„Vieles, was Mitarbeitende bisher an Maschinen mechanisch einstellen mussten, lässt sich heute automatisch ausführen“, sagt Paul Mockenhaupt, Elektroentwickler für Digitalisierung bei Vecoplan. „Um Kunden bei ihren Prozessen noch besser zu unterstützen, wird es für uns immer wichtiger, Maschinen mit Intelligenz auszustatten.“ Mit diesem Anspruch entwickelt Paul Mockenhaupt mit seinem Team technische Features, die Zerkleinerungsprozesse immer weiter optimieren. Zu diesen Neuentwicklungen gehört zum Beispiel ein elektrisch angetriebener Schieber.
Elektrisch = energieeffizient
„Unseren neuen, elektrisch angetriebenen Schieber haben wir mit hochdynamischen Kugelgewindetrieben ausgestattet“, erläutert der Vecoplan-Entwickler. „Weil dieser einen sehr guten Wirkungsgrad erreicht, profitiert der Betreiber von einer äußerst energieeffizienten Komponente.“ Elektrik statt Hydraulik – damit ist auch kein Öl erforderlich, das das Output-Material kontaminieren könnte. Ein Aspekt, der für viele Abnehmer immer wichtiger wird. Ein weiterer Punkt ist die robuste Bauweise. Denn durch den Elektroantrieb sind weniger mechanische Teile verbaut. Damit verringert sich auch der Verschleiß.
„Im Vergleich zu einem hydraulischen Schieber lässt sich unsere neue Lösung besser steuern. Damit kann der Anwender das Drehmoment, also den Druck, der auf das Material ausgeübt wird, sehr genau einstellen“, sagt Mockenhaupt. Der elektrische Schieber bewegt den Input dadurch kontinuierlich in Richtung des auf der Welle liegenden Rotors. Die neue Variante arbeitet zudem dynamischer und damit schneller, was sich positiv auf den Durchsatz auswirkt.
Der leistungsstarke Direktantrieb
Damit der Zerkleinerungsprozess auch bei steigendem Durchsatz kontinuierlich ökonomisch bleibt, stattet Vecoplan seine Schredder optional mit dem HiTorc aus, ein wirtschaftlicher und funktionsstarker Direktantrieb. „Die im Frequenzumrichter integrierte Regelung stellt unter anderem sicher, dass zu jeder Zeit und in jedem Betriebszustand das optimale Drehmoment an der Rotorwelle anliegt“, beschreibt Mockenhaupt. Das macht den Antrieb nicht nur äußerst energieeffizient. Weil bei dieser rein elektrischen Lösung Komponenten wie Kupplungen, Riemenantriebe oder Schwungscheiben wegfallen, reduziert dies auch den Wartungsaufwand erheblich. „Weniger mechanische Komponenten bedeuten auch deutlich geringere Massenträgheitsmomente im gesamten Antriebssystem“, erläutert Mockenhaupt. „Das hohe verfügbare Drehmoment ermöglicht so einen schnellen Anlauf unter Last, also auch bei gefülltem Zerkleinerungsbereich.“
Die vollautomatisierte Steuerung erkennt durch die kontinuierliche Drehzahlanalyse und die Stromauswertung frühzeitig eine Überlastung der Maschine im laufenden Zerkleinerungsprozess. Bei Störstoffen stoppt die Rotorwelle in wenigen Millisekunden. Dadurch lassen sich Schäden an wichtigen Bauteilen vermeiden. Nach einem kurzen Gegenlauf dreht der Vecoplan-Antrieb in wenigen Sekunden wieder in die geforderte Richtung. Der Synchronmotor überzeugt zudem mit seinem Wirkungsgrad: Im Vergleich zu anderen elektromechanischen Antrieben können Kunden mit den so ausgerüsteten Zerkleinerern bis zu 40 Prozent Energie einsparen, im Vergleich mit hydraulischen Antrieben sogar bis zu 60 Prozent.
Störstoffe intelligent erkennen
Zu den neuen Features gehört auch eine intelligente, schwingungsbasierte Störstoff-Erkennung. Damit kann Vecoplan auf das Kundenmaterial noch gezielter eingehen und konsequent Maschinenschäden vermeiden. Dem Betreiber steht ein bedienerfreundlicher Einmessvorgang zur Verfügung. „Unsere Lösung ist selbstlernend“, betont der Vecoplan-Experte. Startet der Zerkleinerer, nehmen Sensoren alle wichtigen Informationen auf, etwa die Material-Eigenschaften, die Schneidstoffe oder die Schneidgeometrie. Damit passt sich die Störstofferkennung an die gewünschte Sensibilität des jeweiligen Inputs und die Umgebungsbedingungen an. Diese Aufgabe musste der Bediener bisher manuell lösen, was Zeit kostet. Werden die Einstellungen verändert, ist lediglich das Rezept zu wechseln. Das funktioniert auch aus der Ferne. „Mit unserer neuen Störstoff-Erkennung erhält der Betreiber nicht nur einen robusten Zerkleinerer. Die Maschine erkennt auf Wunsch auch jeden kleinen Stein und stoppt sofort, ohne dass der Bediener eingreifen muss“, sagt Mockenhaupt. „Um zu beurteilen, wie der Schredder performt, bekommen wir mit diesem nützlichen Feature über die Sensoren ein Daten-Feedback von der Zerkleinerung und können bei Bedarf den Prozess optimieren.“ Vecoplan rüstet auf Wunsch des Kunden auch bestehende Anlagen mit der neuen intelligenten Störstofferkennung nach.
Schnell zum idealen Schnittspalt
Neu im Programm ist auch die automatische Gegenmesser-Einstellung. „In der Regel muss der Bediener in jeder Schicht die Gegenmesser am Schredder manuell nachjustieren, um den geforderten Schnittspalt zu erhalten, weil sich dieser im Betrieb verstellen kann“, berichtet Mockenhaupt. Ist der Schnittspalt zu groß, benötigt die Maschine mehr Energie, weil das Material weniger geschnitten als vielmehr in den Spalt gequetscht wird. Damit weist der Output meist auch nicht das gewünschte Ergebnis auf. Für die manuelle Verstellung benötigt der Mensch an der Maschine zwischen 15 und 30 Minuten. „Unsere automatische Lösung verringert den Zeitaufwand um den Faktor zehn – ohne dass der Bediener eingreifen muss“, sagt Mockenhaupt.
Sobald der Zerkleinerer leer gefahren ist, stellt das Feature die Gegenmesser automatisch korrekt ein. Damit unterstützt diese Lösung die Kunden, ihre Maschineneffizienz und so die Performance über den ganzen Tag aufrecht zu erhalten. Das zeigt sich auch an der konstanten Qualität des Outputs. Der Schredder arbeitet aber nicht nur energieeffizienter, ebenso sinkt der Verschleiß deutlich, was sich auf die Lebensdauer der Maschine auswirkt. „Das richtige manuelle Einstellen der Gegenmesser erfordert zudem einiges an Know-how und das nötige Gefühl vom Bediener“, weiß der Vecoplan-Experte. „Unsere automatischen Gegenmesser sind ein echter Gamechanger. Denn sie stellen den Abstand exakt und wiederholgenau ein, unabhängig vom Kenntnisstand des Mitarbeiters.“
Cool bleiben mit Minimalmengenkühlung
Thermisch empfindliche Kunststoffe können durch den Wärmeeintrag beim Schreddern am Rotor plastifizieren. Der Betreiber erhält damit nicht die geforderte Output-Qualität. Mit Kühlwasser lässt sich dies verhindern. Allerdings ist die richtige Menge entscheidend, da sich ein zu hoher Wasseranteil ansonsten negativ auf die Nachfolgeprozesse auswirken kann. Vecoplan hat deshalb eine Minimalmengenkühlung entwickelt. „Wir können die Menge der Kühlflüssigkeit individuell einstellen, indem wir die Temperatur des Materials messen“, erklärt Mockenhaupt. „Mit Hilfe dieser einstellbaren Temperaturgrenzen sind wir in der Lage, die Wasserzuführung exakt zu regeln.“ Die Flüssigkeit wird in Wasserdampf umgewandelt und so abgeführt. Wechselt der Betreiber das Material, muss er nicht in die Maschine eingreifen, sondern nur das Rezept wechseln. Über die einstellbaren Temperaturgrenzen ist der Anwender bei den zu verarbeitenden Werkstoffen sehr flexibel. Der Kunde selbst muss lediglich einen Wasseranschluss zur Verfügung stellen, hochpreisige Zusatzaggregate sind nicht erforderlich. Über das Digitalisierungskonzept Vecoplan Smart Center (VSC) kann der Betreiber unter anderem Betriebskosten überwachen und aufzeichnen.
„Mit unseren neuen technischen Features unterstützen wir unsere Kunden in der Zerkleinerungstechnik nun noch besser“, resümiert Paul Mockenhaupt. „Denn aufgrund der Intelligenz der Komponenten ist die Performance einer Maschine nicht mehr vom Know-how des Bedieners abhängig, sondern lässt sich exakt und reproduzierbar einstellen.“ Das vermeidet Fehler und spart Zeit. „Unser Ziel ist es, unsere Kunden bestmöglich zu unterstützen.“
Die neue Störstofferkennung von Vecoplan ist ein selbstlernendes System. Startet der Zerkleinerer, nehmen Sensoren alle wichtigen Informationen auf, etwa die Material-Eigenschaften, die Schneidstoffe oder die Schneidgeometrie. Damit passt sich die Störstofferkennung an die gewünschte Sensibilität des jeweiligen Inputs und die Umgebungsbedingungen an. Diese Aufgabe musste der Bediener bisher manuell lösen, was Zeit kostet.
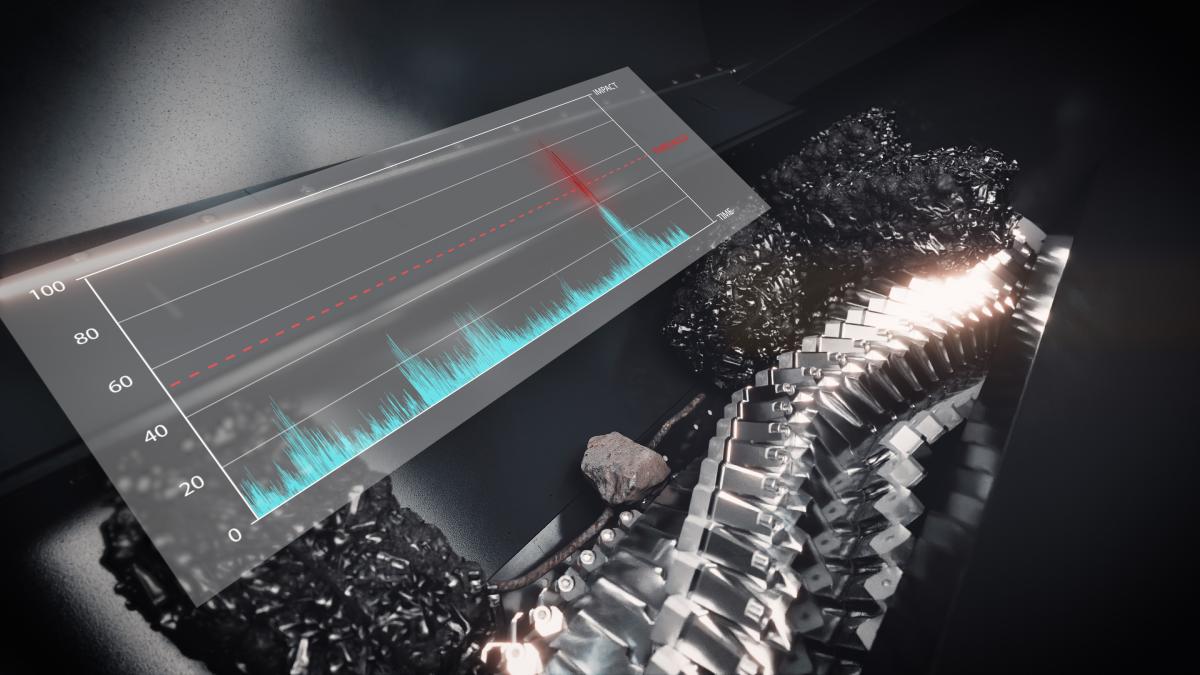
Die neue Störstofferkennung ist nur eines der vielen neuen Features, mit denen Vecoplan die Zerkleinerungsprozesse der Kunden effizienter gestaltet.