"We deliberately focus on niche markets and are the leaders in our field," explains Matthias Henning. He is the managing director of General Industries Deutschland GmbH, or GID for short. The company has existed for almost 30 years. "My father founded it and was already passionate about recycling at a time when recycling wasn’t really an issue," he says. Matthias Henning joined the company just under ten years ago. His father had set up the company on a very broad basis, but his son focused on a novel approach: "I knew we could only hold our own against the big companies if we operated in niches – like a boutique that offers nicer and fancier clothes for special occasions than a department store chain, but which naturally cost a little more." GID comes to the fore when standard solutions are no longer sufficient for users.
The recycling plant in Eschwege and the production plant and logistics centre at the company’s headquarters in Kassel employ around 50 GID staff. In Eschwege, the company transforms lightweight plastics made from expanded polypropylene (EPP), polyethene (EPE) and polystyrene (EPS) into high-quality secondary raw materials. These originate as packaging waste from imported goods (disposable packaging) and as end-of-life packaging (reusable packaging), mainly from the automotive sector. In 2023, GID invested more than €2.5 million in recycling technology in Eschwege and further expanded the site with a new plastics processing and recycling plant that can produce an additional 11,000 tons of plastic regranulate per year over and above the existing capacity of 7,000.
An efficient shredding technology
The material must be shredded before being fed to both extruder lines. "Our existing shredder was only just under three years old, but it was permanently reaching its limits as demands increased," Henning reports. Challenging waste such as coarse nets, ropes and foil sheets proved difficult and even impossible for it to process, since the various materials repeatedly wrapped themselves around the rotor. GID was thus limited as far as shredding certain materials goes. “That didn’t fit in with our concept at all, since we ultimately want to offer ideal solutions for special challenges,” says the managing director. Added to this was the fact that without a frequency converter, the machine was permanently running at full load, increasing power consumption massively. This was a major disadvantage, because the company pays meticulous attention to energy consumption at every process step, from the delivery of the material to the finished recyclate. Energy now accounts for almost half of the total costs at the Eschwege site.
Those responsible in the company looked at various shredders – and at the end of the selection process, there were two suppliers to choose from, one of which was Vecoplan AG. The specialist company, headquartered in Bad Marienberg in the Westerwald region of Germany, develops plants that shred, convey, separate, and store wood, biomass, plastics, paper and household & commercial waste. "We advise our customers, plan the technology and find specific solutions together," explains area sales manager Philipp Güth, who is responsible for GID customer support. Vecoplan forms teams of application engineers and sales staff to this end. Güth: "Our tasks naturally include holistic project management as well as installation, commissioning and comprehensive services."
Flexible and extremely energy efficient
The first contact was made at IFAT 2022 in Munich. At the Vecoplan trade show stand, Matthias Henning explained his requirements for an energy-efficient, reliable and, above all, flexible shredding technology to Philipp Güth. “We supplied a VIZ 1700 shredder with a throughput capacity of about 2,000 kg per hour and a VIZ 1300 with just under 1,200 kg per hour for the two extruder lines,” says Güth.
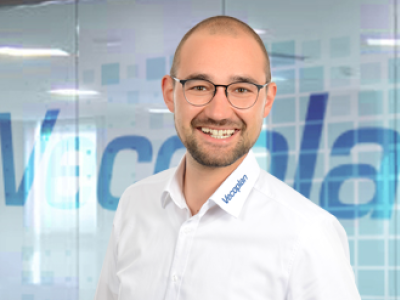
Our Vecoplan Infinity shredders have a high level of availability, their low operating costs and maximum throughput impress users and
they can process a wide range of different plastics.
During development, the focus was on flexible cutting geometry. Vecoplan can adapt the system’s performance to input and output requirements through individual rotor and blade configurations and the choice of the relevant screen. The performance can be precisely matched to the interface. “We were convinced by the HiTorc drive with its high startup power and torque,” reports GID Managing Director Henning. The direct drive is 10-15% more efficient, thanks to the elimination of mechanical drive elements such as belt and gear drives, flywheels and clutches. Energy savings of up to 40 per cent are possible compared to other electromechanical drives – and for hydraulic drives, this figure can be as high as 60 per cent.
This not only significantly reduces electricity costs, but also CO2 emissions – a powerful argument for GID. The company commissions an external institute to determine the total CO2 emissions of the value chain. These emissions are generated during the transport of materials, for example, during extrusion, and of course during shredding. Henning: “This is why we also compared the reference values of the machines offered to us by the manufacturers in advance. Vecoplan convinced us with its energy-efficient drive concept. That was another important decision criterion.”
CO2-neutral from the outset
GID has set up an intelligent collection system for packaging waste made of EPP/EPE, which is both voluminous and very light. To recycle the packaging as efficiently as possible and also reduce CO2 emissions, the company has established collection points throughout Europe where the packaging waste is first compacted. As a result of this process, one truck can carry the amount of material that would normally fill 22 vehicles.
In Eschwege, forklifts feed the palletised and sorted waste directly into the shredders. The VIZ 1700 processes baled packaging residues, production waste and purgings. These bales have maximum dimensions of up to 1,200 x 800 x 500 millimetres.
Stretch films, ropes and coarse nets are also processed. The smaller VIZ 1300 shreds waste up to a maximum of 1,200 x 400 x 400 millimetres in Eschwege. The input material, consisting of various plastics, is hardened and contamination-free. Vecoplan also supplied flat belt conveyors with a small intermediate buffer that transport the shredded material to the extruders. Neodymium magnetic head drums separate metallic impurities that are already magnetised. “We were able to permanently set parameters like ram behaviour and speed without having to change them during operation,” explains Philipp Güth. In some cases, the systems run at a speed of only 25 per cent; the previous shredder ran permanently at 100.
Risk of accidents averted
Another important aspect for Matthias Henning is also the safety of the machines. “With our previous shredder, accidents kept happening during maintenance,” he reports. “The main reason for this was that we had to turn the rotor manually when we were changing the cutting tips.”
Thanks to the HiTorc drive, the VIZ can move the rotor at low speed to the appropriate maintenance position. There is a special mode for setting the cutting gap perfectly and safely outside of the machine. All the maintenance work can also be carried out ergonomically thanks to the hydraulically operated, swing-open bottom flap. The concept of bolted tool holder plates with variable cutting tip sizes also means that rotor changes are no longer required.
Sophisticated digitalisation concept
The two shredders are equipped with the Vecoplan Smart Center (VSC), and the intuitive VSC.control operating panel is integrated into this powerful digitalisation concept. The panel serves as a communication medium for modern control and a direct link to Vecoplan. The machine is networked with the help of the VSC.connect. The VSC.connect also provides online access to additional services such as key performance indicators, remote service and a media database.
“We can use it on our iPads to examine the condition of the shredders and intervene on ourselves if necessary,” says Henning. “That's especially important on weekends when neither I nor the plant manager are present.” Key performance indicators include not only throughput per unit time, but also power consumption. This provides information about how efficiently the material is being processed. With this option, GID can present the actual costs to its customers even more transparently – and the temperature from the output can be continuously measured with the VSC.
A rotor which is too hot can cause some plastics to melt and this in turn causes the components to stick together. In the past, this very often led to unplanned shutdowns during continuous operation. The GID managing director is delighted: “Thanks to the Vecoplan Material Cooling (VMK) system, we can now control the temperature continuously and cool it down only when the process requires it.” The plant manager can also remotely connect to the machines at any time. A camera gives him a view of all the sensitive areas. This minimises downtimes.
The right partner at your side
GID has reduced its energy costs and increased productivity with Vecoplan’s efficient shredding technology – and the company can now process a much broader range of materials. “This makes us even more interesting for our niche because we have the right answer for every material,” emphasises Henning. However, service also plays a very important role for him. “We’re a small company. What if we need support fast? Can we only reach a call centre or do we get an expert on the line right away? With Vecoplan, we know we’ll be talking to an expert.”
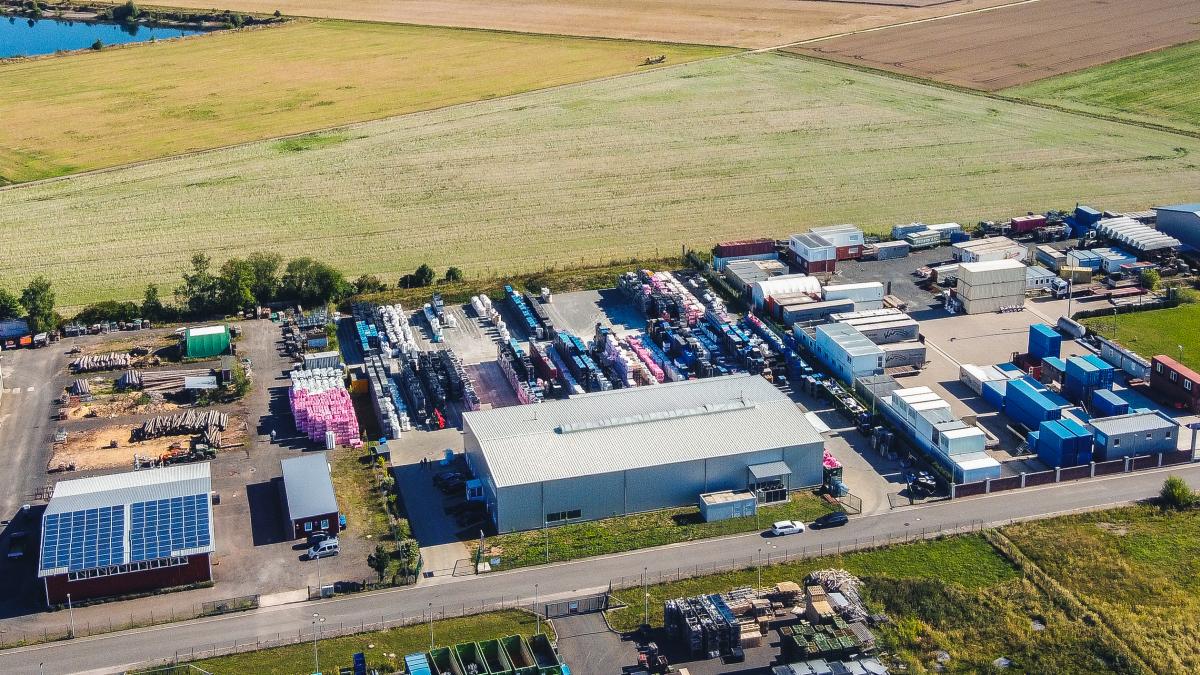
General Industries Germany transforms challenging post-consumer waste of foamed plastics into high-quality secondary raw materials at its Eschwege site.
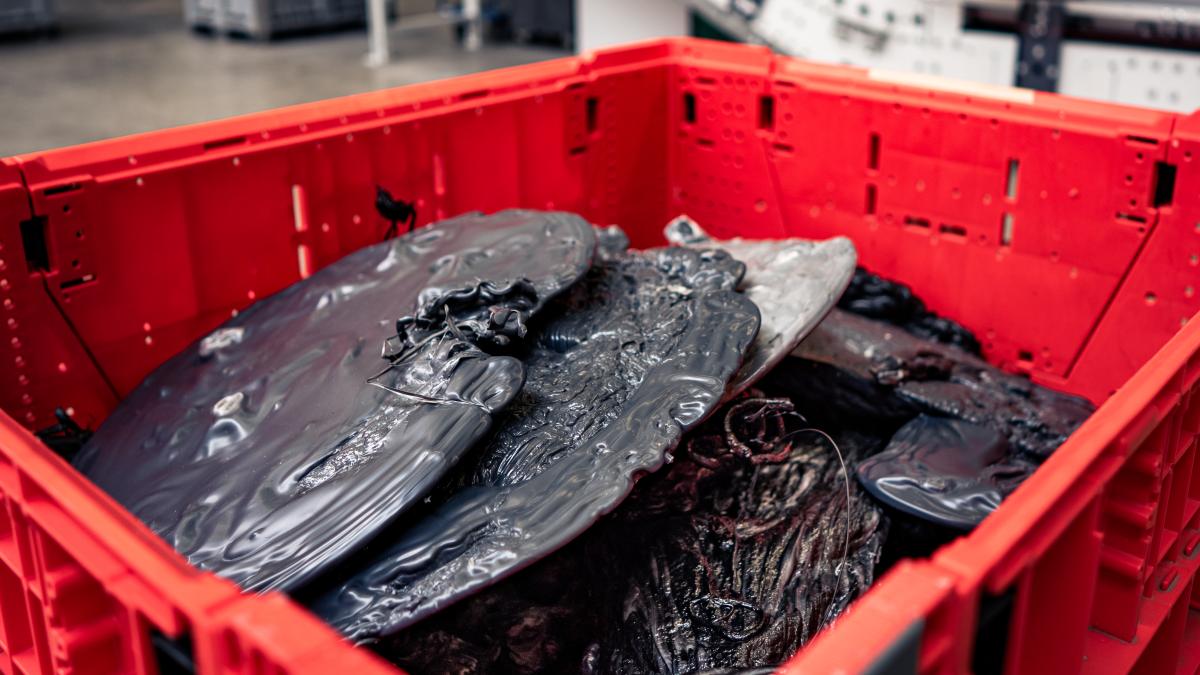
The input material includes purgings (post-industrial waste) …
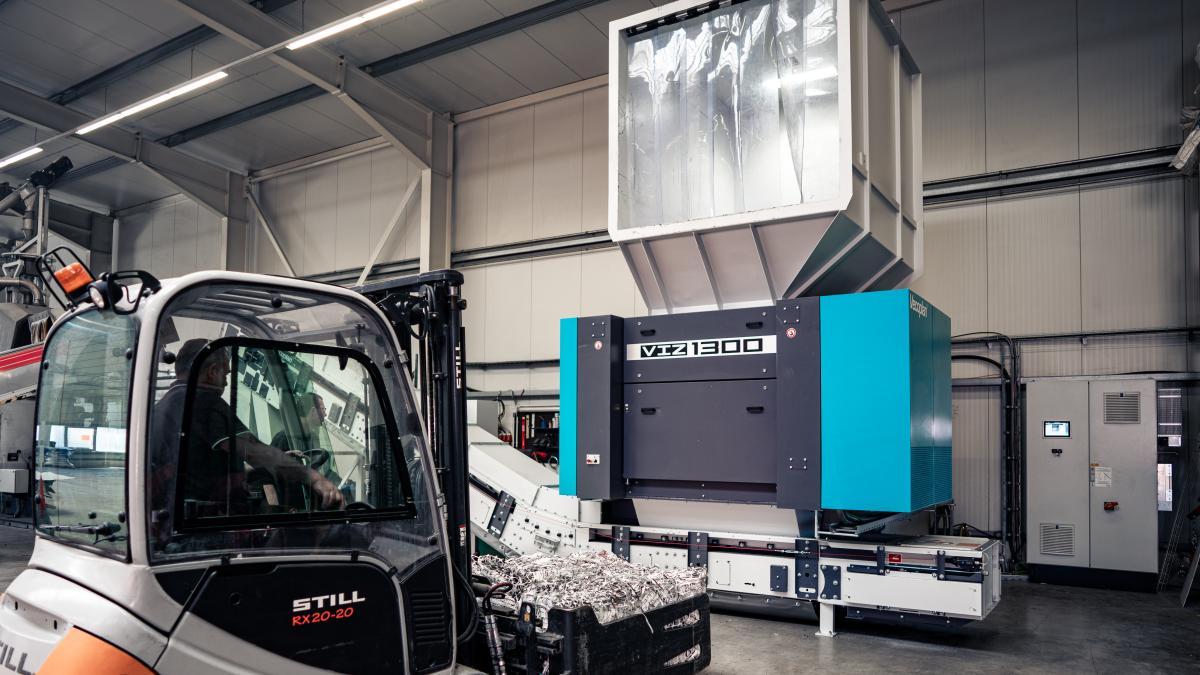
… as well as stamping grid residues (post-industrial waste) pressed into bales.
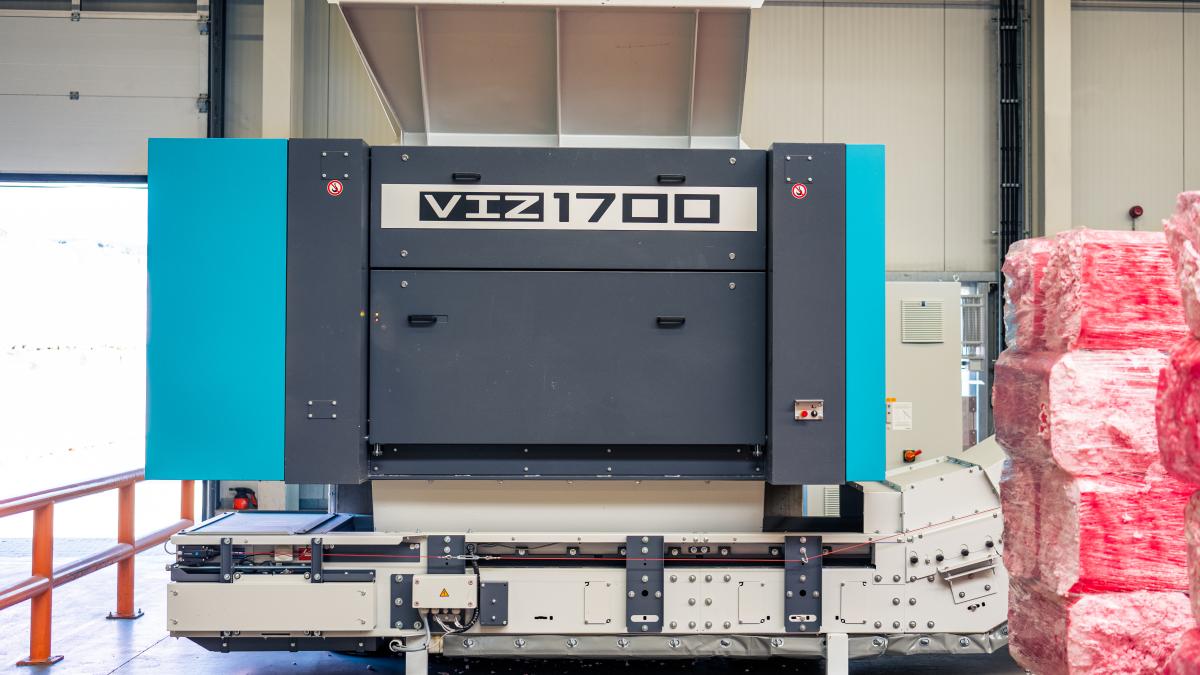
The VIZ 1700 has a throughput capacity of around 2,000 kg per hour. The shredder has a high level of availability and impresses users with its low operating costs.
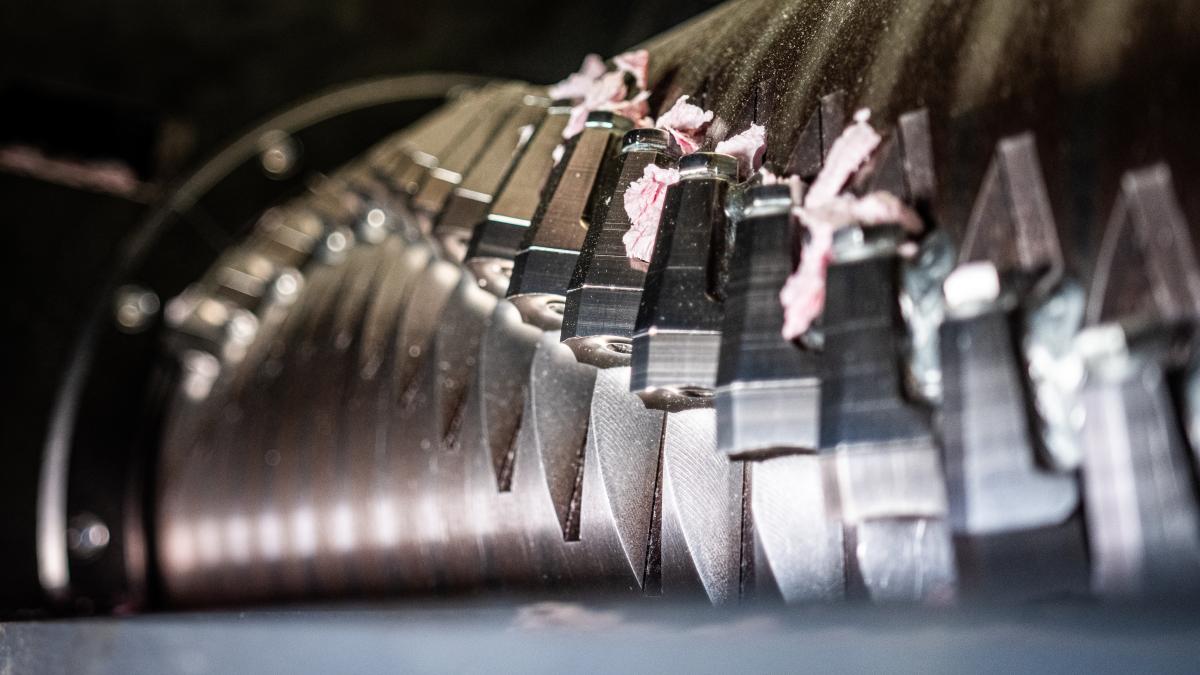
The cutting geometry is exceptionally flexible. Vecoplan can adapt the system’s performance to input and output requirements through individual rotor and blade configurations and the choice of the relevant screen.
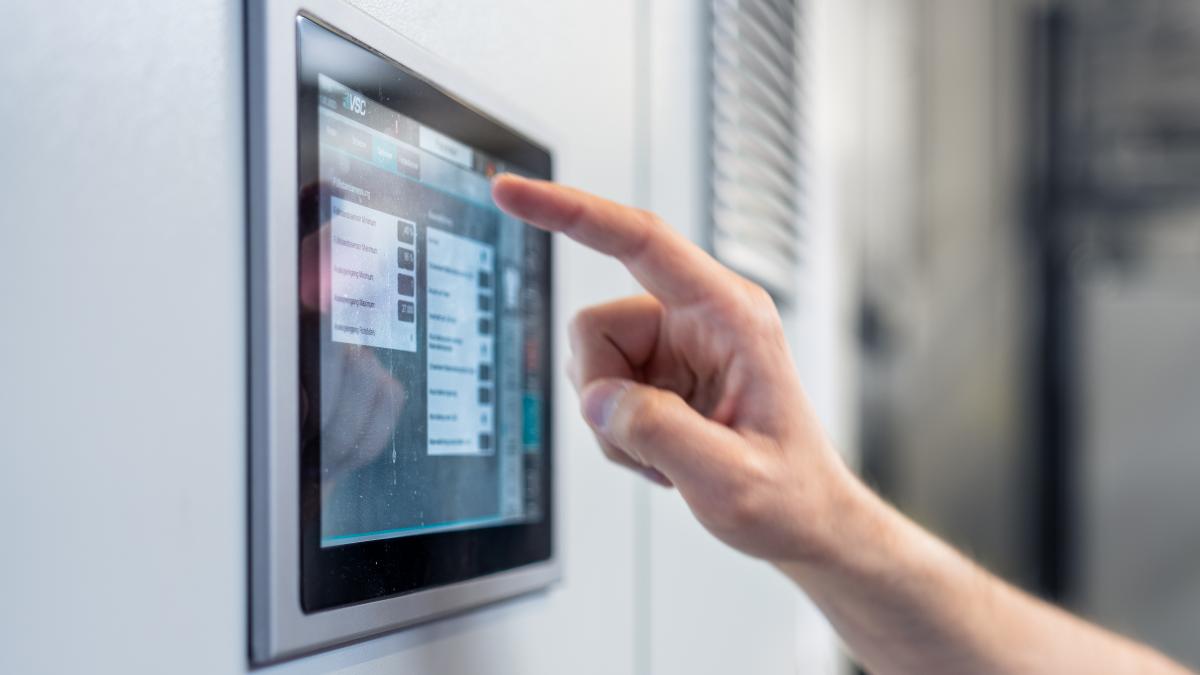
The two shredders are equipped with the Vecoplan Smart Center (VSC), a powerful digitalisation concept.
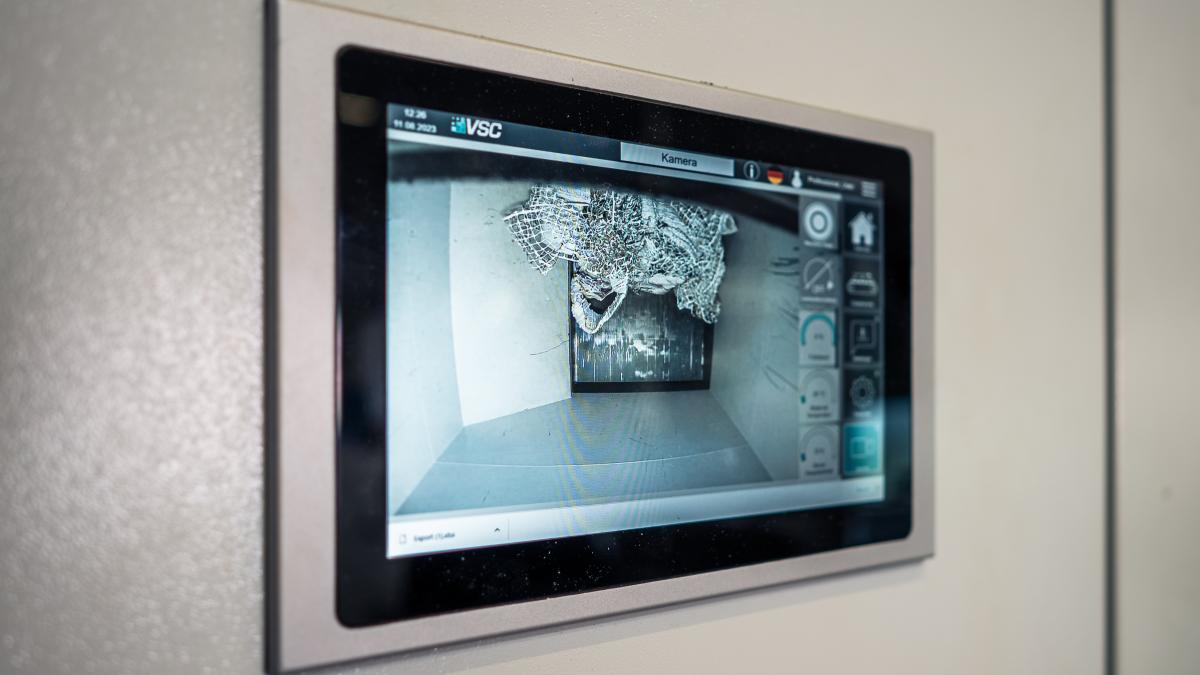
A camera gives the plant manager a view of all the sensitive areas.
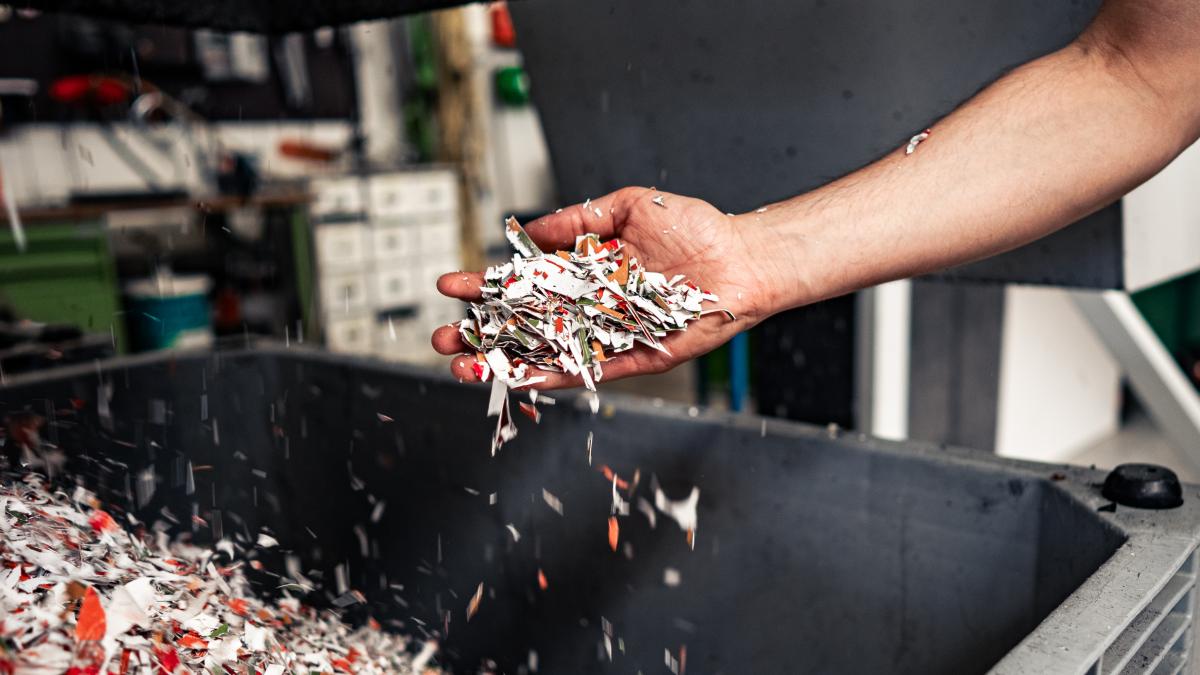
The shredded material is ready for the extruders.
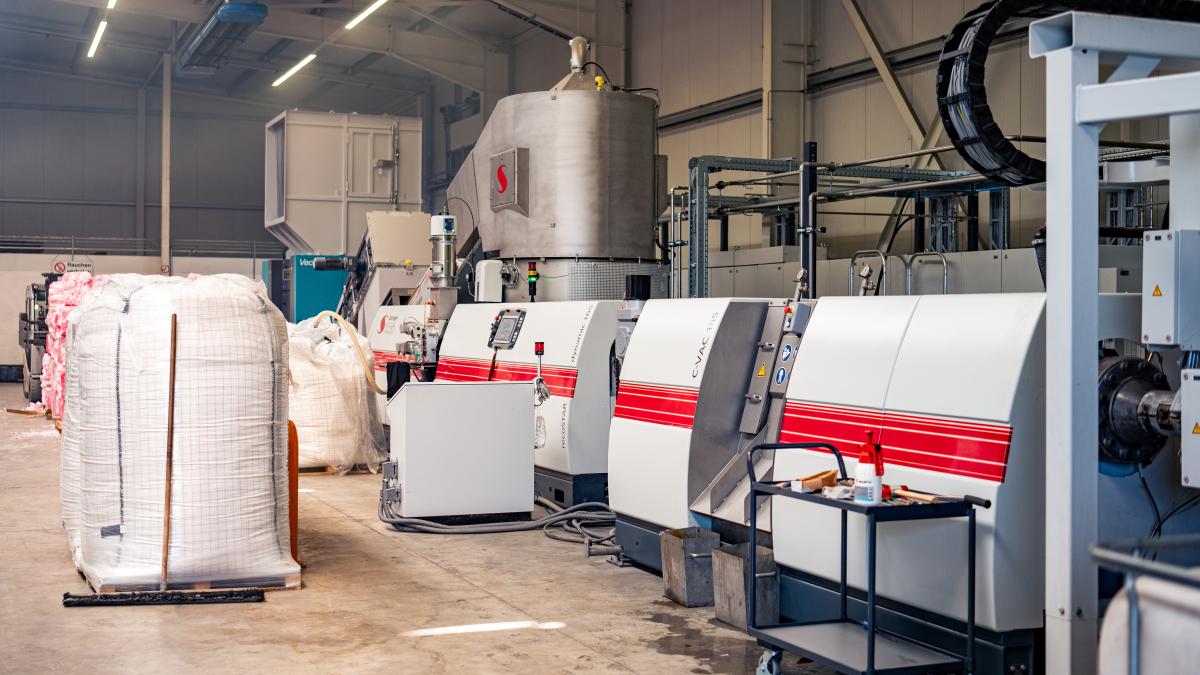
During the downstream processes, metallic impurities are removed from the shredded material, which is then fed to the extruder.
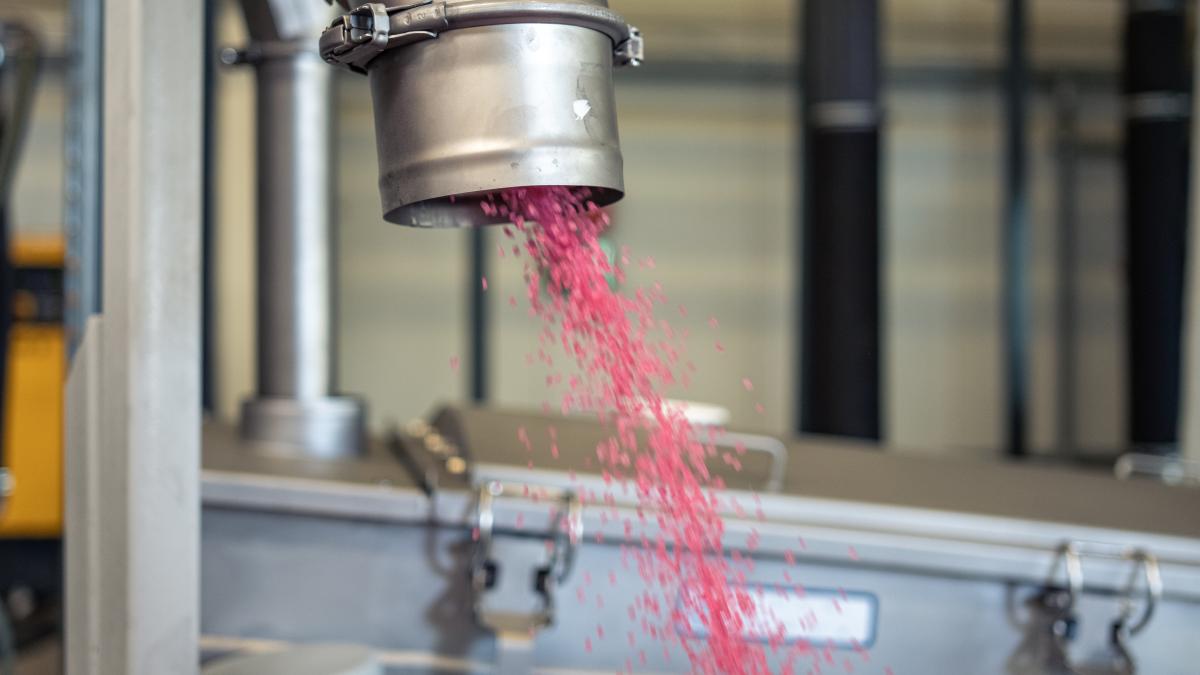
The result? High-quality secondary raw materials.