“We obtain our wood exclusively from Switzerland within a radius of about 100 kilometres, and we only supply the Swiss market with our products,” says Roland Birrer. Tschopp Holzindustrie, based in Buttisholz in the canton of Lucerne, is the only manufacturer in the country that produces shuttering panels for the construction industry. “Our existing sawmill has been in operation since 1999. It’s designed to process 30,000 cubic metres of wood per year – but we’re currently processing up to 115,000 cubic metres,” Birrer adds. Tschopp has worked three shifts for about ten years to cope with this volume. The capacity limit has long been reached. Room for new ideas, for new products? Not a chance. If Tschopp was to expand its capacity, the logical solution was a new sawmill – and in 2018, the company’s decision-makers decided to invest in one. Roland Birrer is the manager of the new sawmill.
Capacity limit significantly expanded
The plant will go into operation in May 2023. Technicians from suppliers and partner companies spent weeks commissioning the installed equipment in the 123-metre-long and 20-metre-high new building. The smell of freshly sawn wood wafts over from the existing plant, which is only a few hundred metres away. “Our new sawmill is designed to process 350,000 cubic metres of wood per year. That’s also enough space to produce new wood-based materials,” says Birrer with satisfaction. Previously, this had not been possible due to the lack of capacity and technology. According to the plan, when the new sawmill is up and running, the old one will gradually be shut down.
Tschopp Holzindustrie was founded as a two-man business in 1920. Today, 125 employees work at all locations. Ronald and Daniel Tschopp are the owners and lead the company in the third generation The company manufactures all the facets of the shuttering panels. A special feature on the longitudinal and end edges of the panels are the seals, which prevent concrete residue from adhering and facilitate cleaning. The seals also lengthen the panels’ service lives. “With these panels, we offer not only quality, but also a high level of technical sophistication. Added to this is our staff’s in-depth expertise in our products,” says Birrer, listing the success factors.
Nothing is unused
The production of shuttering panels generates a lot of wood residues such as chips, sawdust, offcuts and bark – and to ensure that nothing is wasted, 2005 saw Tschopp build its own pellet production facility, which the company has continuously expanded. Today, Tschopp produces up to 120,000 metric tons of pellets every year. The site has also had its own wood-fired power plant since 2014. “The plant provides the entire heat for drying the sawn timber and the pellets,” says the sawmill manager. “We use the residual heat to produce environmentally friendly electricity.” The facility generates around 9.4 million kilowatts per year. Tschopp Holzindustrie thus utilises one hundred percent of the raw material at the site. Since more wood will be processed in the new sawmill, more energy will also be needed for drying it, but there is enough space on the property for another power plant.
The ideal chip thanks to the right technique
Tschopp relies on Vecoplan to process the waste wood for pellet production and green electricity. The specialist company, headquartered in Bad Marienberg in the Westerwald region of Germany, develops plants that shred, convey, separate, and store wood, biomass, plastics, paper and household & commercial waste. “We advise our customers, plan the technology and find the right solution together,” explains Michael Müller, project manager for the Swiss timber company. “Our tasks naturally include holistic project management as well as installation, commissioning and comprehensive services.”
Tschopp Holzindustrie has been working with equipment from the Westerwald company for more than 30 years. Birrer: “Vecoplan has a good name in the market, and the service is always perfect, so it was clear to us that we’d continue the good cooperation.” The machine builder was involved in the project from the outset. Michael Müller and his team assisted the Swiss company with the planning and were able to construct the new facility on its greenfield site.
The Vecoplan expert points upwards. “The sawing lines are on the floor above us here. The waste wood falls through the floor onto the conveyor belts.” In this way, the sawdust is combined on several conveyors. A star screen separates excess lengths. Wood sections (or head discs) also fall onto a conveyor belt and are fed into a VHZ 1600 series shredder, a robust single-shaft shredder with a modular design, which makes it extremely versatile. Vecoplan has various possibilities to configure the perfect machine for the customer. The responsible application engineering department can adapt components such as rotors, cutting crowns, counter knives, screens and drives to match each customer task. The pieces pre-shredded in this way are fed horizontally to the VTH 650 series drum chipper via a vibratory conveyor. “This system achieves enormous throughput rates,” says Müller. Thanks to the shredding method, the waste wood pieces are hacked to a chipping length of about 15 millimetres. The material then passes through another star screen, which separates excess lengths. It can now be fed directly to the drying process in the pellet mill.
Safe and quiet transport
The material prepared in this way is placed on a steep conveyor, which transports it to a pipe belt conveyor of the VRF series. With a length of 140 metres, the pipe belt conveyor transports the bulk material to the raw material halls of the pellet plant, which are only a few metres away. The tubular and all-around closed design of this Vecobelt completely encloses the bulk material, protecting it from the effects of wind. The conveyor belt in this series does not run on rollers like conventional conveyors. Instead, the belt is supported by an air cushion, which minimises friction loss during operation. It also runs quietly, which makes for a more pleasant working atmosphere on the premises. The system conveys the material at a maximum of 2.5 metres per second.
“Thanks to the pipe belt conveyor, Tschopp doesn’t need wheel loaders or trucks to load the processed material, nor is intermediate transport necessary,” says Michael Müller. “This saves time, space and energy.” Tschopp also takes back its customers’ old shuttering panels, which are shredded and fed into the wood-fired power plant.
Mastering the challenges
“The coronavirus crisis naturally presented us with repeated challenges during the construction phase,” says the Tschopp sawmill manager, “because the pandemic really messed up the supply chains.” Roland Birrer had to stay in close contact with the construction and partner companies to ensure that everything ran smoothly during the pandemic. “We strongly encouraged them to order the materials and the components they needed early – and the effort paid off because we never had to wait long for anything.” The supply chains remained stable over the entire duration of the project – although a show of strength was necessary now and then. Added to this were market changes such as rising steel prices, which regularly triggered discussions –
And that’s precisely why the sawmill manager enjoyed working with Vecoplan. Roland Birrer: “On the one hand, Vecoplan provided us with proven technology that delivers what it promises, and on the other, the processing was constructive throughout. Michael Müller and his team contributed ideas and suggestions, and even when we were almost finished with the planning, they were always ready for talks to discuss a solution, even a second, third and fourth time. So in the end, we had our perfect preparation.”
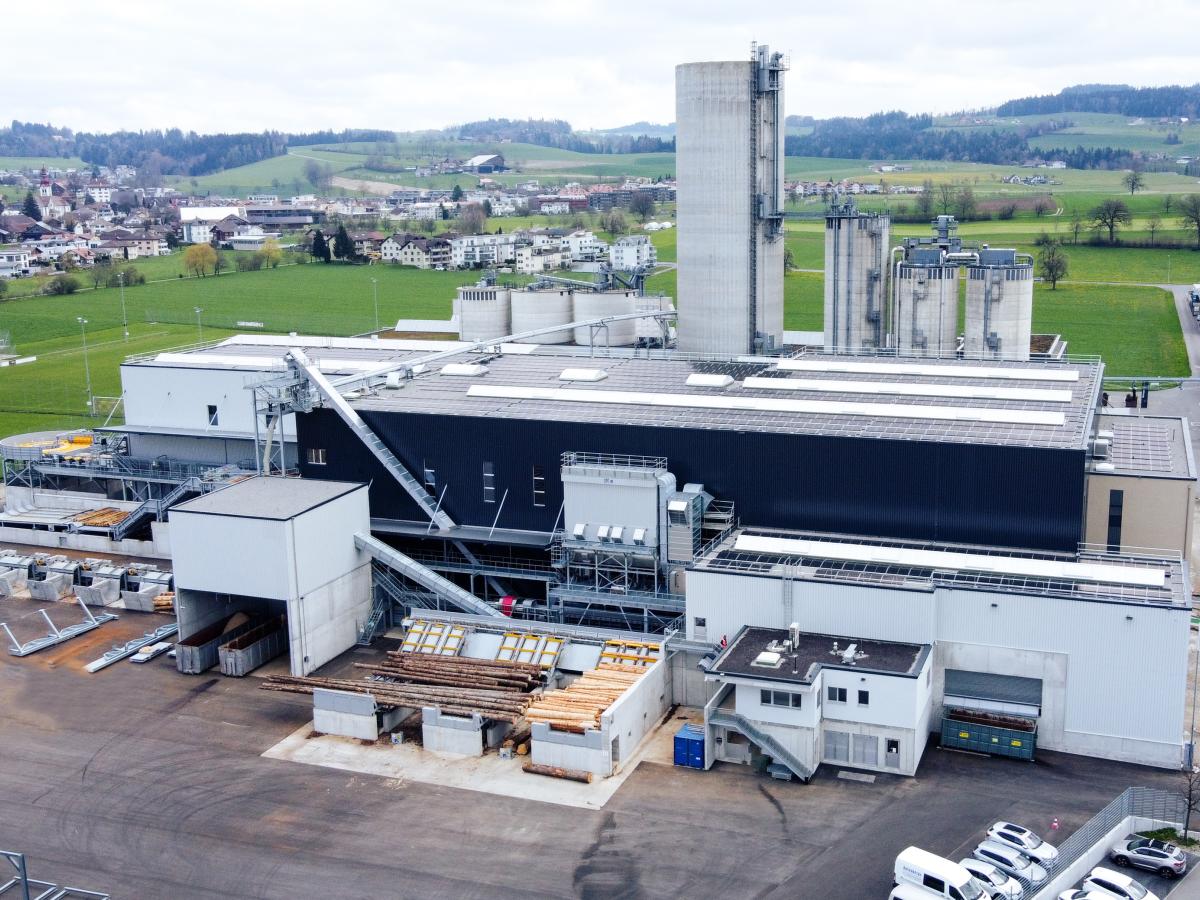
The new building of Tschopp AG: Vecoplan supplied the equipment for the disposal and processing of the waste wood from the sawmill line.
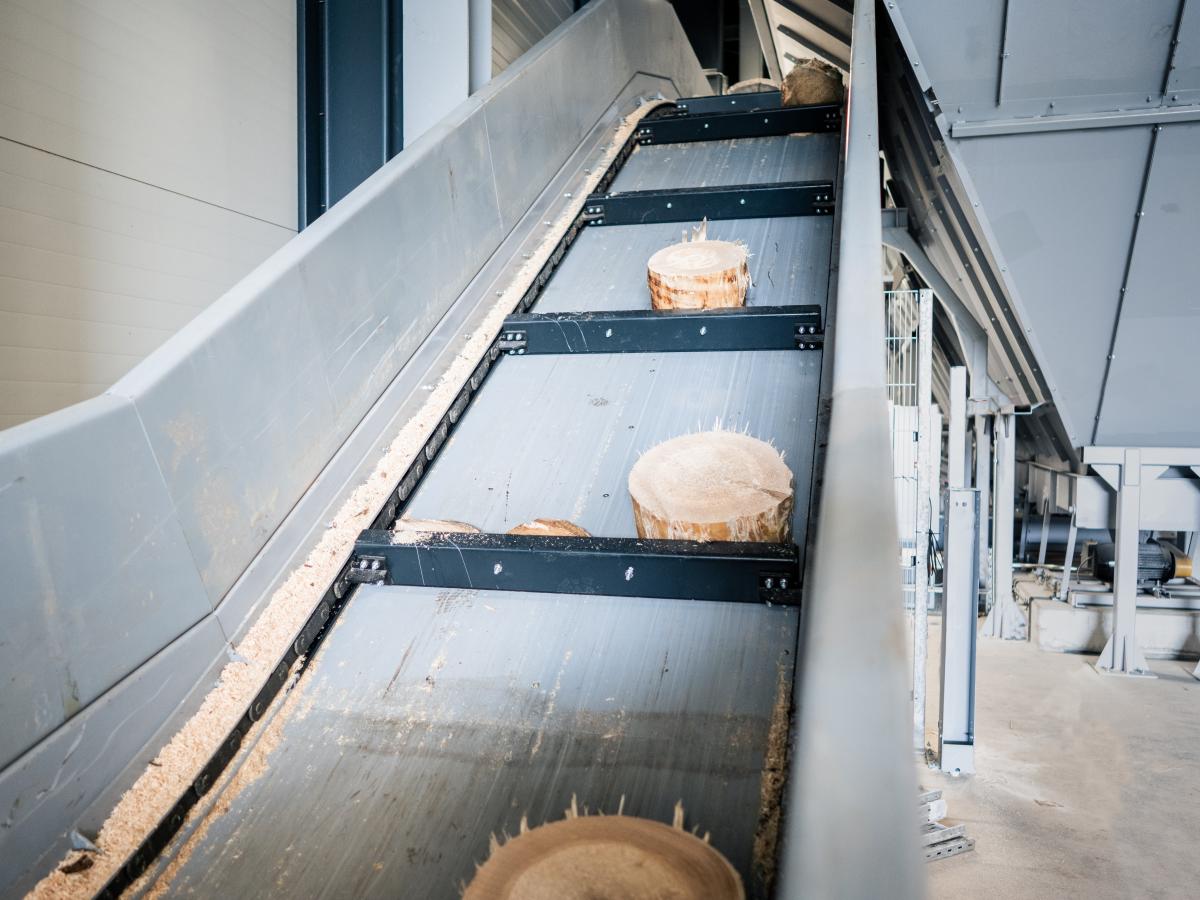
The conveyor system transports the pile caps to the VHZ 1600 for pre-shredding.
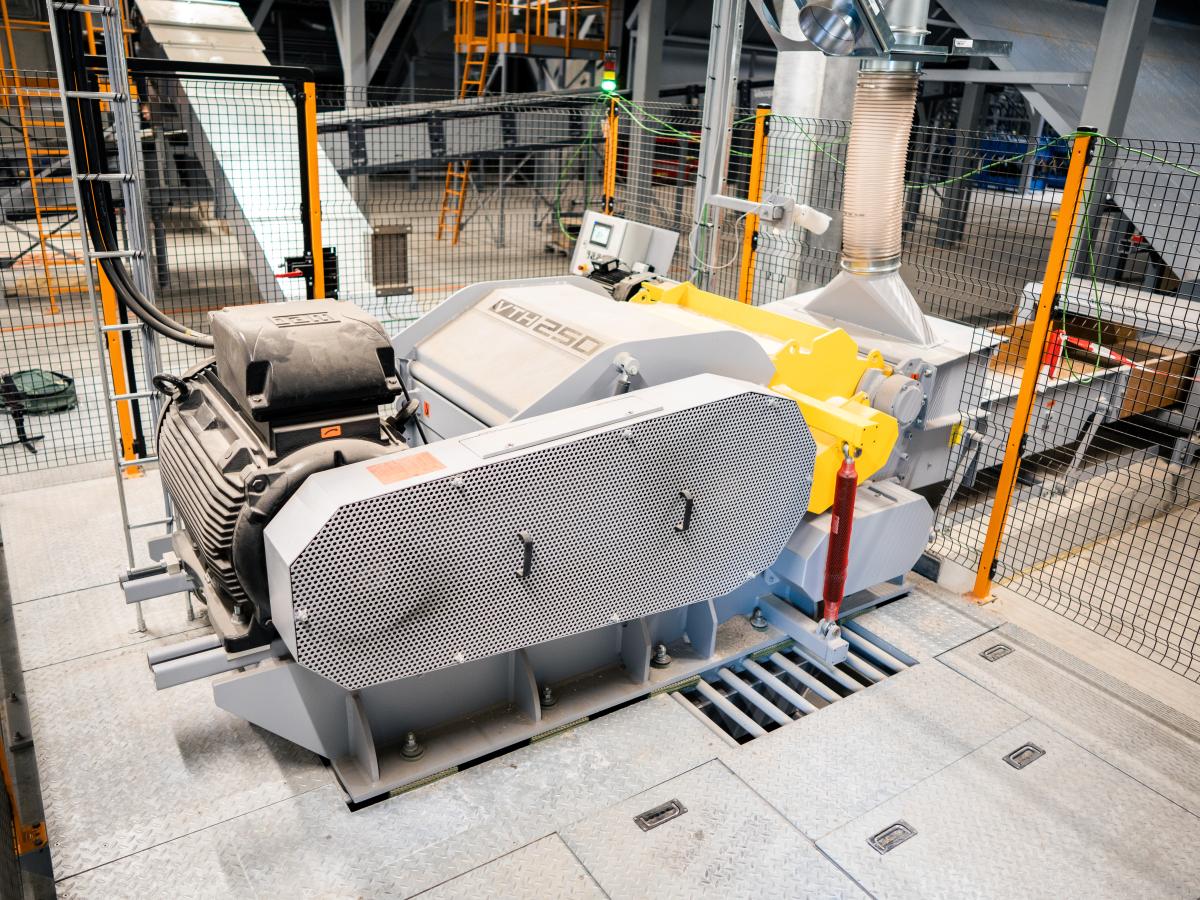
The drum chipper reduces the waste wood to a maximum chip length of 15 millimetres.
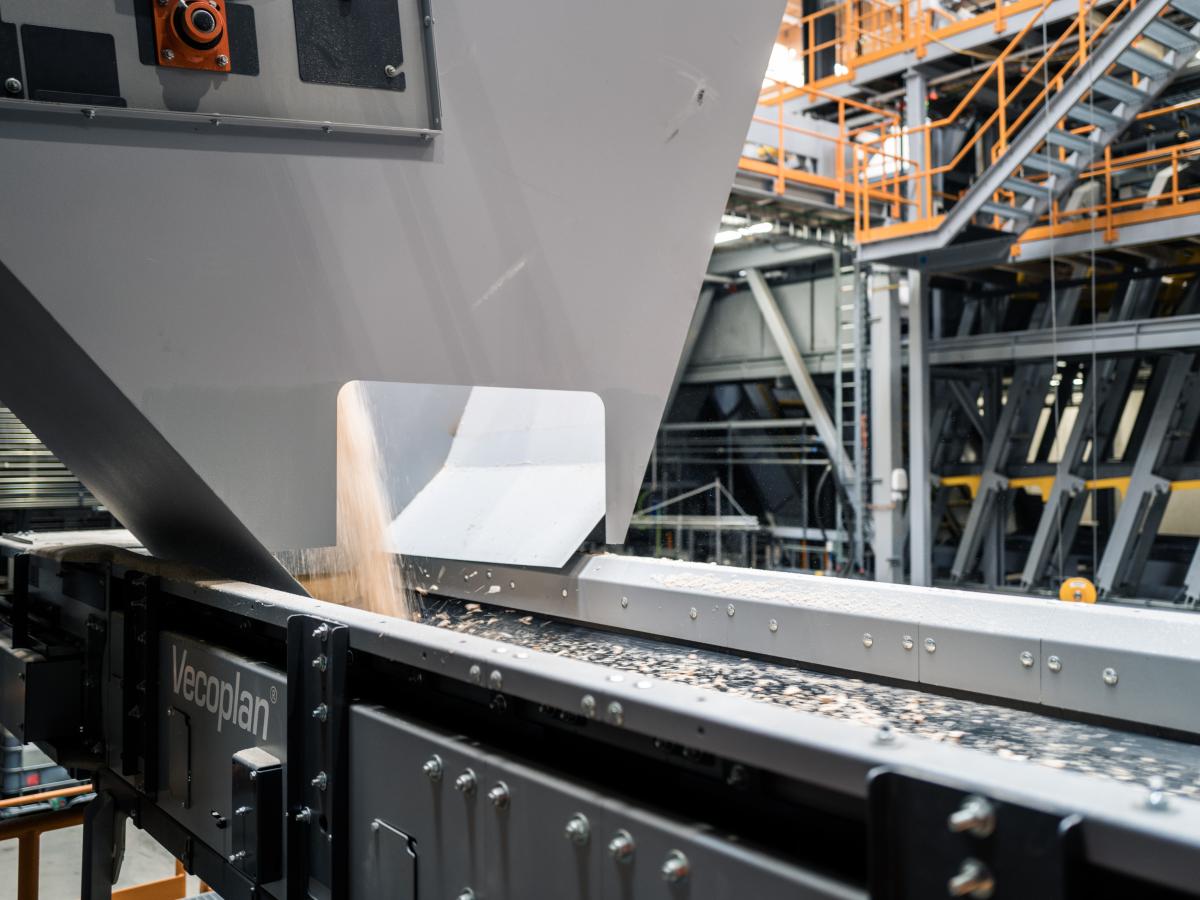
The conveying technology installed by Vecoplan transports the material within the disposal line, continuously and safely.
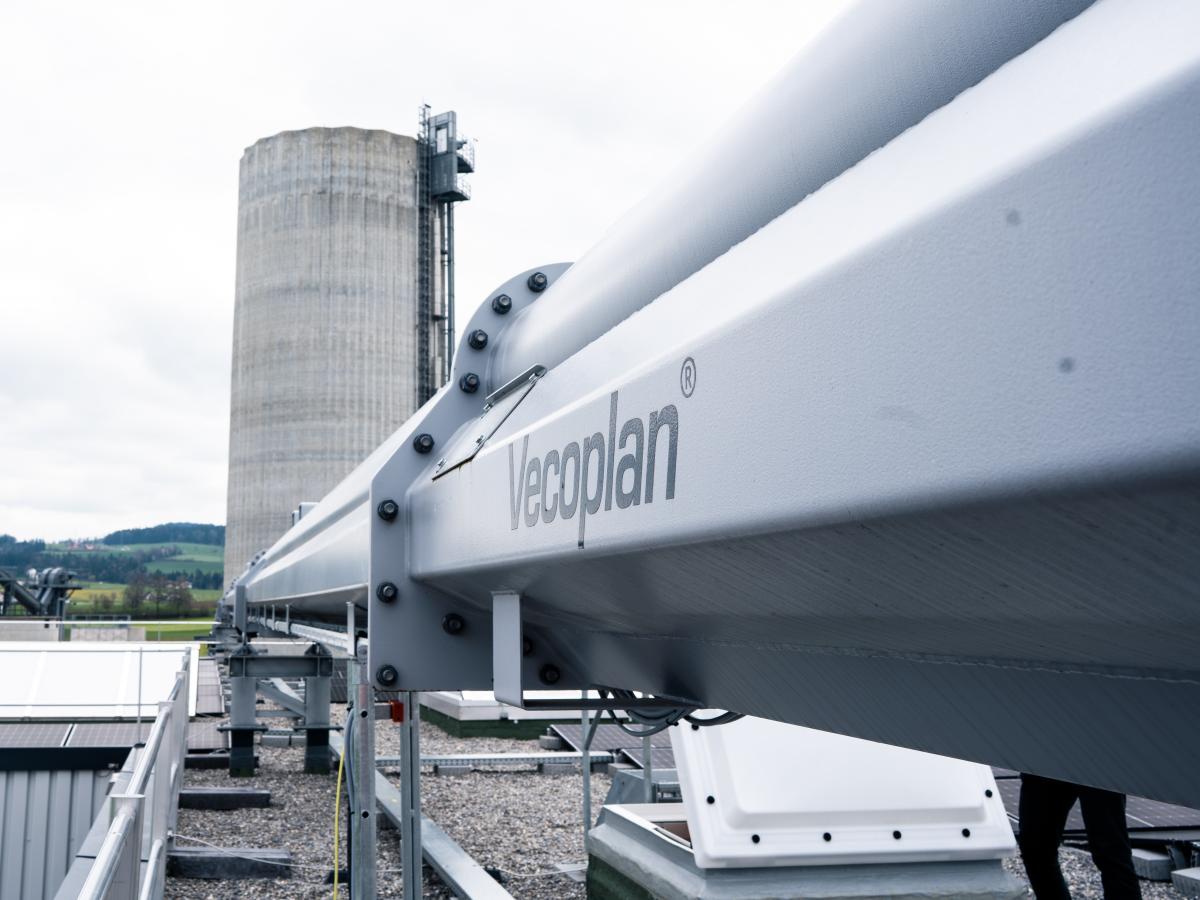
Outside the building, Vecoplan bottom-strand chain conveyors and pipe conveyors transport the processed material to the pellet facility in a dust-free procedure.
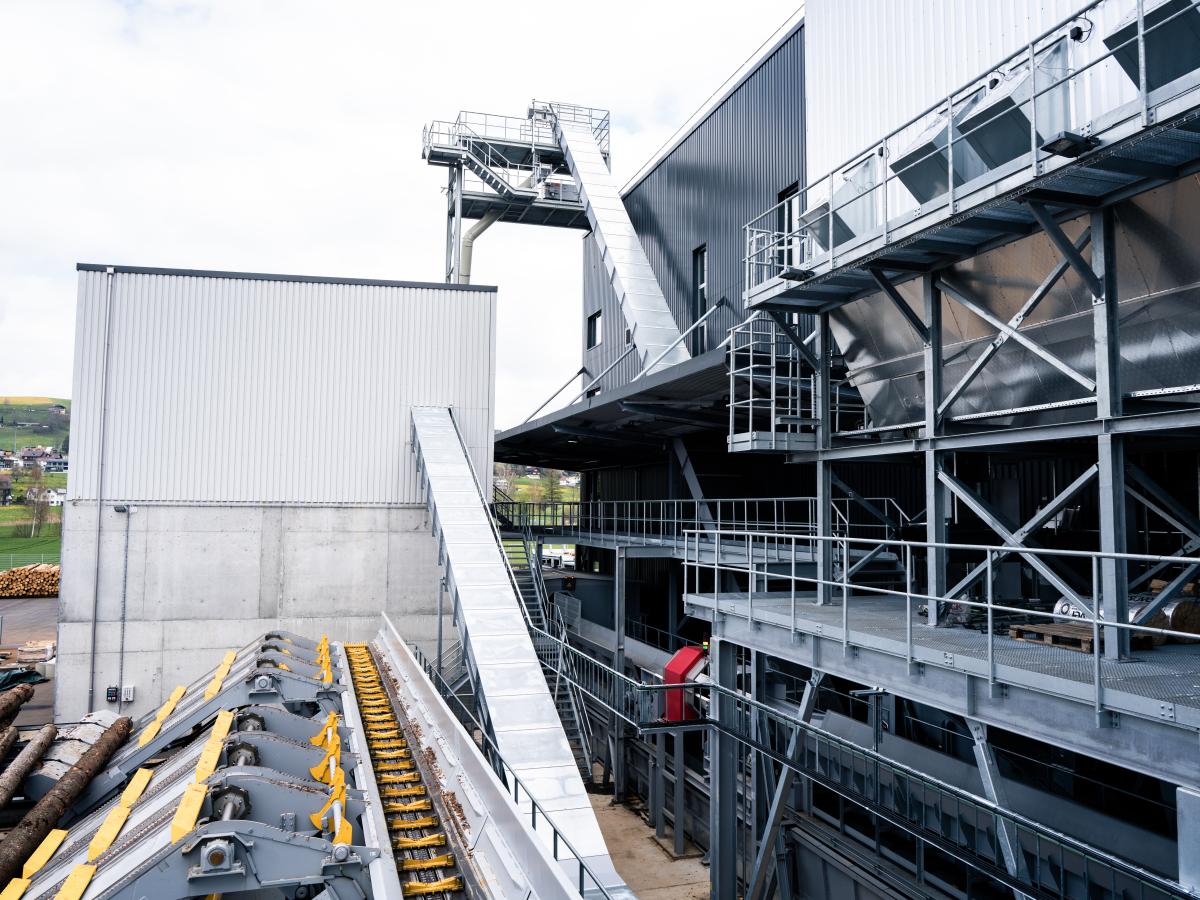
The waste bark collected in the box is also transported to the pellet facility.