Basics
1. Mr. Beib, can you explain what makes the wood-based material CLT so special for the construction industry?
Cross-laminated timber is exceptionally stable, and its high strength is impressive. Building with CLT is more ecologically sustainable and progressive than using materials such as concrete and steel, which have been mainly used in the past decades. CLT is also ideal for constructing multi-storey buildings thanks to its high strength. In Scandinavia, buildings with total heights approaching 100 metres are already being constructed using CLT. This is not yet possible in other European countries due to regulatory requirements for using cross-laminated timber. Within the EU countries, these requirements are handled differently – and even in Germany, this differs from region to region. A maximum of four stories is permitted in timber construction with CLT. It’s foreseeable that this will change as sustainable wood construction becomes more popular and is promoted by more and more governments.
2. How is the material constructed, and why is it so stable?
CLT consists of several solid wood layers glued together crosswise at a 90-degree angle and compressed under high pressure. The result is a material with a low density and amazingly high degrees of strength and static stability, so it can effectively replace steel and concrete in the construction of houses. For example, it’s suitable for the construction of floor slabs, interior & exterior walls and roofs, and its density also makes it relatively easy to handle.
3. Is cross-laminated timber more expensive than the other two materials?
Yes, CLT is still comparatively expensive. No one can look into a crystal ball and predict exact developments, but it’s likely that this will change in the coming years and that CLT prices will align with those of materials such as concrete and steel. This is because the requirements for sustainable construction are still increasing, and the technology in producing CLT and precast elements for house construction is constantly developing.
Preparation
4. The residual materials generated during the production of CLT house construction elements can be used for energy and heat recovery. How challenging is it to prepare them for that?
As long as the material is not glued, the residual wood consists of chips or board cuttings, as seen in sawmills. These can be processed using the classic methods. We offer proven solutions here, such as our drum chippers and a wide range of conveyor systems. However, the process is more difficult when you have to deal with finished components. For example, the dimensions are very large. Window or door cutouts can measure up to two-by-two metres in length and width and have thicknesses up to 360 millimetres.
Then you also have the very high strength of the glued CLT. Conventional sawmill shredding lines can’t handle the CLT elements at all, so we use our expertise and technology from our Recycling | Waste division for this special material – with the high-performance shredder of the VAZ series, for instance.
This single-shaft, slow-running machine can shred these solid, large-sized, and relatively strong residual timbers. Grain sizes smaller than 20 millimetres can be achieved in one single-stage process. The plant operator can use the shredded material for thermal recycling, but he can also use it to produce briquettes or pellets. It’s type-sorted, free of extraneous materials and dry.
5. Your customers include the Finnish-Swedish group Stora-Enso. To handle this large-format CLT production waste, the company needed a processing line for its new plant in the Czech Republic. How did you realise this for Stora-Enso?
We installed our VAZ 1600 series shredder. This machine gives us various configuration options. For example, we can fit vibration dampers to absorb the immense vibrations that occur when CLT is shredded. Normally, we use dampers for usage scenarios in our recycling division. The rotor is fitted with cutting crowns and matched in size to the required end product and the selected screen perforation. The rotor jacket can be hardfaced if necessary. This reduces the wear from mechanical abrasion. We have specially armoured, 60 by 60 millimetre cutting tips on the rotor, providing much greater stability – and we use our powerful HiTorc direct drive. This purely electric drive solution is extremely efficient. A ratchet coupling is also installed to protect against extraneous materials: The machine stops immediately if any foreign body gets into it. There’s also a screen with a very small hole diameter. The VAZ single-stage shredding eliminates the need for pre- and post-processing.
The large-format remnants are fed in via a conveyor belt or a crane. We positioned a tilting hopper upstream to feed the machine with the CLT pieces. The hopper is raised or lowered depending on the filling level.
6. Does Vecoplan support other customers who process waste wood from the production of CLT elements, and if so, what are the requirements?
Yes, we’ve delivered solutions for CLT reprocessing to several customers. And the number of customers is growing. We’ve already installed a number of plants in various European countries. The requirements are all very similar: the shredding of large-sized, high-strength components. The differences are mostly only in the required throughput capacity. This is because some operators produce 100 residential units in one period, for example, while others produce only 20 in the same time. To supply them with the right solution, we equip our shredders with larger or smaller drives as required – or we select the machine to match the requirements.
One plant with a wide range of Vecoplan equipment is used by our customer Mayr-Melnhof Holz GmbH in Leoben, Austria. In addition to several conveyor systems and components for separation, the company integrated various shredders for the disposal and processing of waste wood from CLT production: a biomass chipper, a VAZ 2500 shredder and a hammer mill. Mayr-Melnhof officially opened its ultramodern, energy-efficient plant in June 2023. It uses the output material to produce high-quality pellets.
Another company, Holzwerke van Roje, which is based near our main site in Bad Marienberg, has added CLT to its range of products. In 2022 we supplied the company with a disposal line, including a drum chipper and various conveyor systems. Van Roje also recycles its production waste to produce pellets.
Outlook
7. In your opinion, is CLT being used more and more?
Definitely. There are several studies on this. Some say that global CLT production will increase by an average of 15 per cent annually in the coming years, while others believe that volumes will increase three to four times by 2040 compared to the current demand. There are many reasons for this, most of which we’ve mentioned earlier. First and foremost, it’s about the requirements for sustainable construction. It can be assumed that the authorities will approve increasingly higher construction methods using this material in the medium term. At least that’s what the forecasts say – and because the demand is increasing, more and more plants are being built. We’re very optimistic about this development.
8. Will you continue to develop your solutions in this direction?
The market is constantly presenting us with new challenges. We already know this from the past. In the future, even smaller particles may have to be produced when shredding CLT. Then the machines will have to be protected from dust and the danger of explosions. We’re continuously making our plants more energy-efficient. Confronting these challenges is a top priority. This is the only way to move forward.
At Vecoplan, we can adapt solutions from other industries to the respective usage scenario, such as recycling – without having to pay for the learning process. That’s also what makes us so competitive – or even better, it sets us apart from many of our market competitors. This enables us to find the right technique, even for materials that are very difficult to handle, such as CLT.
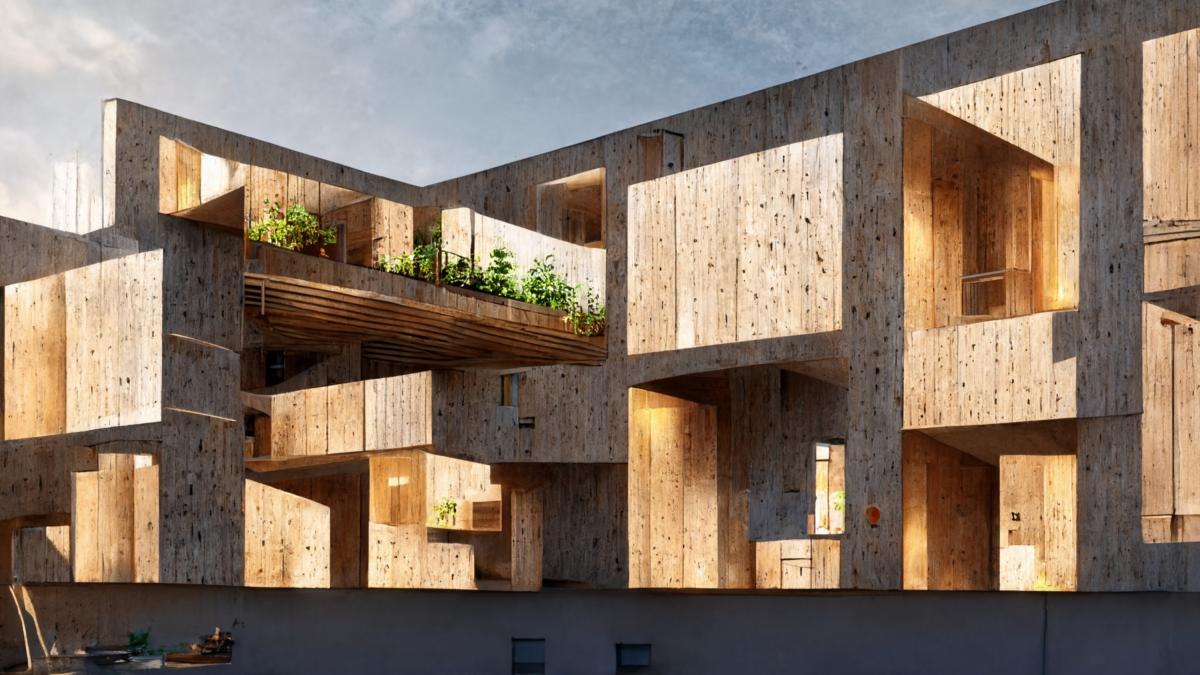
Cross-laminated timber (CLT) can be used to construct entire house walls. The solid production waste can be processed for reuse as fuel using Vecoplan technology.
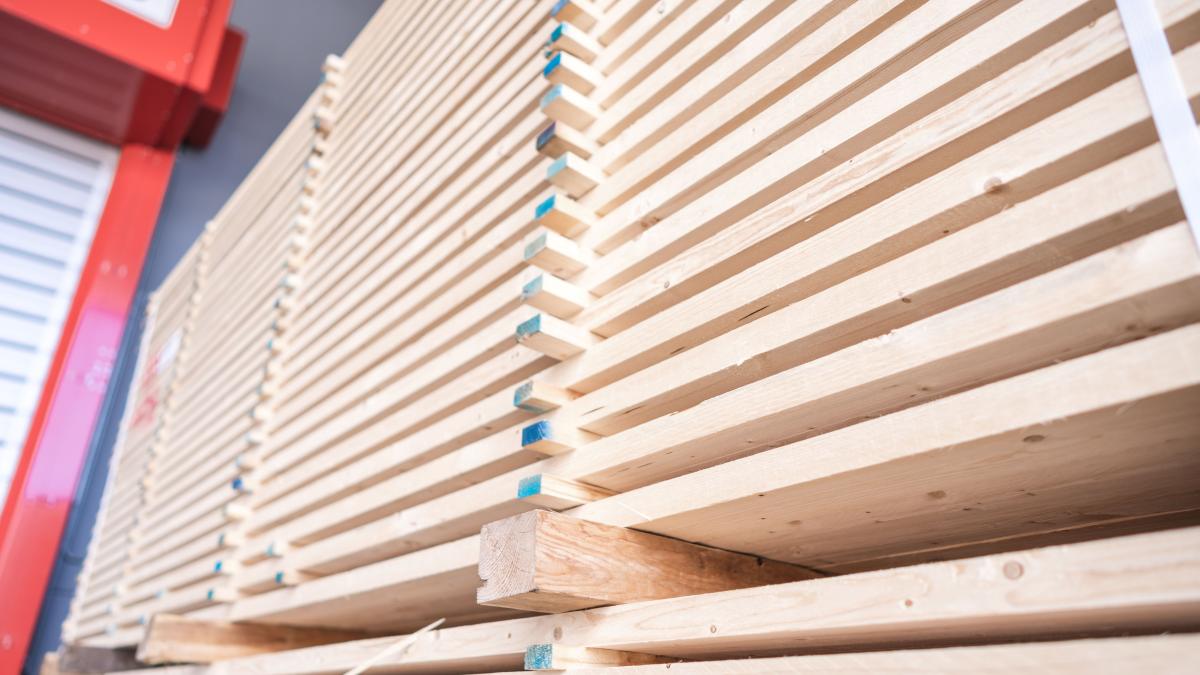
To achieve CLT’s enormous strength and high stability, several solid wood layers are glued crosswise at a 90-degree angle and compressed under pressure.
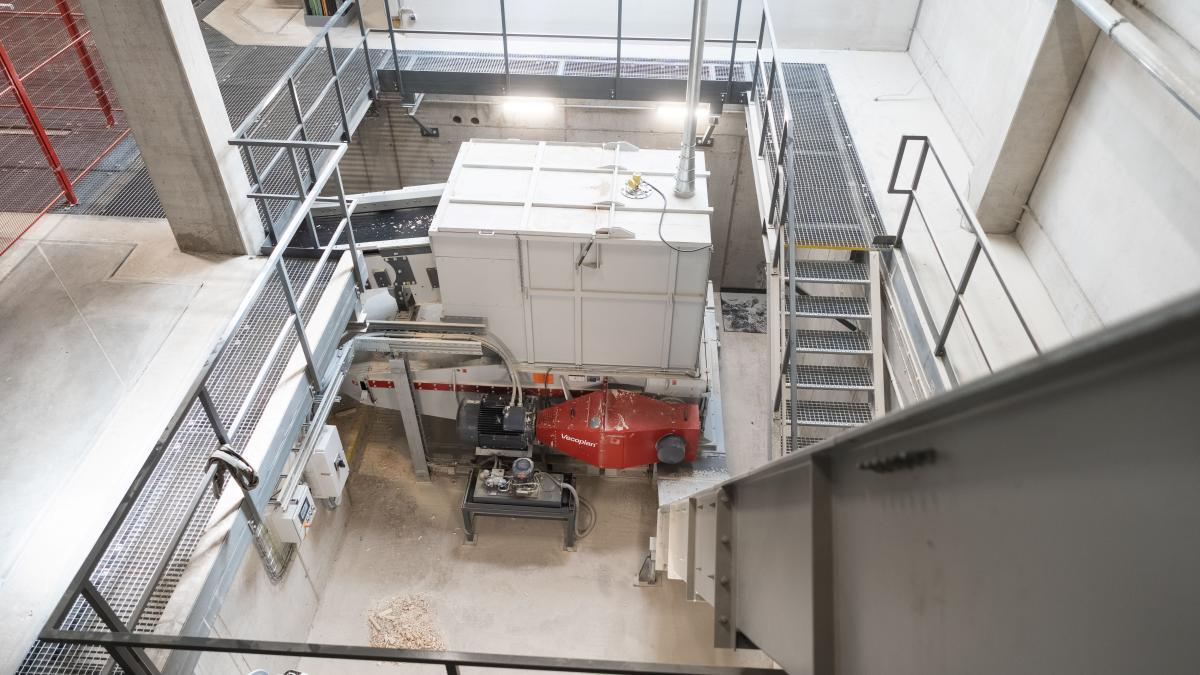
The robust and reliable VAZ 1600 single-shaft shredder has been equipped with several special features and integrated into the processing line.
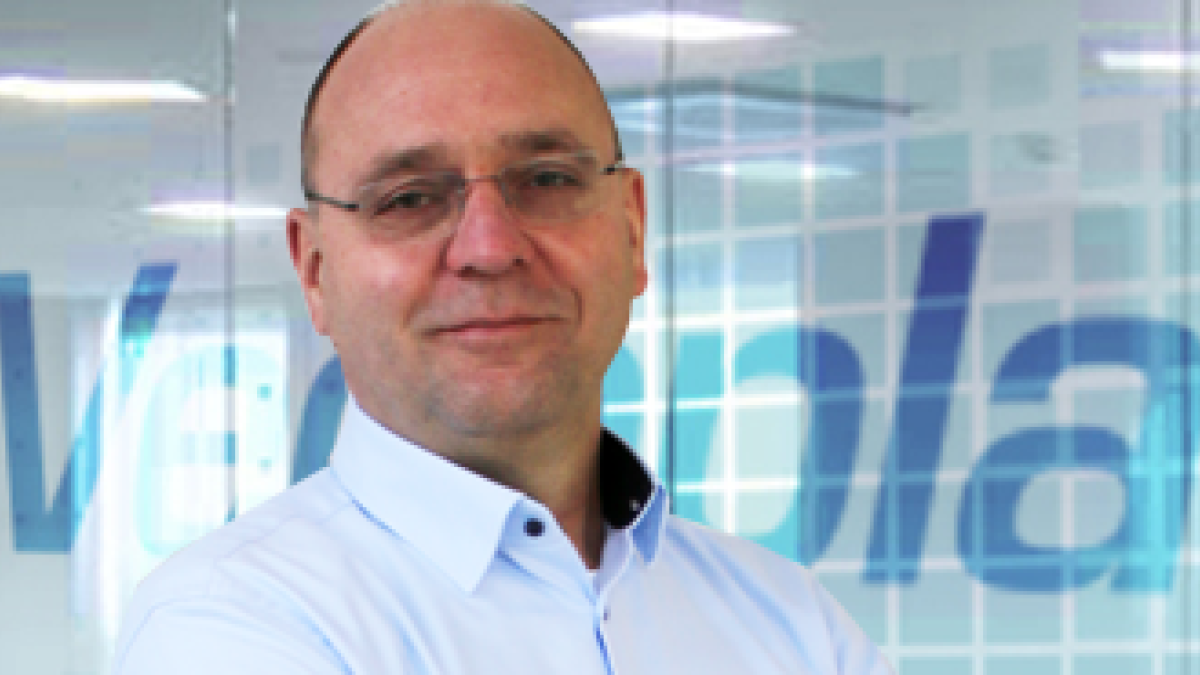
Kersten Beib: “Our big advantage at Vecoplan is that we can adapt solutions from other industries for a specific usage scenario.”