“Every door we make is absolutely unique”, says Markus Löhr. The master carpenter’s family business in Höchstenbach in the Westerwald is now almost 160 years old and in its fifth generation. The company meanwhile employs 15 people, five of whom are master carpenters. “We manufacture customised solid wood doors. They can be modern if desired, but our focus is on historical doors,” he explains. His father still offered the classic range, including windows, stairs, front and interior doors. However, the competition from larger companies was strong. When Markus Löhr took over the business in 2004, he transformed the carpentry workshop into a door manufacturing facility – not only returning to “real” carpentry, but also finding a market niche in which he has been extremely successful for years. “Our annual turnover is around one million euros,” says Löhr. Customers come from all over Germany and neighbouring countries like Switzerland, Luxembourg, and France. The master carpenter even had a door delivered to Denmark recently.
Customized doors
In the workshop, Markus Löhr points to various doors, some of which are still being made, while others are ready for delivery. “Some customers send us their suggestions, others provide photos of their houses, and I’ll take some pictures myself on site – then we develop the appropriate designs based on our analyses of these pictures and on discussions with the customer,” says the master carpenter. It’s crucial that the result matches the building’s style and design perfectly – because it makes a big difference whether the building was constructed during the Art Nouveau period or the Wilhelminian era. Löhr also often has to reconstruct doors, a task for which he uses photos or old drawings. If necessary, these have to be coordinated with the heritage conservation authority. On request, his solutions comply with the current thermal insulation regulations, or his doors can be made burglar-proof or soundproof. “Our doors can meet specific climate classes and even the passive house standard if required”, explains the master carpenter. He is also very proud that he can offer yet another craft to customers, because his team includes a glazier who specialises in decorative and individually-designed leaded glass – and he also offers hand-carved decorations that are as unique as the customers’ wishes.
Sustainability is a top priority for Löhr, because historical building materials, such as old wood from old oak beams, are revitalised during the door manufacturing process. His craftsmen use these to create modern front door designs as well as historical replicas – and combine them with the latest security features. The first lorryload of historical timber drove into the yard around twelve years ago. Orders were a little slow at first; and he tried out a lot of ideas, but soon demand started to grow steadily. Today, a large part of the wood he stores and uses comes from old half-timbered and demolition buildings. However, even although the stock of timber is currently well filled, Löhr is always looking for new sources.
The efficient shredding of residual wood
In production, the beams are sawn into planks, planed and glued. Then the movable part of the door – the door leaf – and the fixed frame are constructed. This involves gluing the planks layer by layer, then milling in locks, strike plates, and hinges. Waste is inevitably generated during production: untreated residual wood, old wood, pieces of beams, wood offcuts and cuttings. “We use the waste material to fire our furnace system, which we recently modernised,” explains Löhr. This enables the company to heat its buildings efficiently. To reduce the wood to the required size, the facility relied on a Vecoplan shredder for almost exactly 30 years. With its headquarters just a few kilometres away in Bad Marienberg, Vecoplan develops systems that shred, convey, separate and store wood, biomass, plastics, paper and household and commercial waste. “Vecoplan was a customer of ours for many years, we knew them well,” says Löhr. “So it was only natural to buy a machine from them.”
The old shredder from the small VAZ series ran reliably for years without any significant issues. A local locksmith could handle small repairs when needed, the carpentry workshop did the oil changes themselves, while Vecoplan supplied new counter knives and concave cutter. Apart from the various maintenance intervals, the owner is delighted that no maintenance has ever been necessary in the 30 years. However, even the most robust system shows signs of ageing at some point in its working life. The control cabinet recently broke down, and the electrician highly recommended buying a new machine.
Suitable for any input
Florian Greb, Area Sales Manager at Vecoplan, provides support for the Löhr door manufacturing company: “We advise our customers, plan the technology, and find the right solution together,” he says. “Of course, our tasks also include complete project management, assembly, commissioning and a comprehensive service programme.” Vecoplan offers the VHZ 800 specifically for carpentry and joinery businesses. This durable and robust shredding solution was specifically developed by the machine manufacturer for the needs of the wood processing industry and small businesses. The single-shaft shredder is an economical solution for customers, enabling them to feed various input materials and different quantities directly and undosed into the shredding process. Thanks to its VHZ-ESC drive (E=Electronic, S=Slip, C=Control), the machine operates energy-efficiently and cost-effectively compared to conventional drive systems. “We conducted trial shredding in our in-house technology centre,” says Florian Greb. Markus Löhr was present and provided his typical material for the machine in advance – and he was immediately impressed – “That machine went through the historical wood as if it were butter.”
The new VHZ 800 stands in the yard. A forklift driver feeds the machine’s feed hopper with input material which can be up to 200 x 100 x 500 millimetres in size. With a throughput of 100 kilogrammes per hour, the new machine processes the wood to a particle size of less than 20 millimetres. The system is in use for about two hours a day and two days a week. Master carpenter Löhr is convinced: “If the new machine works as reliably over the next 30 years as our first shredder, we’ve made the right decision.”
Doors built to last for generations
“Original historical front doors were originally made of wood. When restored, they’re still splendid ornamental objects that give the property entrance a face,” says Löhr. “However, aspects like energy efficiency and security no longer meet today’s standards.” The massive and multi-layer glued solid wood front doors made by the master carpenter can be passed down to the next generations, like their historical counterparts. “They are secure, impervious to all kinds of weather and incomparably valuable and beautiful,” he says.
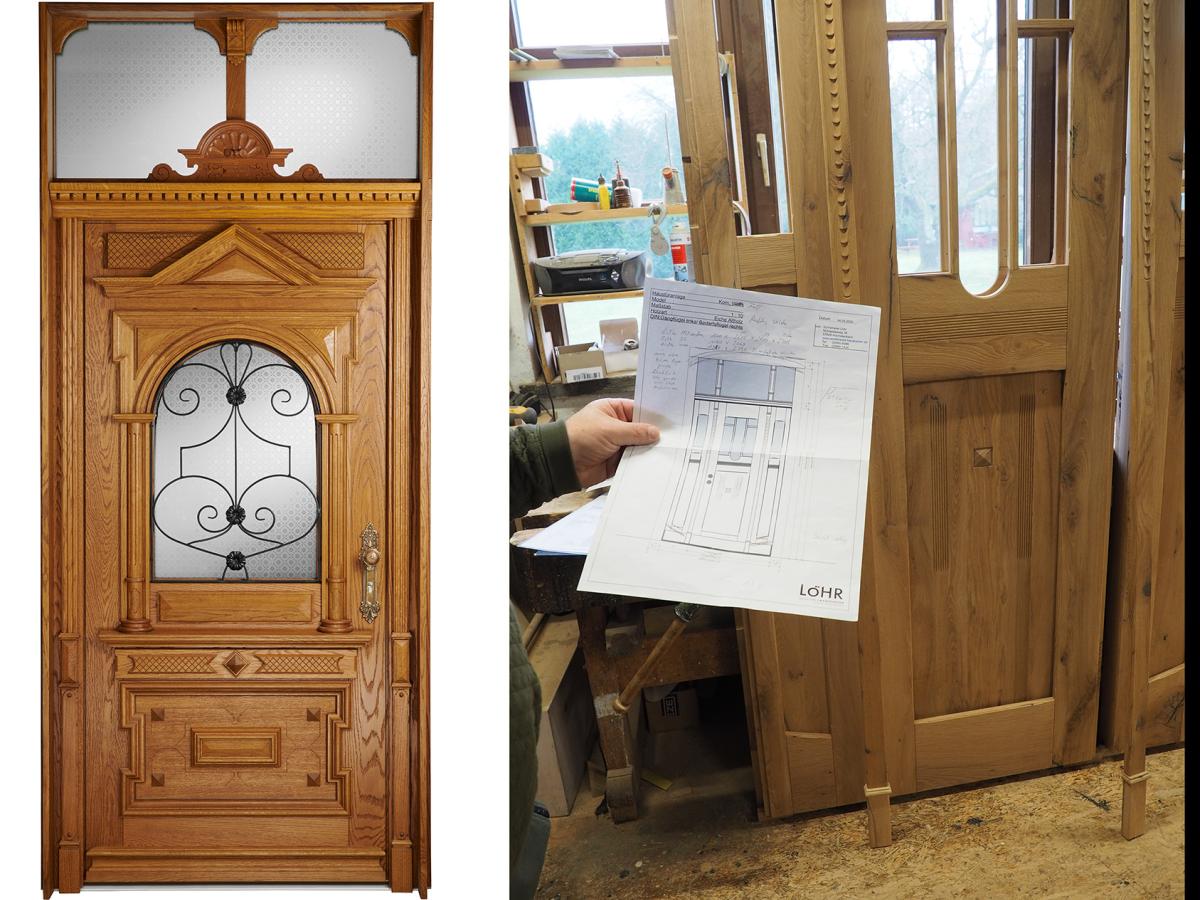
Every door is unique – Löhr carpenters manufacture customised, solid wooden doors from historical wood. It’s crucial that the doors are stylistically accurate and match the building – or better yet, the era – perfectly.
A look into the company’s production, where pure carpentry craftsmanship is key.
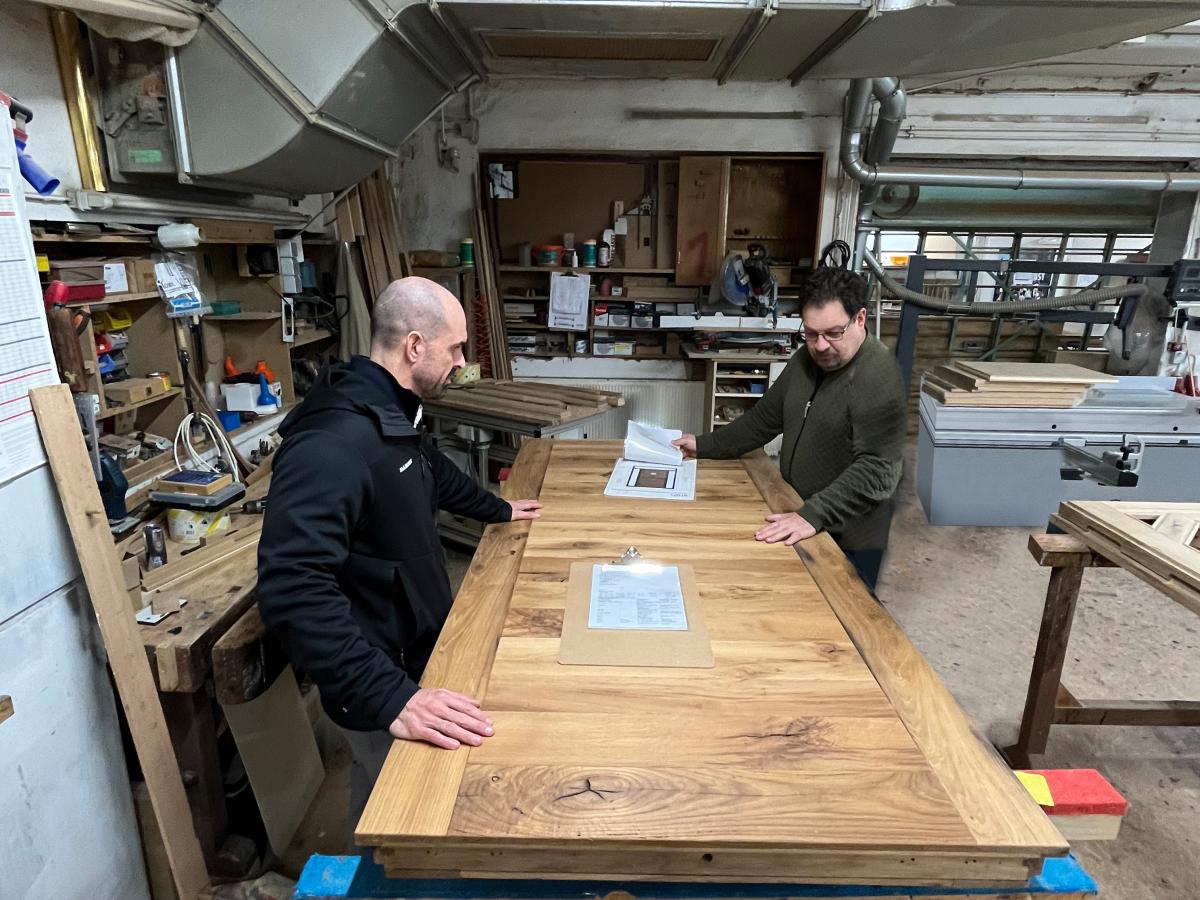
Master carpenter Markus Löhr (right) and Vecoplan’s Florian Greb: “We find the right solution together.”
Oak is the main material that’s used.
Untreated residual wood and old wood generated during production is fed into the furnace and used for heating.
To shred the wood to the required particle size, Vecoplan provided a durable and robust shredding solution with the VHZ 800. Forklifts can load residual wood into the feed hopper.