Since 2017, YS Reclamation has invested heavily in new equipment to enhance the quality of their final plastic product. However, issues with the originally supplied primary shredder were restricting productivity and quality.
YS Reclamation process an input of 27 tonnes per day of post-consumer LDPE plastic film. Through a bespoke process, the recycler produces up to 25 tonnes per day of high-quality plastic pellets for use in the manufacture of a wide range of plastic products. Five grades of pellet are produced and the waste ‘fines’ are sent to an energy-from-waste plant, resulting in zero waste process.
The received plastic waste is initially assessed and graded at a separately located warehouse facility. To ensure the correct grade of pellets is produced, further grading occurs at the Warrington plant prior to the material entering the process.
The baled plastic film passes through a guillotine press and onto a manual sorting line to remove any visible contamination such as baling wire or metal. The unbaled material then passes up an incline conveyor into the Vecoplan shredder.
After shredding, the <50mm plastic film passes through a washing plant to clean and remove materials of different densities (e.g., ceramic, glass and metal), before being granulated to <10mm. A hydrocyclone, using density separation, removes material such as PET film and trays, before the material is dried and extruded as plastic ready for reuse in making new PE film.
The shredder installed with the original plant proved unreliable and failed to produce the required quality of shred. During the first 8,000 hours of operation, YS Reclamation had experienced over 1,400 hours of downtime due to mechanical failures and other issues with the original shredder. The severity of the shredder problem led YS Reclamation to contact Vecoplan to assess the installation and identify possible improvements.
Vecoplan recommended the installation of a model VAZ 1700 L6 shredder, which would produce a better yield of product and improve productivity. The single-shaft VAZ model is specifically designed for recycling applications. The robust, powerful and energy-efficient design enables the universal use of the high-performance shredders of the VAZ series for a wide range of applications. By adapting the rotor design, the shredder achieves maximum throughput with a homogeneous output, even with challenging materials.
Due to the urgency of replacing the original poor-functioning shredder, YS Reclamation visited the Vecoplan stand at the K 2022 trade fair for plastics and rubber (Düsseldorf, German) to see the VAZ1700 shredder in action. Following the show, the shredder was shipped to the Warrington plant.
The VAZ 1700 L6 model has a rotor length of 1660mm, diameter of 640m and weighs approximately 20 tonnes. The control is mounted on springs on the side of the shredder for easy installation and access.
Since the installation, YS Reclamation has seen a significant improvement in productivity and product quality. The design of the Vecoplan shredder produces 40% less fines, which reduces the level of contamination in the extruder process; greatly improving the end product quality. The Vecoplan shredder is capable of shredding 4 tonnes per hour of baled plastic film. Which, when compared with the original shredder, means the Vecoplan shredder only operates for 30% of the time. The energy savings due to the reduced operating time were considerable, especially as the Vecoplan shredder stops when not processing unlike the original shredder.
Once installed and operational, YS Reclamation identified further advantages of the Vecoplan VAZ 1700 shredder, with a significant drop in the level of noise and vibration. Maintenance time was also reduced, with the internal design of the shredder enabling simpler and quicker replacement of worn parts such as blades, which has reduced the downtime for changing knives by 4-hours and the counter knives by 5-hours.
The engineering team at YS Reclamation were also impressed with the service response times from the UK-based service team. The Vecoplan shredder also benefits from having remote internet access allowing for online support and program changes remotely.
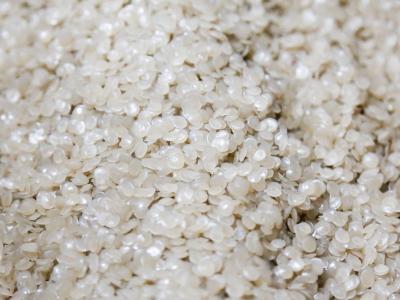
Replacing the old shredder with the Vecoplan VAZ1700 has dramatically changed the operating performance of our plant. The new shredder performs exactly as Vecoplan explained. Extended production downtime due to shredder issues is no longer an issue and we are producing a better-quality end product.