„Unser Holz beziehen wir ausschließlich aus der Schweiz in einem Umkreis von etwa 100 Kilometern, und wir beliefern mit unseren Produkten auch nur den Schweizer Markt“, erzählt Roland Birrer. Die Tschopp Holzindustrie mit Sitz in Buttisholz im Kanton Luzern ist der einzige Hersteller im Land, der Schalungsplatten für die Bauindustrie fertigt. „Unser bestehendes Sägewerk haben wir seit 1999 in Betrieb. Es ist für 30.000 Kubikmeter Holz im Jahr ausgelegt. Aktuell verarbeiten wir bis zu 115.000 Kubikmeter“, ergänzt Birrer. Um diese Menge zu bewältigen, arbeitet Tschopp seit etwa zehn Jahren im Dreischichtbetrieb. Die Kapazitätsgrenze ist schon lange erreicht. Raum für neue Ideen, für neue Produkte? Keine Chance. Die logische Konsequenz, um weiter zu wachsen: Die Verantwortlichen entschlossen sich 2018 für den Bau eines neuen Sägewerks. Leiter ist Roland Birrer.
Kapazitätsgrenze deutlich erweitert
Im Mai 2023 geht die Anlage in Betrieb, nachdem die Techniker der Lieferanten und Partnerunternehmen über Wochen damit beschäftigt waren, in dem 123 Meter langen und 20 Meter hohen Neubau die installierten Anlagen in Betrieb zu nehmen. Der Geruch von frisch gesägtem Holz weht vom bestehenden Werk herüber, das nur wenige hundert Meter entfernt ist. „Wir haben unser neues Werk für 350.000 Festmeter Holz im Jahr ausgelegt. Damit ist auch genug Platz für die Fertigung neuer Holzwerkstoffe vorhanden“, erzählt Birrer zufrieden. Das sei bisher aus Kapazitäts- und Technologiegründen nicht möglich gewesen. Läuft das neue Werk, wird das alte nach und nach stillgelegt, so der Plan.
Die Tschopp Holzindustrie wurde als Zweimannbetrieb 1920 gegründet, heute arbeiten an allen Standorten verteilt 125 Mitarbeitende. Ronald und Daniel Tschopp sind die Inhaber und leiten die Firma in der dritten Generation. Die Schalungsplatten fertigt der Betrieb in allen Facetten. Eine Besonderheit sind die Versiegelungen auf den Längs- und Stirnkanten der Platten. Diese verhindern die Haftung von Betonrückständen und erleichtern die Reinigung. Zusätzlich erhöhen sie die Lebensdauer. „Dabei bieten wir nicht nur Qualität, sondern auch einen hohen Grad an Technologisierung. Dazu kommt das tiefe Fachwissen unseres Personals in unsere Produkte“, zählt Birrer die Erfolgsfaktoren auf.
Nichts geht verloren
Weil bei der Herstellung der Schalungsplatten jede Menge Abfälle entstehen – wie Späne, Sägemehl, Kappstücke und Rinde – besitzt Tschopp seit 2005 eine eigene Pelletproduktion, die das Unternehmen kontinuierlich ausgebaut hat. Heute fertigt es bis zu 120.000 Tonnen Pellets im Jahr. Seit 2014 steht auf dem Gelände auch ein eigenes Holzkraftwerk. „Wir können damit den gesamten Wärmebedarf für das Trocknen des Schnittholzes und für die Pellets abdecken“, resümiert der Werksleiter. „Die Restwärme nutzen wir, um umweltfreundlichen Strom zu produzieren.“ Im Jahr entstehen so rund 9,4 Millionen Kilowatt. Die Tschopp Holzindustrie verwertet den Rohstoff Holz am Standort damit zu hundert Prozent. Da der Betrieb im neuen Werk mehr Schnittholz verarbeiten wird, ist auch mehr Energie für das Trocknen erforderlich. Auf dem Grundstück ist genug Platz für ein weiteres Kraftwerk vorhanden.
Mit der richtigen Technik zum idealen Span
Um das Restholz für die Pelletproduktion und den Ökostrom aufzubereiten, setzt Tschopp auf Vecoplan. Der Spezialist mit Hauptsitz in Bad Marienberg im Westerwald entwickelt Anlagen, die Holz, Biomasse, Kunststoffe, Papier sowie Haus- und Gewerbeabfälle zerkleinern, fördern, separieren und lagern. „Wir beraten unsere Kunden, planen die Technik und finden gemeinsam die passende Lösung“, erklärt Michael Müller, der als Projektleiter den Schweizer Holzbetrieb betreut. „Zu unseren Aufgaben gehören natürlich auch ein ganzheitliches Projektmanagement sowie Montage, Inbetriebnahme und ein umfassender Service.“
Tschopp Holzindustrie arbeitet seit mehr als 30 Jahren mit den Anlagen der Westerwälder. Birrer: „Vecoplan hat einen guten Namen im Markt, und der Service passt einfach immer. Deshalb war für uns klar, dass wir die gute Zusammenarbeit fortsetzen.“ Der Maschinenbauer war von Anfang an in das Projekt eingebunden. Michael Müller und sein Team begleiteten die Schweizer bei der Planung und konnten im Zuge des Neuaufbaus die Anlagen auf der grünen Wiese errichten.
Der Vecoplan-Experte zeigt nach oben. „In der Etage über uns befinden sich die Sägelinien. Das Restholz fällt durch den Boden auf die Förderbänder.“ Auf diese Weise wird das Sägemehl auf mehreren Förderern zusammengeführt. Ein Sternsieb scheidet Überlängen ab. Abschnitte – oder auch Kopfscheiben genannt – fallen ebenfalls auf ein Förderband und werden einem Schredder der Baureihe VHZ 1600 zugeführt. Der robuste Ein-Wellen-Zerkleinerer ist modular aufgebaut und damit vielseitig einsetzbar. Vecoplan hat diverse Möglichkeiten, die für den Kunden passende Maschine zu konfigurieren. Dazu kann die zuständige Anwendungstechnik Komponenten wie Rotoren, Schneidkronen, Gegenmesser, Siebe und Antriebe an die jeweilige Aufgabe anpassen. Die so vorzerkleinerten Stücke werden dem Trommelhacker der Baureihe VTH 650 horizontal über eine Vibrorinne zugeführt. „Diese Anlage erreicht enorme Durchsatzleistungen“, sagt Müller. Durch das Zerkleinerungsprinzip wird das Restholz auf eine Hacklänge von etwa 15 Millimetern gehackt. Das Material passiert ein weiteres Sternsieb, das Überlängen aussondert. Es kann nun direkt dem Trocknungsprozess im Pelletwerk zugeführt werden.
Sauberer und leiser Transport
Das so aufbereitete Material kommt auf einen Steilförderer, der es zu einem Rohrgurtförderer der Baureihe VRF führt. Mit einer Länge von 140 Metern transportiert dieser das Schüttgut zu den nur wenige Meter entfernten Rohstoffhallen des Pelletwerks. Die rohrförmige und rundum geschlossene Bauweise des „Vecobelts“ schließt das Material komplett ein und schützt das Schüttgut so vor Windeinflüssen. Der Fördergurt bei dieser Baureihe läuft nicht auf Rollen wie bei herkömmlichen Förderanlagen. Der Gurt wird von einem Luftkissen getragen, sodass im Betrieb nur geringe Reibungsverluste auftreten. Er läuft dadurch auch leise, was zu einer angenehmeren Atmosphäre auf dem Betriebsgelände führt. Die Anlage fördert das Material mit einer maximalen Geschwindigkeit von 2,5 Metern in der Sekunde.
„Mit dem Rohrgurtförderer benötigt Tschopp für die Verladung des aufbereiteten Materials keine Lkw oder Radlader, ein Zwischentransport ist auch nicht erforderlich“, sagt Michael Müller. „Das spart Zeit, Platz und Energie.“ Tschopp nimmt zudem die alten Schalungsplatten seiner Kunden zurück. Diese werden geschreddert und ebenfalls ins Holzkraftwerk geführt.
Herausforderungen gemeistert
„Sicher hatten wir während der Bauphase bedingt durch die Corona-Krise immer wieder mit Herausforderungen zu kämpfen“, erzählt der Tschopp-Werksleiter. „Denn die Pandemie brachte die Lieferketten ganz schön durcheinander.“ Roland Birrer stand daher permanent im engen Kontakt mit der Baufirma und den Partner-Unternehmen. „Wir haben sie immer wieder dazu angehalten, ihr Material und die benötigten Komponenten frühzeitig zu bestellen. Der Einsatz hat sich gelohnt, denn am Ende mussten wir nie lange auf etwas warten.“ Die Lieferketten blieben über die komplette Projektdauer stabil – auch wenn hin und wieder ein Kraftakt nötig war. Dazu kamen die Marktveränderungen wie steigende Stahlpreise. Das löste regelmäßig Diskussionen aus.
Und genau deswegen gefiel dem Werksleiter die Zusammenarbeit mit Vecoplan. Roland Birrer: „Zum einen lieferte uns Vecoplan bewährte Technik, die hält, was sie verspricht und zum anderen funktionierte die Abwicklung durchweg konstruktiv. Michael Müller und sein Team brachten Ideen und Vorschläge ein. Und selbst, wenn wir mit der Planung schon fast am Ende waren, sie waren immer für Gespräche bereit, um eine Lösung auch ein zweites, drittes oder viertes Mal zu besprechen. Am Schluss hatten wir die für uns perfekte Aufbereitung.“
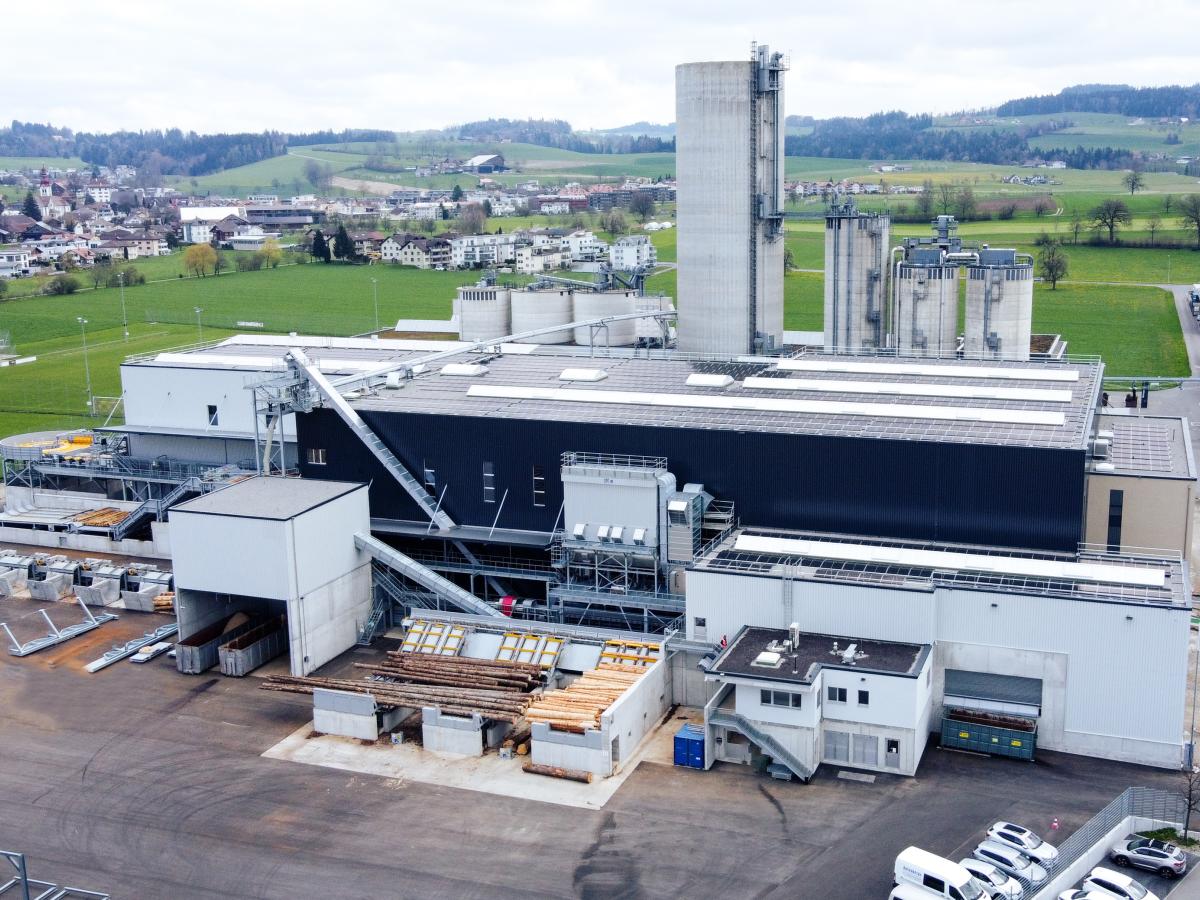
Der Neubau der Tschopp AG: Vecoplan lieferte Anlagen, um die Resthölzer der Sägewerkslinie zu entsorgen und aufzubereiten.
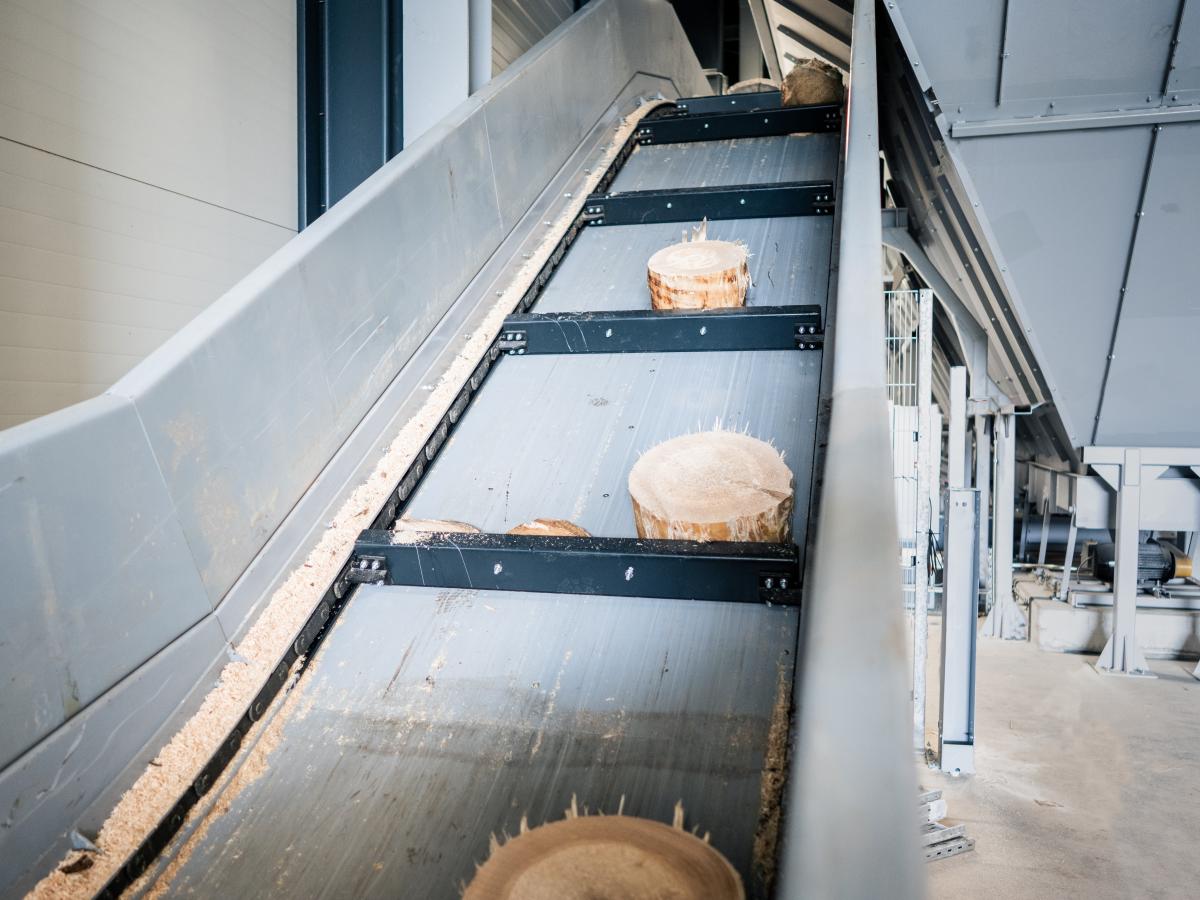
Die Förderanlage transportiert die Kappscheiben zum VHZ 1600 zur Vorzerkleinerung.
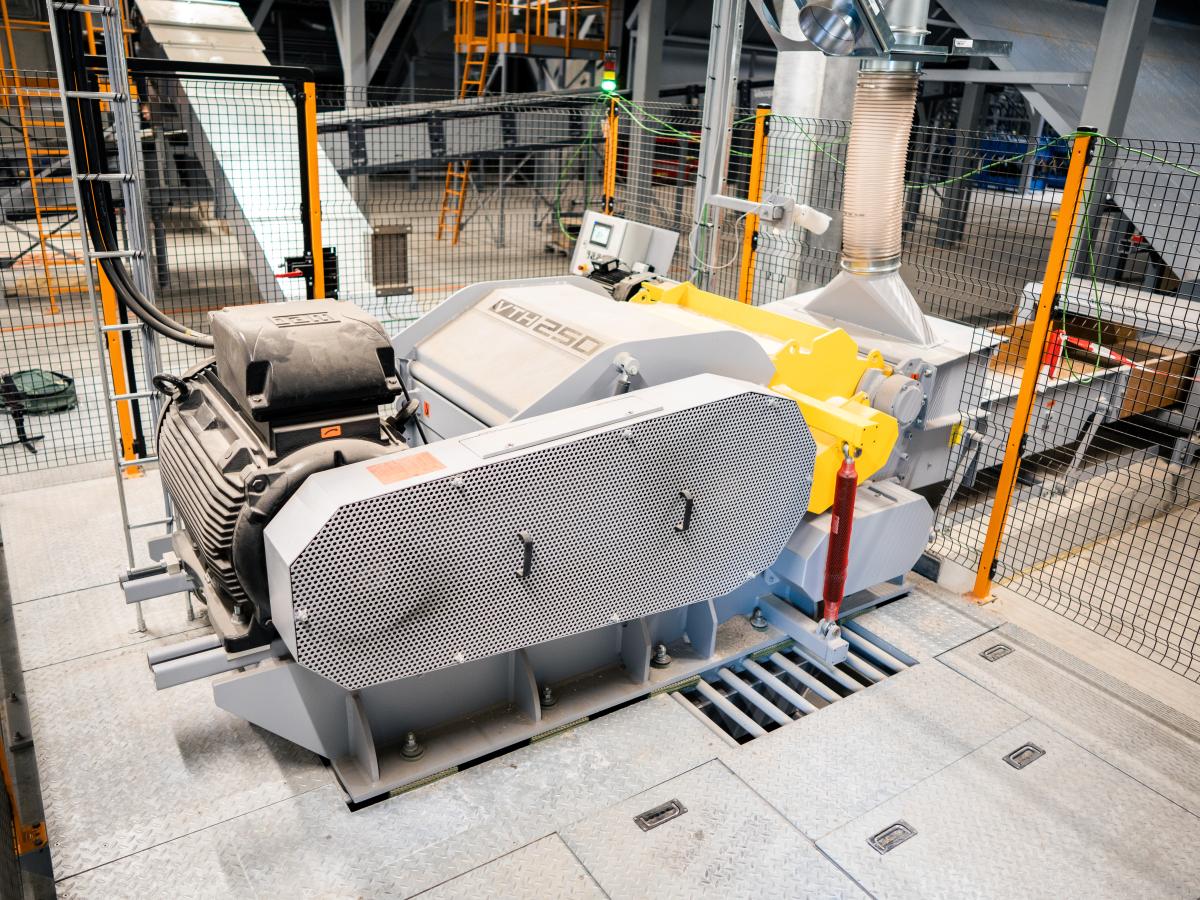
Der Trommelhacker reduziert das Restholz auf eine Hacklänge von maximal 15 Millimetern.
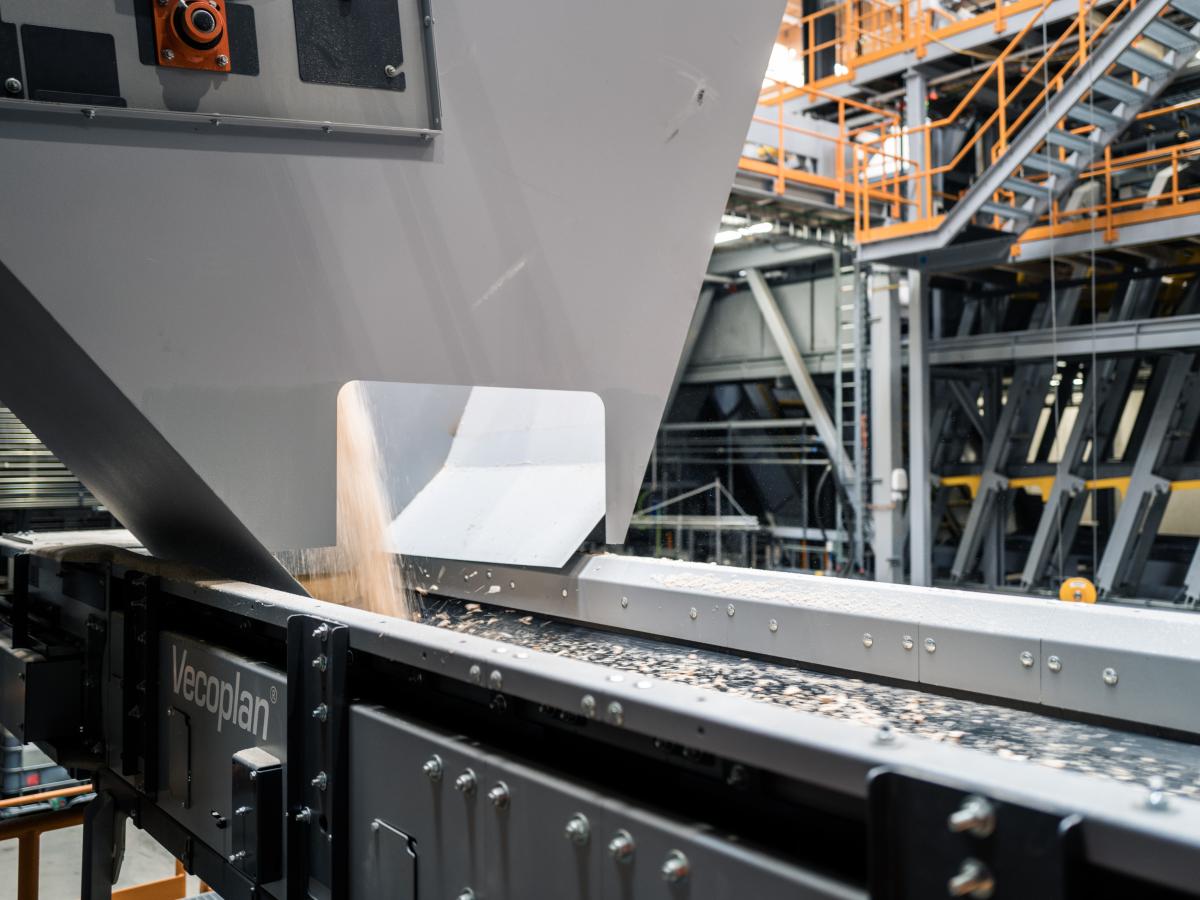
Die von Vecoplan installierte Fördertechnik transportiert das Material im Inneren der Entsorgungslinie kontinuierlich und sicher.
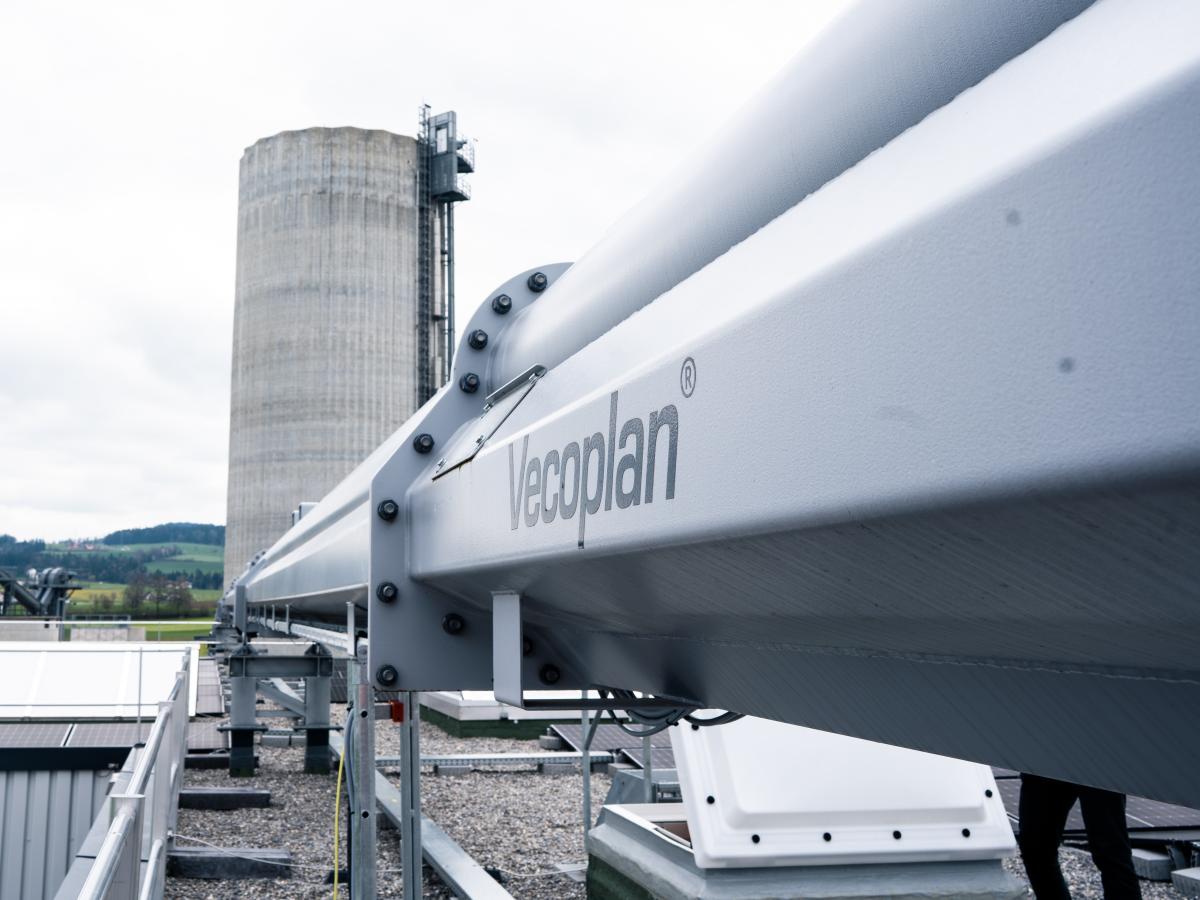
Außerhalb des Gebäudes sorgen Kratzketten- und Rohrgutförderer von Vecoplan für den staubfreien Transport des aufbereiteten Materials bis zum Pelletwerk.
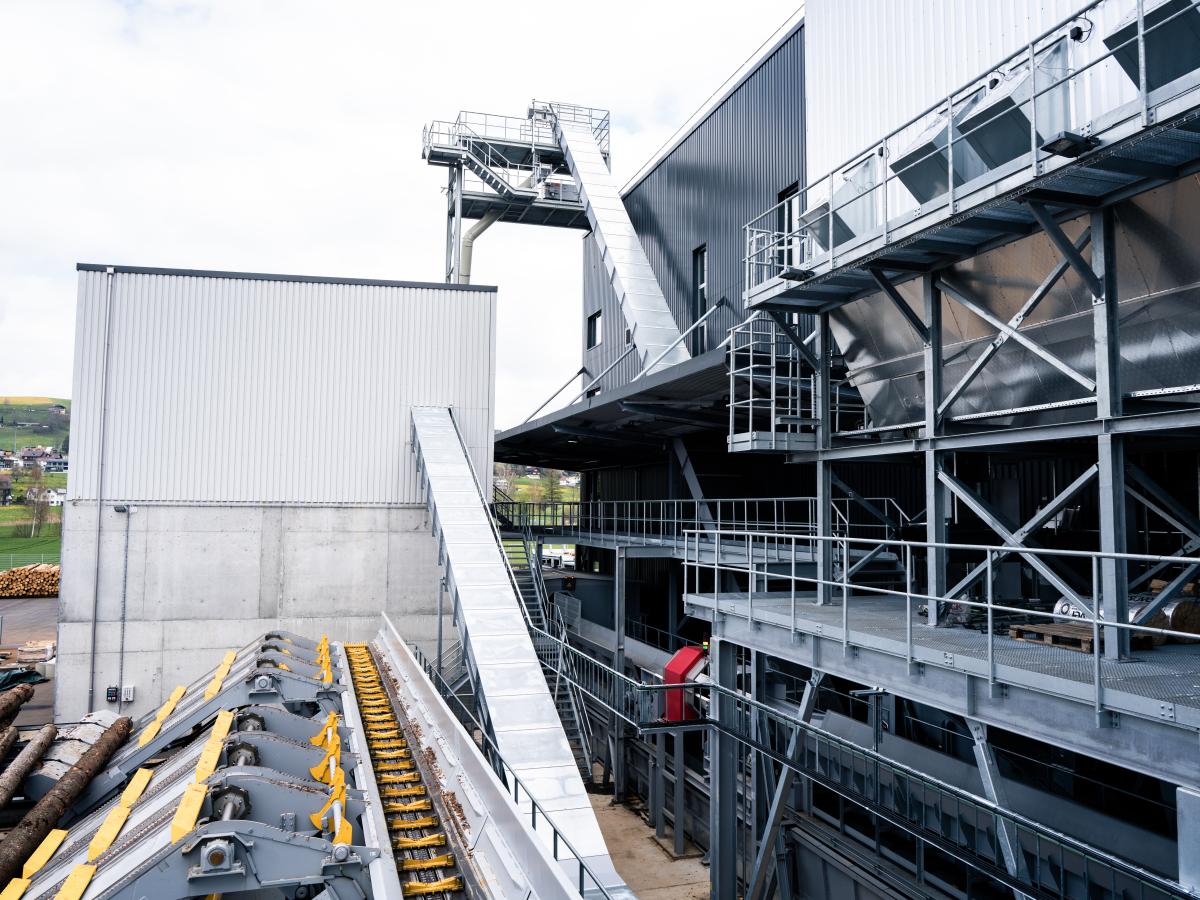
Die in der Box gesammelten Rindenabfälle werden ebenfalls zum Pelletwerk gefördert.