When a sawmill starts cutting timber, it doesn’t only produce valuable sawn wood; a lot of wastewood is also left over after the cutting process has ended – and this by-product can quickly become a major problem if it’s not disposed of efficiently. If chips, bark, and wood chips are allowed to accumulate, production downtime looms large. That’s why Schaffer Holz GmbH has integrated a customized solution right from the start when building its new sawmill in Styria, Austria. Vecoplan state-of-the-art conveying, shredding and screening technology efficiently controls and economically utilises the entire waste wood flow.
Schaffer Holz GmbH is one of the most renowned softwood sawmills in Austria. The company specialises in the processing of thick timber, mainly processing large logs measuring 45 cm in diameter. The window and furniture industries are among its customers, as well as manufacturers of soundboards and tonewoods for pianos. A large proportion of the production is exported abroad. To avoid jeopardising this value chain, the new sawmill had to be designed in such a way that the by-products could be reliably processed from the start.
This is a board: 35% waste wood from solid logs
The challenge involved several aspects: The high proportion of waste wood of around 35%, which is produced from an annual cutting volume of 150,000 solid cubic meters, had to be taken into account, as did the narrow and confined layout of the plant on site. The sawmill stretches along a stream and is bordered by railroad tracks on the opposite side, which extends the length of the facility. The entire disposal technology had to fit into the special architecture without compromising on performance and reliability. So Schaffer opted for a complete solution from Vecoplan, consisting of conveying, shredding and screening technology optimally adapted to the complex system. The exact separation of wood chips and sawdust is particularly important to the company, as the quality of the end product influences the sales price. "The quality of the wood chips has a direct influence on the price in our region. If we exceed the minimum requirements, it has a positive effect on revenue. That's why it was crucial for us that the Vecoplan system would meet our high quality requirements," explains Lambert Sattler, authorized signatory at Schaffer Holz.
Precise separation, maximum utilisation
Vecoplan has developed a customised system for Schaffer – and it matches the company’s requirements perfectly. The solution for waste wood disposal includes conveyor technology, a powerful drum chipper and an intelligent screening system with a vibrating separator. The wood residues are first transported via vibrating screens and conveyor systems to a powerful drum chipper, which produces high-quality wood chips. These chips are recycled in the paper industry. Using a drag chain conveyor, the wood chips and sawdust are fed to a vibro screen to separate excess lengths which then are fed back to the chipper via a conveyor belt. The sawdust and wood chips, now freed of excess lengths, are then transferred to a VRF 500 P pipe belt conveyor by another drag chain conveyor. The drag chain conveyors form a closed system and ensure a continuous material flow. They’re combined with the VVR vibrating conveyor, which regulates the material feed by means of a uniform conveying flow. The VRF pipe belt conveyor system then transfers the fine wood chips to the VSS 6000 vibrating separator above the sawdust boxes. The VRF was specially developed for the clean and quiet transport of bulk goods over long distances and Schaffer uses it for an 80-meter-long route across the entire factory yard. The closed system ensures that the material is conveyed very cleanly and safely. Another special feature of the system is the subsequent material separation by the vibrating separator directly above the storage box. The two-line separation takes place just before discharge, so wood chips and sawdust can be precisely separated and optimally utilised. The Vecoplan system processes up to 18 cubic meters of waste wood per hour – a level of performance that's crucial for smooth sawmill operation
Tailor-made technology in the tightest of spaces
The implementation of this demanding project was an exciting challenge for both Schaffer and Vecoplan. One of the biggest hurdles was the integration of the waste wood disposal into the existing production processes and the cooperation with several suppliers. "Due to the challenging design of the sawmill, it was important to develop a compact but powerful solution," says Helmut Bammer, Area Sales Manager at Vecoplan. Thanks to Vecoplan’s customized solutions, all of the customer's specific requirements could be met, from reinforced vibrating feeders to individually adapted conveyor elements. Following a one-year planning phase, the installation was started in March 2024. The system was finally commissioned in July and has been producing impressive results ever since. "We’re very happy that we decided to choose Vecoplan. The system runs reliably, the quality of the wood chips is good and the screens allow us to make targeted improvements," says Lambert Sattler.
The result? A reliable and sustainable solution
The effects on the company’s operations are clearly noticeable. The entire disposal process runs smoothly and the quality of the wood chips meets the highest standards. This in particular has a direct economic significance, as better sorting increases the market value of the by-products. Wood chips are sold to the paper and pulp industry, while sawdust is mainly used by pellet producers. Thanks to Vecoplan's robust and reliable technology, Schaffer's new sawmill can operate smoothly and with maximum efficiency. Lambert Sattler was particularly impressed by Vecoplan’s flexibility and customer orientation during implementation: "Vecoplan has given us a solution that is precisely tailored to our requirements. The combination of high conveying capacity, compact design and intelligent material separation convinced us completely. We’re very happy that we opted for this system."
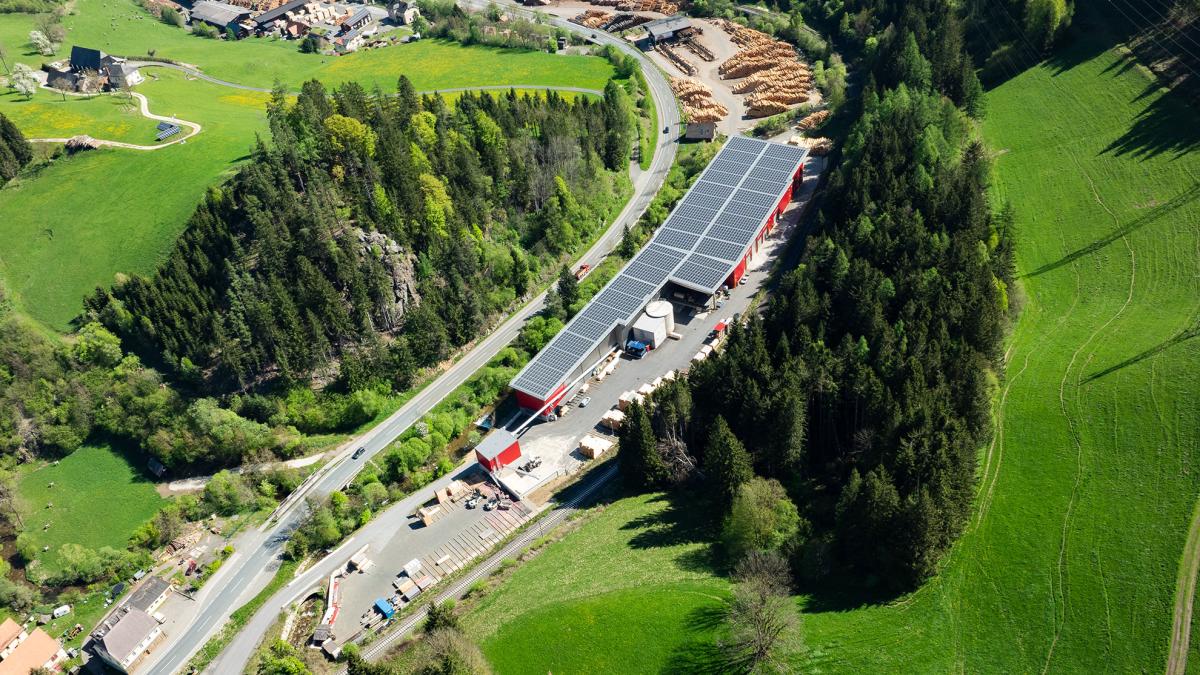
The constricted design of the sawmill necessitated very specific planning. The plant runs alongside a stream and is bordered on the opposite side by railway tracks.
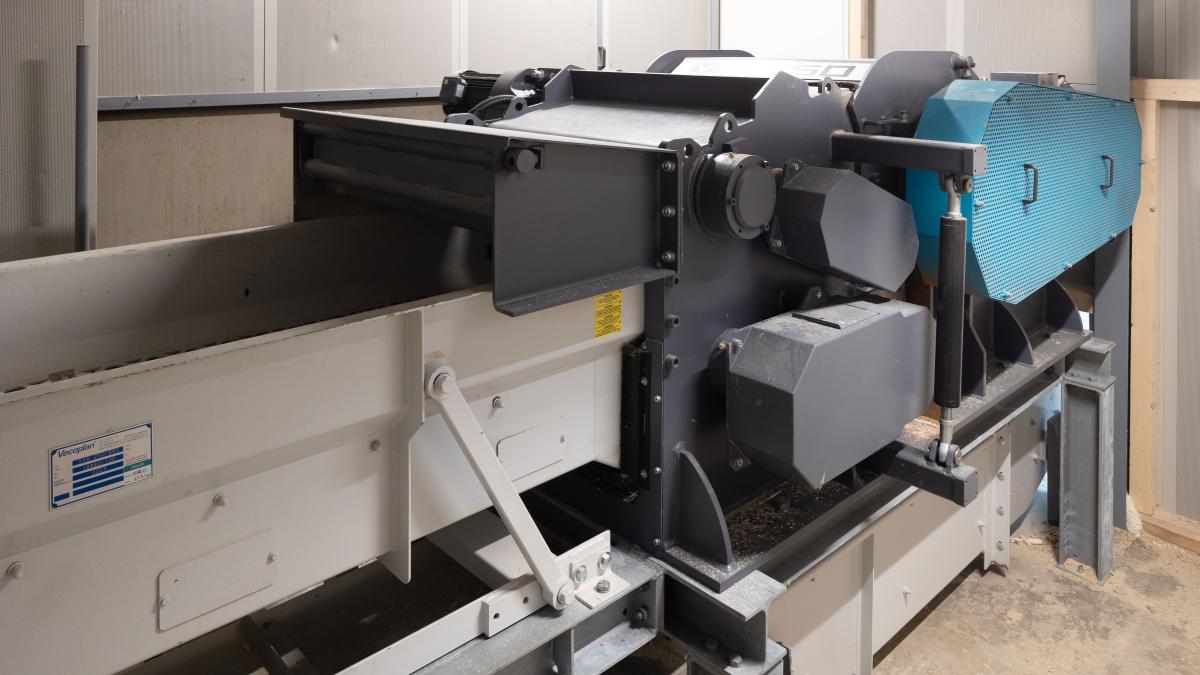
The Vecoplan VTH 250-850 drum chipper produces high-quality wood chips for downstream processing.
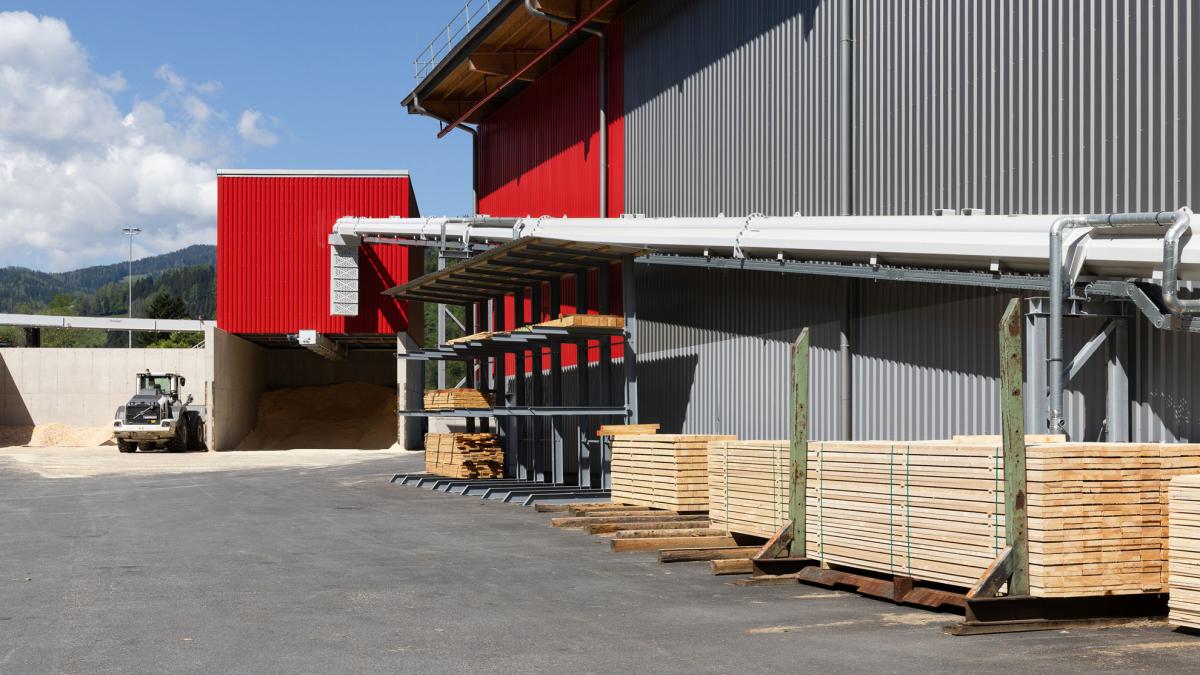
The VRF 500 P was specially developed for the clean and quiet transport of bulk materials over long distances and is used by Schaffer on an 80-meter route throughout the entire yard.
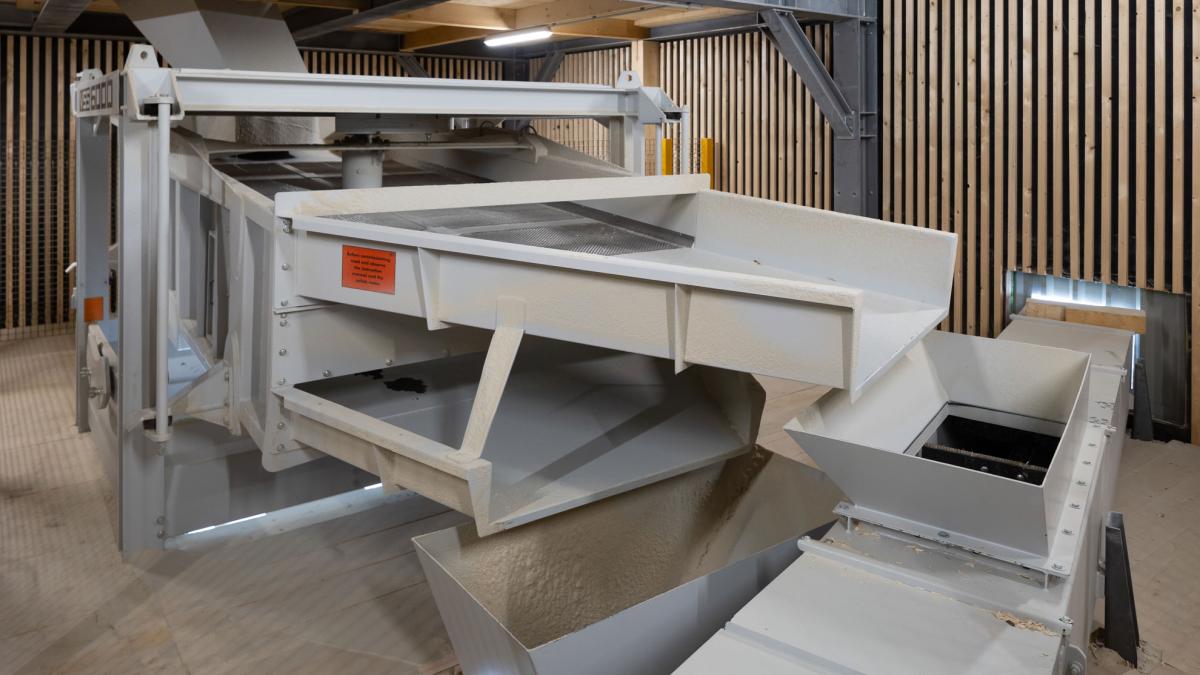
The intelligent screening system with the VSS 6000 vibrating separator ensures the effective screening of the wood chips.
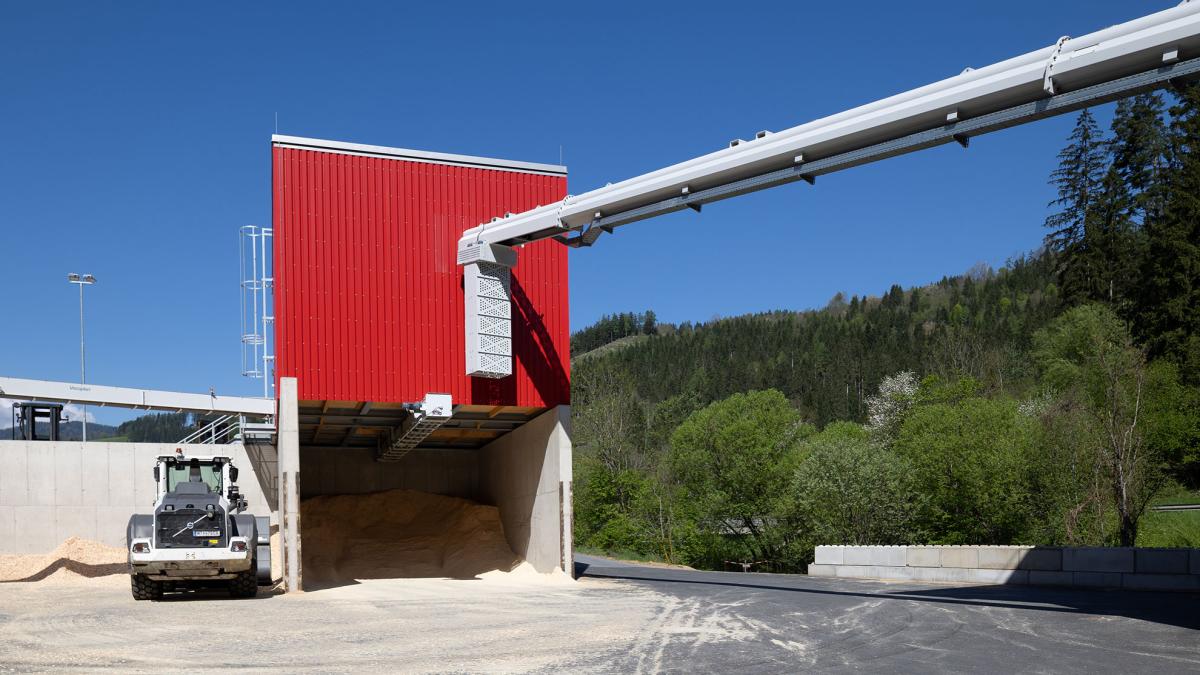
The fine wood chips are conveyed via the VRF 500 P pipe belt conveyor system to the VSS 6000 vibrating separator above the sawdust boxes.