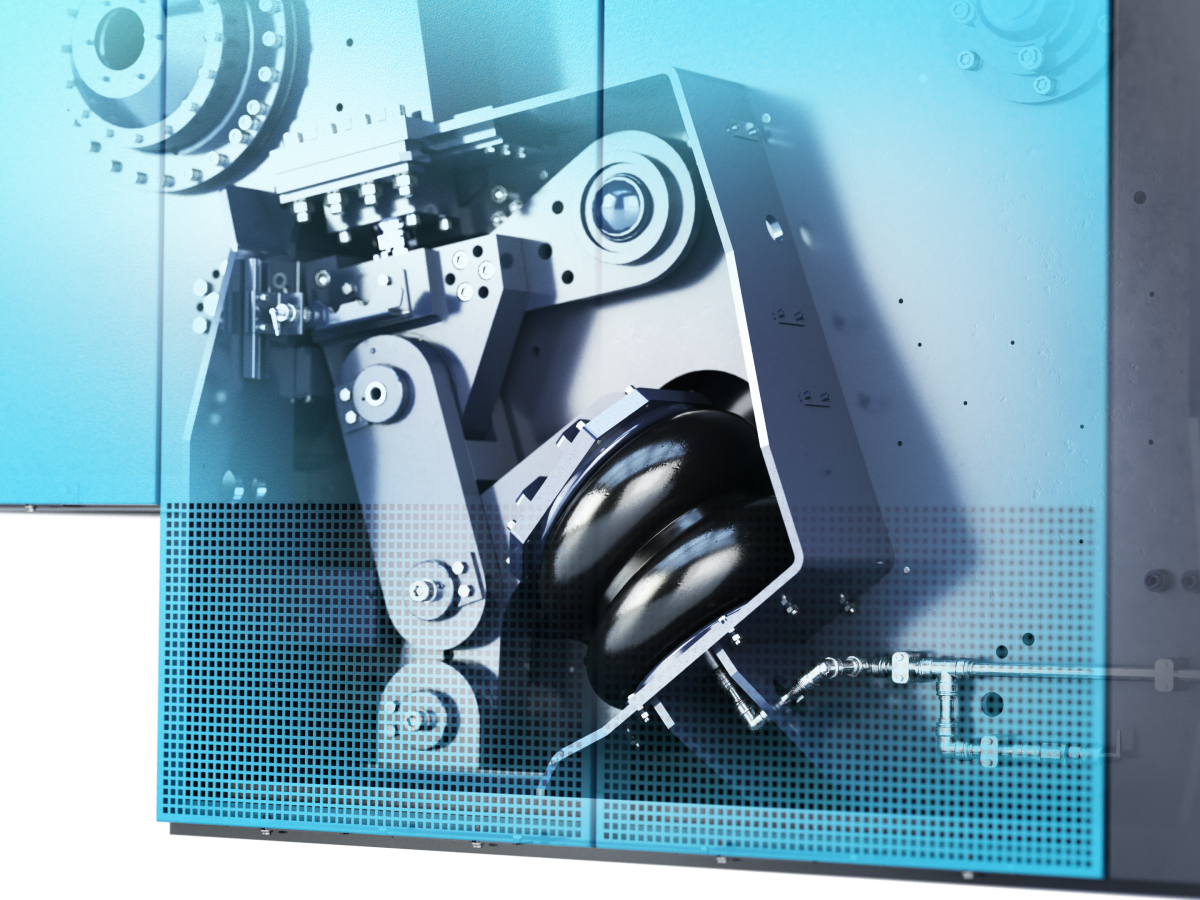
The "Flipper" machine breakage protection system from Vecoplan prevents damage when feeding materials contaminated with impurities.
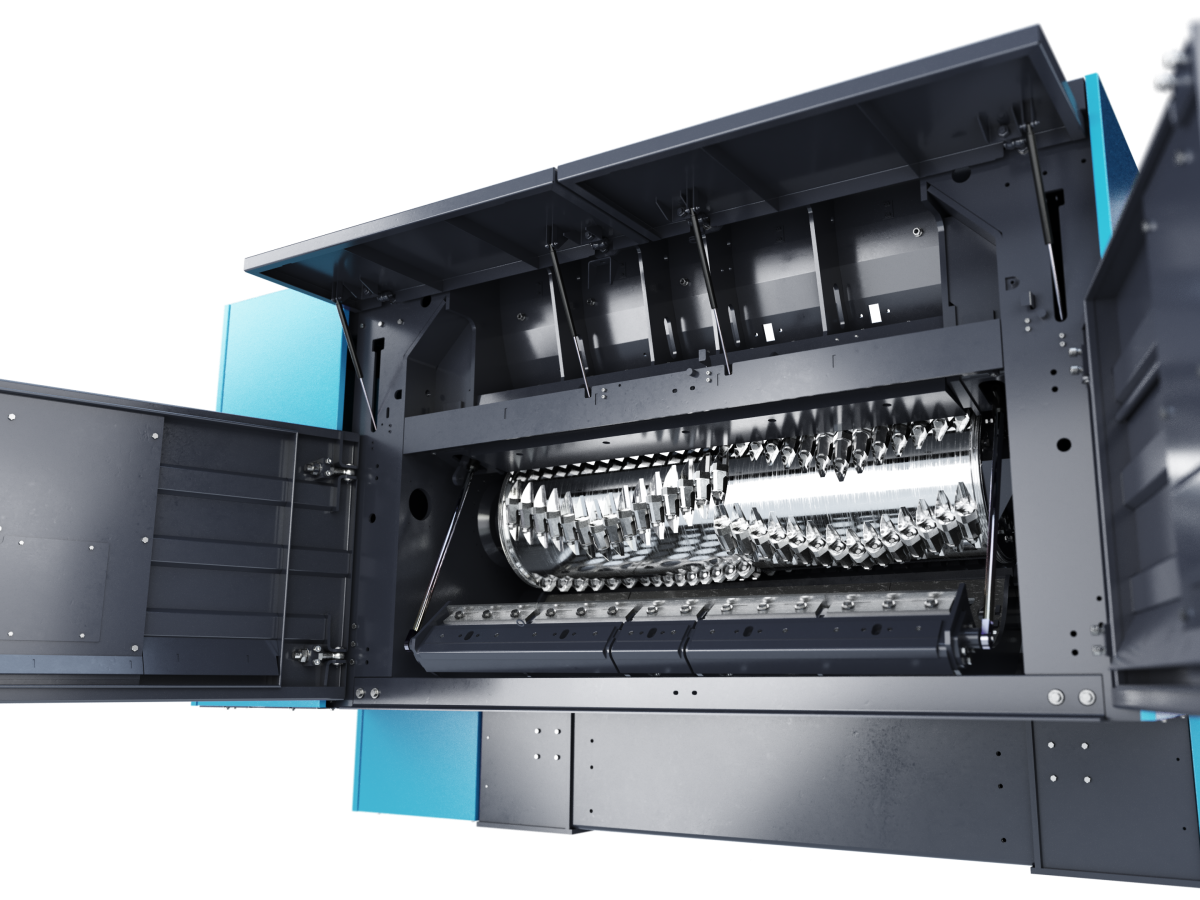
Large doors and a hydraulically lowerable screen allow good accessibility for maintenance work.