“The economic environment for wood processers in France is currently very unfavourable,” explains Christophe Lagarde. Together with his brother Richard, Christophe manages C2R, a wood processing company based in Saint-Junien in the French département of Haute-Vienne. The company employs five other people in maintenance, production and management. “One problem for us is the declining number of DIY stores, which means that sawmills are getting fewer orders. As a result, there is less residual wood, which we use for producing biomass fuel, and that makes it more expensive.” In addition, sales of modern wood stoves in France are rising steeply. This is increasing the demand for wood as a raw material for energy generation. “The situation in this market is similar to that for industrial wood. It’s difficult to obtain and transport enough raw material. In other words, not enough trees are being felled and processed.” Another problem is a shortage of qualified workers, which is leading to greater competition among companies that purchase wood for industrial use and fuel.
In 2008 the company C2R grew out of a partnership with Comptoirs des Bois de Brive (CBB), which buys, uses and markets structural timber, pulpwood and fuelwood. CBB is a subsidiary of the American Sylvamo Corporation, a producer of offset paper and pulp. C2R currently processes 130,000 metric tons of wood per year from sawmill by-products and forest products. CBB supplies the wood. “We have two business areas,” says Christophe Lagarde. “We supply products for the paper industry and we produce fuels for regional companies.”
Selection of a proven partner
C2R has been relying on Vecoplan for processing various wood products ever since it was founded. Headquartered in Bad Marienberg in the Westerwald region of Germany, Vecoplan develops plants that shred, convey, separate, and store wood, biomass, plastics, paper and household & commercial waste. “We advise our customers, plan the technology and find specific solutions together,” explains Bertrand Thiebold from Vecoplan France, the French subsidiary of Vecoplan AG. “We form teams of application engineers and sales staff to this end. Our tasks also include complete project management, assembly, commissioning and a comprehensive service programme.”
Vecoplan was able at the start to prevail over its competitors. It supplied two processing lines: one for wood chips for the paper industry and one for producing fuels from biomass. “Our expectations were fully met,” says C2R manager Lagarde. However, the company was forced to upgrade the processes at its site on account of increasing competition in purchasing. Lagarde: “On our two former lines, there were two tools for grinding the various basic products, but market trends meant that we couldn't process certain products, such as log purges, because of their size. In the current economic situation, we can no longer afford to do without them.” The decision-makers at C2R turned to Vecoplan for help, and thanks to a long-time partnership and many years of experience Vecoplan had the answer.
A viable solution
Wood residues processed by C2R include sawmill off-cuts, bark, pallets and forestry chips. In fuel production the requirements for the shredding process are especially rigorous. The fuel must not only have a stable moisture content in line with the customer’s specifications, it must also comply with the stipulated particle size.
C2R divides the production process into four phases: “First,” says manager Christophe Lagarde, “we dose the raw materials – for example, wood chips, bark and forest chips – to achieve the required moisture content and quality. In the second step we use a disc screen to separate pieces larger than 100 millimetres from the mass. This wood is passed to our new primary wood crusher in Vecoplan’s VVB series.” In order to calibrate the final product, that is to remove fine particles and pieces of excess length from the high-quality fractions, the material is screened out in a VSS vibrating separator. “This enables efficient sorting of the processed product into different particle sizes,” explains Bertrand Thiebold.
The VSS consists of inclined, circularly vibrating screen boxes which are independently suspended in a steel frame. The vibration has an ideal separating effect.
A colossal force for biomass production
The heart of the processing system is the VVB primary crusher. The solid steel rotor is notable for its enormous flywheel mass. C2R uses the primary crusher to match large throughput quantities to the given application. “An impurity content of less than 2% is no problem for this machine,” says Ralf Rosenkranz, head of application engineering at Vecoplan. The counter-knife unit and sieve basket swivel away automatically if extraneous material is detected. Once the impurities have been removed, the units return automatically to their operating position. With this system C2R can produce fuel in particle sizes from P45 to P100, compliant with DIN EN ISO 17225. The machine processes fresh bark with up to 60 percent water content, logs up to 400 millimetres in diameter, and pile caps up to 1,000 millimetres in diameter and 400 millimetres in length. It can be fed balled material, log yard residues, sawdust, short-cut wood waste, pre-crushed pallets and demolition wood. The crusher is ergonomically designed and easy to maintain. For maintenance the rotor hood and rear panel of the machine pivot downwards. Once folded down, the rear panel can serve as a maintenance platform, giving the operator quick access to the entire machine. A maintenance platform is also integrated into the rotor hood. The counter-knives extend hydraulically during maintenance.
Another feature of the machine is the VSC control panel. This modern unit lets users adjust the machine parameters and store their individual settings. It gives an overview of current values and messages, including the message history and data values. Additional services are accessible online. If a fault occurs in the system, it can usually be remedied by hotline in a short time without requiring a local visit by a Vecoplan technician. This saves a lot of time and money. “The hotline is an indispensable tool. It ensures high efficiency and was especially valuable during installation,” recalls Lagarde.
From France for France
The machine is currently operating in an eight-hour shift, five days per week. “The VVB meets our expectations in every respect,” says the manager. “We now have many more options when it comes to material procurement, because we can feed the machine all the raw material we purchase, which means whatever is being offered by wood suppliers. This is a real advantage for our business.” Lagarde is certain that the VVB was the right choice for his company – and that Vecoplan is the ideal partner.
This is significant for yet another reason. In 2023 Vecoplan founded a subsidiary in France in order to supply reliable local service to its French customers. Customers can now receive direct support from Vecoplan France. This facilitates communication within the company during the design and implementation of Vecoplan systems and reduces the number of interfaces. French-speaking experts are on hand to provide expert advice. “We can now communicate on a regular basis,” says Lagarde. “This helps us to get the most out of our systems in accordance with our ideas.”
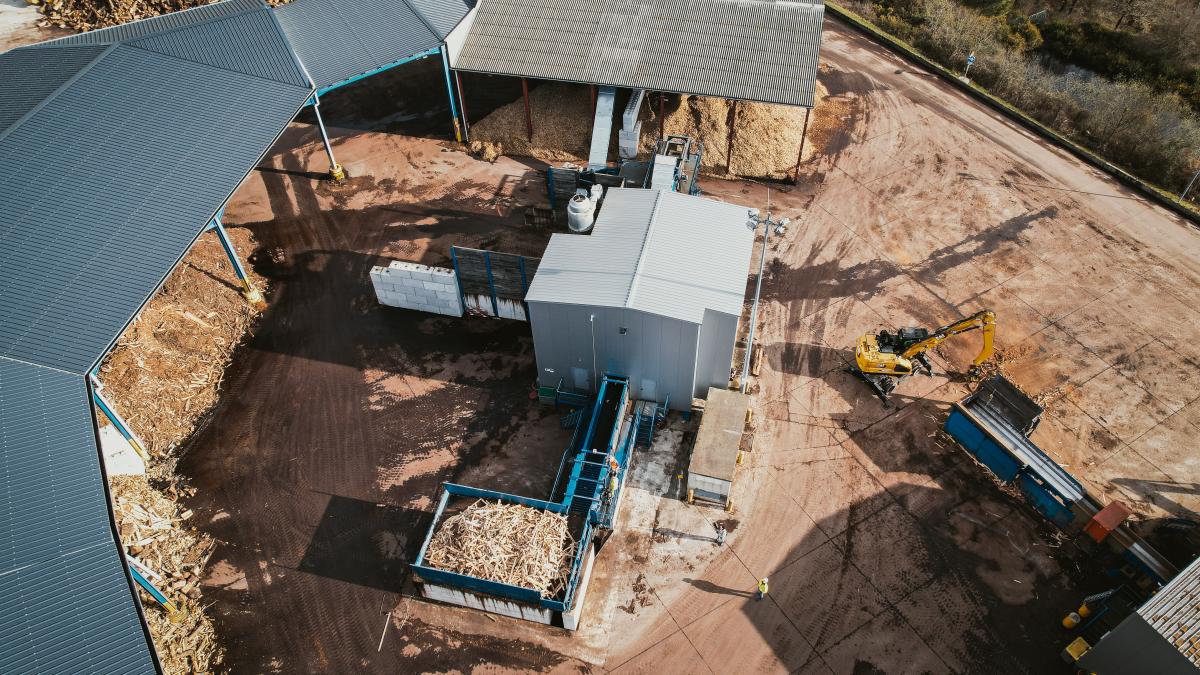
A view of the C2R premises with the two production lines.
With its new VVB primary crusher C2R can process a wide variety of materials in large quantities.
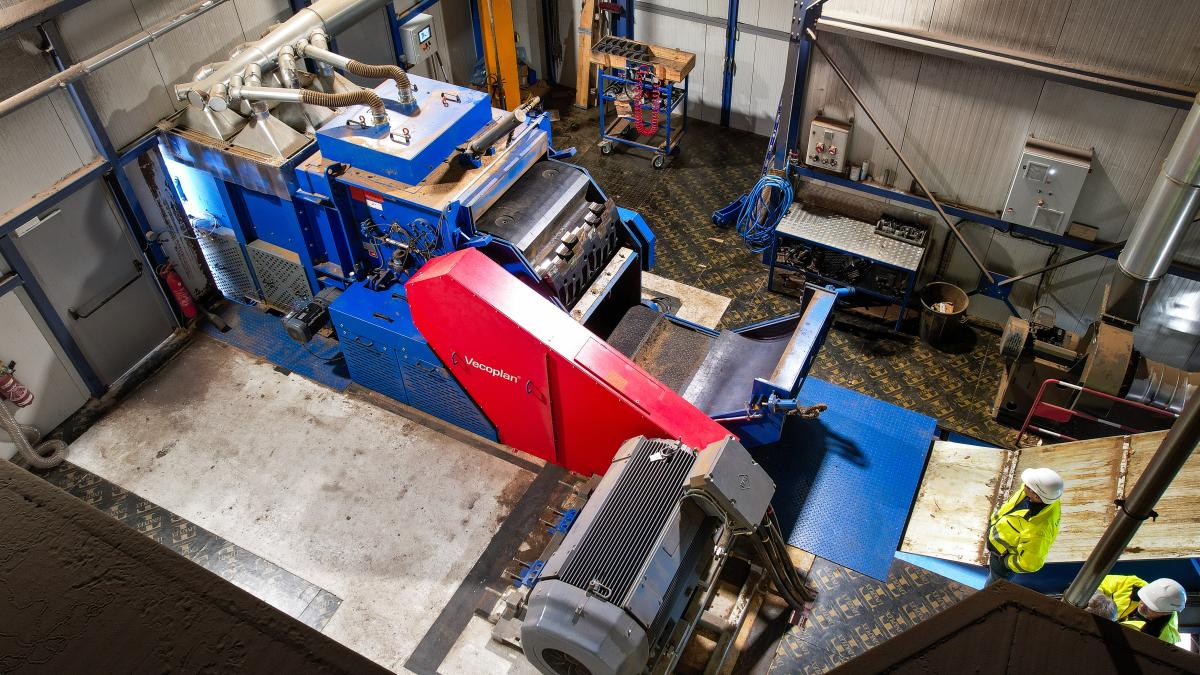
Material is fed to the system outdoors via a conveyor belt. The shredding itself takes place indoors for noise reduction.
The VVB primary crusher features a robust design. A service platform integrated in the panel opens at an ideal height for maintenance personnel.
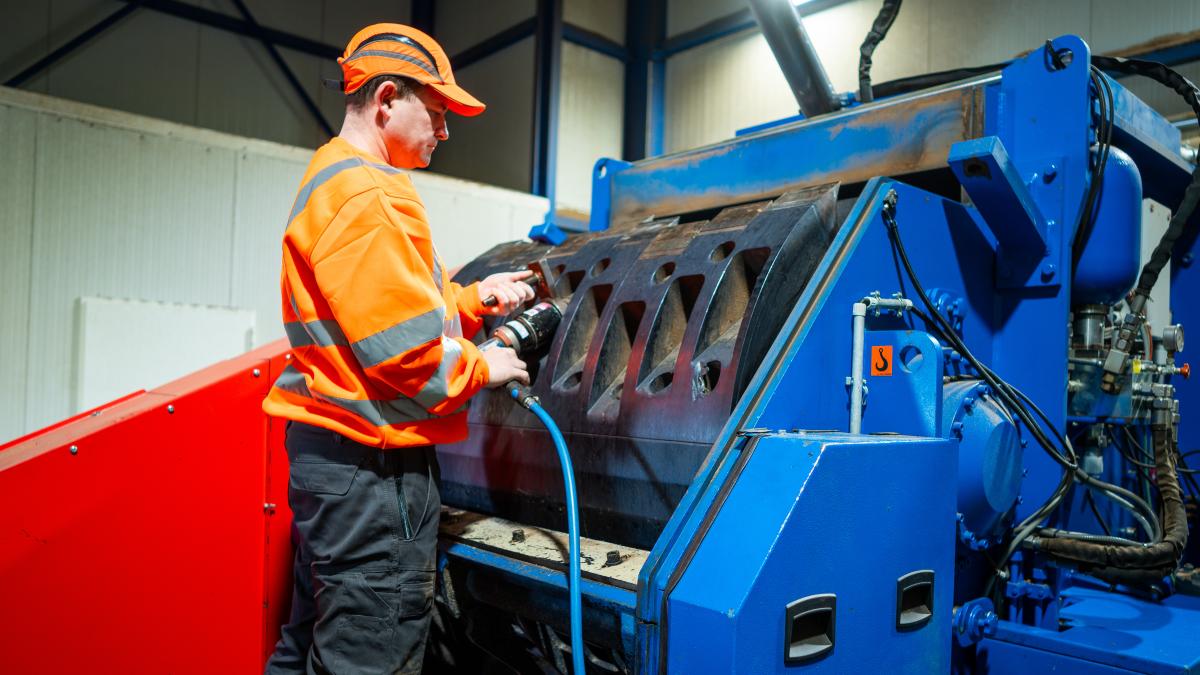
An optimal maintenance plan is an essential part of new machine design. The aim is to make repeated operations such as knife replacement faster and easier.